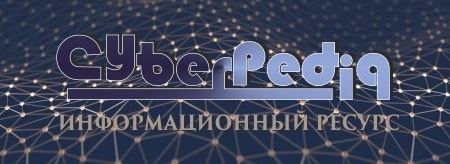
Адаптации растений и животных к жизни в горах: Большое значение для жизни организмов в горах имеют степень расчленения, крутизна и экспозиционные различия склонов...
Папиллярные узоры пальцев рук - маркер спортивных способностей: дерматоглифические признаки формируются на 3-5 месяце беременности, не изменяются в течение жизни...
Топ:
Характеристика АТП и сварочно-жестяницкого участка: Транспорт в настоящее время является одной из важнейших отраслей народного хозяйства...
Характеристика АТП и сварочно-жестяницкого участка: Транспорт в настоящее время является одной из важнейших отраслей народного...
Комплексной системы оценки состояния охраны труда на производственном объекте (КСОТ-П): Цели и задачи Комплексной системы оценки состояния охраны труда и определению факторов рисков по охране труда...
Интересное:
Что нужно делать при лейкемии: Прежде всего, необходимо выяснить, не страдаете ли вы каким-либо душевным недугом...
Распространение рака на другие отдаленные от желудка органы: Характерных симптомов рака желудка не существует. Выраженные симптомы появляются, когда опухоль...
Лечение прогрессирующих форм рака: Одним из наиболее важных достижений экспериментальной химиотерапии опухолей, начатой в 60-х и реализованной в 70-х годах, является...
Дисциплины:
![]() |
![]() |
5.00
из
|
Заказать работу |
|
|
В цеху на участке внепечной обработки стали расположены две установки «ковш-печь» (рисунок 19) для обработки металла после выпуска из электропечи.
1 - металловозная тележка; 2 - сталеразливочный ковш; 3 - трансформатор стенда электродугового нагрева; 4 - крышка стенда электродугового нагрева; 5 - бункер для подачи ферросплавов и лигатур; 6 - дозирующие весы; 7 - бункера ферросплавов и лигатур; 8 - пульт управления
Рисунок 19 – Схема установки «ковш-печь»
В состав участка ковш-печь (УКП) № 1А входят:
− две независимые позиции обработки оборудованные водоохлаждаемыми сводовыми крышками;
− оборудование для индивидуальной обработки расплава с продувочными устройствами, подачей легирующих добавок;
− четыре двухручьевых трайб-аппарата для ввода проволоки, по два на каждой позиции обработки;
− поворотный портал для поворота графитированных электродов и создающий возможность нагрева плавки в обеих позициях обработки.
УКП имеет следующие вспомогательные устройства:
− манипулятор для измерения температуры и отбора проб металла;
− аварийная фурма для продувки металла инертным газом (при отказе продувочных пробок установленных в днище);
− сталевозы;
− система газоотсоса.
− стенд для навинчивания электродов и площадка для их хранения;
− стенд для перепуска и выравнивания графитированных электродов.
В состав УКП №2 входят:
− две независимые позиции обработки оборудованные поворотным порталом для поворота одновременно с графитированными электродами, водоохлаждаемой сводовой крышкой, создающей возможность нагрева плавки в обеих позициях обработки.
− оборудование для индивидуальной обработки расплава с продувочными устройствами, подачей легирующих добавок и два четырехручьевых трайб-аппарата для ввода проволоки по одному на каждой позиции обработки.
|
УКП №2 имеет следующие вспомогательные устройства:
− манипулятор с нефутерованной (расходуемой) металлической трубкой для вдувания углеродосодержащих материалов (кокс) в металл;
− система газоотсоса;
− стенд для навинчивания электродов и их хранения;
− стенд для перепуска и выравнивания графитированных электродов;
− стенд сталеразливочного ковша (2 шт).
Перед началом работы на установке первый подручный сталевара проверяет наличие расходуемых материалов в бункерах и на рабочей площадке обеих позиций. После простоя установки свыше 8 часов и после выполнения каких-либо ремонтных работ производят холодное опробование установки перед подачей ковша под плавку в следующем порядке:
1) опускают крышку;
2) проверяют наличие напряжения;
3) включают разъединитель;
4) устанавливают органы управления перемещением электродов в положение «Автомат»;
5) включают вакуумный выключатель и убеждаются в том, что электроды начали движение вниз;
6) выключают вакуумный выключатель;
7) поднимают электроды;
8) поднимают крышку;
9) устанавливают сталевоз в положение «Установка ковша».
Температура футеровки ковша подаваемого под плавку должна быть не менее 900ºС (красного или малинового цвета). Рекомендуемый оборот ковша должен быть не более 3 ч.
