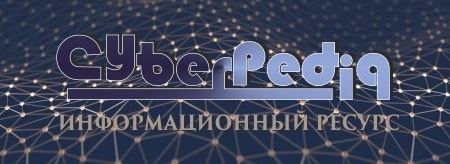
Особенности сооружения опор в сложных условиях: Сооружение ВЛ в районах с суровыми климатическими и тяжелыми геологическими условиями...
История развития пистолетов-пулеметов: Предпосылкой для возникновения пистолетов-пулеметов послужила давняя тенденция тяготения винтовок...
Топ:
Особенности труда и отдыха в условиях низких температур: К работам при низких температурах на открытом воздухе и в не отапливаемых помещениях допускаются лица не моложе 18 лет, прошедшие...
Методика измерений сопротивления растеканию тока анодного заземления: Анодный заземлитель (анод) – проводник, погруженный в электролитическую среду (грунт, раствор электролита) и подключенный к положительному...
Отражение на счетах бухгалтерского учета процесса приобретения: Процесс заготовления представляет систему экономических событий, включающих приобретение организацией у поставщиков сырья...
Интересное:
Мероприятия для защиты от морозного пучения грунтов: Инженерная защита от морозного (криогенного) пучения грунтов необходима для легких малоэтажных зданий и других сооружений...
Средства для ингаляционного наркоза: Наркоз наступает в результате вдыхания (ингаляции) средств, которое осуществляют или с помощью маски...
Принципы управления денежными потоками: одним из методов контроля за состоянием денежной наличности является...
Дисциплины:
![]() |
![]() |
5.00
из
|
Заказать работу |
6.3.1. Сосуды, на которыераспространяется действие Правил, должны подвергаться техническомуосвидетельствованию после монтажа, до пуска в работу, периодически в процессеэксплуатации и в необходимых случаях - внеочередному освидетельствованию.
6.3.2. Объем, методы ипериодичность технических освидетельствований сосудов (за исключением баллонов)должны быть определены изготовителем и указаны в руководстве по эксплуатации.
В случаеотсутствия таких указаний техническое освидетельствование должно проводиться всоответствии с требованиями табл. 10, 11, 12, 13,14, 15 Правил.
Если по условиямпроизводства не представляется возможным предъявить сосуд дляосвидетельствования в назначенный срок, владелец обязанпредъявить его досрочно.
Освидетельствованиебаллонов должно проводиться по методике,утвержденной разработчиком конструкции баллонов, в которой должны быть указаныпериодичность освидетельствования и нормы браковки.
При техническомосвидетельствовании допускается использовать все методы неразрушающегоконтроля, в том числе метод акустическойэмиссии.
6.3.3. Техническое освидетельствование сосудов, не регистрируемых в органахГосгортехнадзора России, проводится лицом,ответственным за осуществлениепроизводственного контроля за соблюдением требований промышленной безопасностипри эксплуатации сосудов, работающих поддавлением.
Первичное,периодическое и внеочередное техническое освидетельствование сосудов,регистрируемых в органах Госгортехнадзора России, проводится специалистоморганизации, имеющей лицензию Госгортехнадзора России на проведениеэкспертизы промышленной безопасности технических устройств (сосудов).
6.3.4. Наружный и внутреннийосмотры имеют целью:
при первичномосвидетельствовании проверить, что сосуд установлен и оборудован в соответствиис Правилами и представленными при регистрации документами, а также что сосуд иего элементы не имеют повреждений;
припериодических и внеочередных освидетельствованиях установить исправность сосудаи возможность его дальнейшей работы.
Гидравлическоеиспытание имеет целью проверку прочности элементов сосуда и плотностисоединений. Сосуды должны предъявляться к гидравлическому испытанию сустановленной на них арматурой.
6.3.5. Перед внутреннимосмотром и гидравлическим испытанием сосуд должен быть остановлен, охлажден(отогрет), освобожден от заполняющей его рабочей среды, отключен заглушками отвсех трубопроводов, соединяющих сосуд с источникомдавление или с другими сосудами. Металлическиесосуды должны быть очищены до металла.
Сосуды,работающие с вредными веществами 1-го и 2-го классов опасности по ГОСТ12.1.007-76, до начала выполнения внутрикаких-либо работ, а также перед внутреннимосмотром должны подвергаться тщательнойобработке (нейтрализации, дегазации) в соответствии с инструкцией побезопасному ведению работ, утвержденнойвладельцем сосуда в установленном порядке.
Футеровка,изоляция и другие виды защиты от коррозии должны быть частично или полностьюудалены, если имеются признаки, указывающие на возможностьвозникновения дефектов материала силовых элементов конструкции сосудов(неплотность футеровки, отдулиныгуммировки,следы промокания изоляции и т.п.). Электрообогреви привод сосуда должны быть отключены. При этом должны выполняться требованияпп. 7.4.4, 7.4.5, 7.4.6Правил.
6.3.6. Внеочередноеосвидетельствование сосудов, находящихся вэксплуатации, должно быть проведено в следующих случаях:
если сосуд неэксплуатировался более 12 месяцев;
если сосуд былдемонтирован и установлен на новом месте;
если произведеновыправлениевыпучин или вмятин, а также реконструкция или ремонт сосуда сприменением сварки или пайки элементов, работающих под давлением;
перед наложениемзащитного покрытия на стенки сосуда;
после авариисосуда или элементов, работающих под давлением, если по объемувосстановительных работ требуется такое освидетельствование;
по требованиюинспектора Госгортехнадзора России или ответственного по надзору заосуществлением производственного контроля за соблюдением требованийпромышленной безопасности при эксплуатации сосудов, работающих под давлением.