Рекомендуемая продолжительность от конца выпуска до начала обработки металла на установке «ковш-печь» не должна превышать 30 мин. Температура металла в ковше перед началом обработки на УКП должна быть не менее 1530ºС. Выпуск металла из печи производить с присадкой в ковш во время выпуска шлакообразующих материалов:
− при отсутствии продувки аргоном – от 300 до 450 кг извести и от 50 до 100 кг плавикового шпата (или глиноземсодержащего материала);
− при наличии продувки аргоном – от 600 до 800 кг извести и от 100 до 200 кг плавикового шпата (или глиноземсодержащего материала).
|
Продолжительность усреднительной продувки должна быть от 3 до 5 мин. При проведении продувки металла инертным газом во время выпуска из электропечи усреднительную продувку допускается проводить в течение от 2 до 3 мин с последующим отбором пробы металла №1.
В качестве шлакообразующих материалов используют свежеобожженную известь, плавиковый шпат, глиноземсодержащий материал.
Обработка металла на УКП преследует следующие задачи:
− корректировка и усреднение металла по температуре;
− корректировка и усреднение металла по химическому составу;
− десульфурация металла;
− рафинирование металла от вредных примесей;
− согласование работы печей и МНЛЗ.
При подаче аргона на пробку кратковременно устанавливают максимальный расход аргона («байпасом») для «пробивания» продувочного блока. После запуска пробки устанавливают необходимый расход аргона для ведения процесса. Регулирование объёмного расхода аргона производят, не допуская сильного оголения металла в районе продувочного пятна и бросков тока по фазам. Диаметр пятна не должен превышать значений от 20 до 30 см (определяется визуально). Обязательной является продувка в течение 1,0 мин перед измерением температуры после отключения токовой нагрузки. Визуальный контроль продувки рекомендуется производить каждые 5-10 мин, особенно при работе на высоких ступенях нагрева.
Ступень нагрева выбирают исходя из требуемой скорости нагрева металла. Скорость нагрева определяется также массой и состоянием шлака, интенсивностью продувки аргоном, состоянием ковша и массой добавок.
Разрешается при отказе донной продувки производить дуговой нагрев продолжительностью не более 10 мин на пониженных ступенях (для УКП № 1А – не более 8 ступени, для УКП №2 – не более 5 ступени) с одновременным вводом шлакообразующих материалов.
Во избежание насыщения стали углеродом и азотом, рекомендуется в период наведения шлака (до отдачи не менее 800 кг извести и 300 кг плавикового шпата) дуговой подогрев производить на пониженных ступенях нагрева. Масса шлака в ковше должна обеспечивать незначительное оголение металла в зоне продувки, стабильное и бесшумное горение дуги, а также защиту огнеупорной футеровки ковша и водоохлаждаемых элементов установки от прямого излучения дуг.
|
Расход извести должен составлять от 1200 до 1500 кг на плавку (с учетом извести присаженной в ковш на выпуске из ДСП). Известь вводят в ковш порциями массой от 200 до 300 кг. Расход плавикового шпата (расход другого материала для разжижения шлака оговаривается отдельно) должен составлять от 300 до 400 кг на плавку.
Ввод раскислителей разрешается осуществлять после отдачи не менее 600 кг извести и 300 кг плавикового шпата. Ввод карбида кремния производить после ввода карбида кальция с учетом массовой доли углерода в металле. Рекомендуется производить комплексное раскисление карбидом кальция и карбидом кремния. Ввод гранулированного алюминия массой 30 кг производить после ввода карбидов, для стали с массовой долей серы менее 0,005% разрешается увеличивать массу вводимого гранулированного алюминия от 50 до 70 кг. Рекомендуемая температура начала раскисления плавки – не менее 1530 0С.
Через 5-10 минут после отдачи раскислителей шлака, либо совместно с отбором пробы металла №2, производится отбор пробы шлака. Если массовая доля (FeO) в шлаке выше 1,5%, то производится дополнительное раскисление шлака присадкой карбида кальция (кремния) или при невозможности присадки карбидов, раскисление произвести гранулированным алюминием массой от 10 до 15 кг.
В процессе наведения шлака отбирают пробы шлака для визуального контроля. Шлак может быть черного, коричневого, серого, зеленого, желтого или белого цветов с промежуточными оттенками, характеризующими следующее:
– черный шлак - суммарная массовая доля (FeO) и оксида марганца (ΙΙ) (МnО) в шлаке более 2,0%;
– от серого до коричневого - суммарная массовая доля (FeO) и (МnО) – 1,0-2,0%;
– зелёный - повышенная массовая доля оксидов хрома;
– от желтого до белого - массовая доля оксида железа (FeO) менее 1,0%;
– жёлтый - насыщение шлака серой.
Хорошо раскисленный высокоосновный рафинировочный шлак должен быть светло-серого, желтого или белого цвета, иметь матовую шероховатую поверхность, намораживаться на металлический прут «шубой», толщиной около 5 мм (определяется визуально), не иметь видимых включений разнородных материалов, в изломе иметь мелкопористую структуру, при охлаждении рассыпаться в порошок светло-серого или белого цвета.
|
Через 1-2 мин после ввода раскислителей шлака производят присадку ферросплавов на нижний марочный предел (с учетом ферросплавов, введенных на выпуске). Разрешается отдачу первой порции ферросплавов производить после наведения шлака одновременно с вводом раскислителей.
Доводку химического состава стали по углероду и кремнию производить преимущественно с помощью карбида кальция и (или) карбида кремния. Присадка феррониобия (FeNb) и ферромолибдена (FeMo) на УКП должна производиться не позднее, чем за 20 мин до конца обработки. Разрешается производить присадку всех легирующих при включенной нагрузке на пониженных и средних ступенях мощности трансформатора кроме ферротитана, алюминия и силикокальция. Легирование стали ферротитаном (FeTi) (кроме стали марки 20ГЮТ) производить в конце внепечной обработки стали на УКП непосредственно перед вводом алюминиевой проволоки. При отдаче коксовой пыли (коксового орешка) при включенной нагрузке (под дугами) усвоение углерода считать ориентировочно от 30 до 50%.
Рекомендуемая температура металла за 10-15 мин до конца обработки (перед вводом алюминия) должна быть на 10-15ºС более заданной температуры разливки.
По результатам измерения активности кислорода и температуры стали производят ввод алюминиевой проволоки.
Расчет массы вводимой алюминиевой проволоки для стали, дополнительно легированной титаном, производить с учетом массы алюминия, вносимого с FeTi.
Легирование стали бором, если это необходимо в соответствии с заказом, производить в конце внепечной обработки стали на УКП после ввода алюминиевой проволоки. Масса вводимого бора рассчитывается на верхнемарочное значение без учета угара. После ввода ферробора, интенсивность продувки металла аргоном должна быть минимальной.
После ввода силикокальциевой проволоки производят продувку металла аргоном с интенсивностью не приводящей к оголению металла в течение времени от 5 до 10 мин.
Отбор проб металла производят разовыми пробоотборниками при отключенной дуговой нагрузке.
Пробы металла отбирают:
− первую пробу – после усреднительной продувки в течение времени от 3 до 5 мин;
− вторую пробу и последующие – не ранее, чем через 5 мин после окончания доводки химического состава металла;
− последняя проба отбирается после окончания внепечной обработки перед отдачей плавки на разливку.
Пробы шлака отбирают:
− первую пробу – из ковша после усреднительной продувки;
− вторую пробу – через 5-10 минут после отдачи раскислителей шлака, либо совместно с отбором пробы металла №2;
|
− третью пробу – перед отдачей плавки на разливку. В пробах шлака определяют массовую долю оксидов кальция (CaO), кремния (ΙV) (SiO2), железа (ΙΙ) (FeO), марганца (MnO), магния (MgO), алюминия (ΙΙΙ) (Al2O3).
После постановки ковша с металлом на УКП и проведения усреднительной продувки производится замер температуры. Промежуточный контроль температуры металла рекомендуется производить через каждые 10 - 15 мин работы под током (в зависимости от ступени напряжения) и через 15 мин. при работе без дугового подогрева. Последний замер температуры производят не ранее, чем за 2 мин перед подачей ковша на разливку.
Измерение температуры при обработке на установке «ковш-печь» производить при отключенной дуговой нагрузке.
Рекомендуемая длительность обработки металла на установке «ковш-печь» должна быть не менее 70 мин.
В процессе обработки металла на установке «ковш-печь» контролеры фиксируют и заносят в паспорт плавки следующие параметры технологического процесса:
− номер и позицию установки «ковш-печь»;
− номер сталеразливочного ковша;
− время начала и конца обработки металла на установке «ковш-печь»;
− время измерения температуры и взятия ковшевых проб;
− температуру металла в процессе обработки.
Все результаты заносятся в паспорт плавки на ковш печи:
− время начала и окончания продувки аргоном (азотом);
− массу, вид, и время ввода материалов (при вводе ферросплавов, кокса и алюминия указывают время отдачи каждой порции материала);
− химический состав металла и шлака по ходу обработки;
− время включения и отключения подогрева, ступень напряжения;
− расход электроэнергии;
− общий объём инертного газа.
Техническое обслуживание оборудования проводить в соответствии с требованиями карт технического обслуживания и инструкций по эксплуатации и техническому обслуживанию, ремонту технических устройств.
|
|
Своеобразие русской архитектуры: Основной материал – дерево – быстрота постройки, но недолговечность и необходимость деления...
Наброски и зарисовки растений, плодов, цветов: Освоить конструктивное построение структуры дерева через зарисовки отдельных деревьев, группы деревьев...
Эмиссия газов от очистных сооружений канализации: В последние годы внимание мирового сообщества сосредоточено на экологических проблемах...
Индивидуальные и групповые автопоилки: для животных. Схемы и конструкции...
© cyberpedia.su 2017-2024 - Не является автором материалов. Исключительное право сохранено за автором текста.
Если вы не хотите, чтобы данный материал был у нас на сайте, перейдите по ссылке: Нарушение авторских прав. Мы поможем в написании вашей работы!