6.3.7. Техническоеосвидетельствование сосудов, цистерн, баллонов и бочек может производиться наспециальных ремонтно-испытательных пунктах, ворганизациях-изготовителях, наполнительных станциях, а также ворганизациях-владельцах, располагающих необходимой базой, оборудованием дляпроведения освидетельствования в соответствии с требованиями Правил.
6.3.8. Результатытехнического освидетельствования должны записыватьсяв паспорте сосуда лицом, производившим освидетельствование,с указанием разрешенных параметров эксплуатации сосуда и сроков следующих освидетельствований.
При проведениивнеочередного освидетельствования должна быть указана причина, вызвавшаянеобходимость в таком освидетельствовании.
Если приосвидетельствовании проводились дополнительные испытания и исследования, то впаспорте сосуда должны быть записаны виды и результаты этих испытаний иисследований с указанием мест отбораобразцов или участков, подвергнутых испытаниям, а также причины, вызвавшиенеобходимость проведения дополнительных испытаний.
6.3.10. Если при освидетельствовании будут обнаружены дефекты, снижающие прочность сосуда, то эксплуатация его может бытьразрешена при пониженных параметрах (давление и температура).
Возможностьэксплуатации сосуда при пониженных параметрах должна быть подтверждена расчетомна прочность, представляемым владельцем, при этом должен быть проведенпроверочный расчет пропускной способности предохранительных клапанов ивыполнены требования п. 5.5.6Правил.
Такое решениезаписывается в паспорт сосуда лицом, проводившим освидетельствование.
6.3.11. В случае выявлениядефектов, причины и последствия которых установить затруднительно, лицо,проводившее техническое освидетельствование сосуда, обязано потребовать отвладельца сосуда проведения специальных исследований, а в необходимых случаях -представления заключения специализированной организации о причинах появлениядефектов, а также о возможности и условиях дальнейшей эксплуатации сосуда.
6.3.12. Если при техническомосвидетельствовании окажется, что сосуд вследствие имеющихся дефектов илинарушений Правил находится в состоянии, опасном для дальнейшей эксплуатации,работа такого сосуда должна быть запрещена.
6.3.13. Сосуды, поставляемые в собранном виде, должны бытьизготовителем законсервированы и в руководстве по эксплуатации указаны условия и сроки их хранения. При выполнении этихтребований перед пуском в работу проводятся только наружный и внутренний осмотры, гидравлическое испытание сосудовпроводить не требуется. В этом случае срок гидравлического испытанияназначается исходя из даты выдачи разрешения на эксплуатации сосуда.
Емкости длясжиженного газа перед нанесением на них изоляции должны подвергаться тольконаружному и внутреннему осмотрам, еслибыли соблюдены сроки и условия изготовителя по их хранению.
После установкина место эксплуатации до засыпки грунтом указанные емкости могутподвергаться только наружному осмотру, если смомента нанесения изоляции прошло не более 12месяцев и при их монтаже не применялась сварка.
6.3.14. Сосуды, работающиепод давлением вредных веществ (жидкости и газов) 1-го, 2-го классовопасности по ГОСТ12.1.007-76 должны подвергаться владельцем сосуда испытанию на герметичность воздухом или инертным газом под давлением, равнымрабочему давлению. Испытания проводятся владельцем сосуда в соответствии синструкцией, утвержденной в установленном порядке.
6.3.15. При наружном ивнутреннем осмотрах должны быть выявлены все дефекты, снижающие прочностьсосудов, при этом особое внимание должно быть обращено на выявление следующихдефектов:
на поверхностяхсосуда - трещин, надрывов, коррозии стенок (особенно в местах отбортовкиивырезок), выпучин, отдулин(преимущественно у сосудов с «рубашками», а также у сосудов с огневым илиэлектрическим обогревом), раковин (в литых сосудах);
в сварных швах -дефектов сварки, указанных в п. 4.5.17Правил, надрывов, разъеданий;
в заклепочныхшвах - трещин между заклепками, обрывов головок, следов пропусков, надрывов вкромках склепанных листов, коррозионных повреждений заклепочных швов, зазоровпод кромками клепаных листов и головками заклепок, особенно у сосудов,работающих с агрессивными средами (кислотой, кислородом, щелочами и др.);
в сосудах сзащищенными от коррозии поверхностями - разрушений футеровки, в том численеплотностей слоев футеровочных плиток, трещин в гуммированном,свинцовом или ином покрытии, скалыванийэмали, трещин и отдулин в плакирующем слое,повреждений металла стенок сосуда в местах наружного защитного покрытия;
в металлопластиковых инеметаллических сосудах - расслоения и разрывыармирующих волокон свыше норм, установленныхспециализированной организацией.
6.3.16. Лицо, проводящееосвидетельствование, при необходимости можетпотребовать удаления (полного или частичного) защитного покрытия.
6.3.17. Сосуды высотой более 2 м перед осмотром должны быть оборудованы необходимымиприспособлениями, обеспечивающими возможностьбезопасного доступа ко всем частям сосуда.
6.3.18. Гидравлическое испытание сосудов проводится только приудовлетворительныхрезультатах наружного и внутреннего осмотров.
6.3.19. Гидравлическиеиспытания должны проводиться в соответствии с требованиями, изложенными в разд.4.6 Правил, за исключением п.4.6.12. При этом величина пробногодавления может определяться исходя из разрешенного давления для сосуда. Подпробным давлением сосуд должен находиться в течение 5 мин, если отсутствуют другие указания изготовителя.
Пригидравлическом испытании вертикально установленных сосудов пробное давлениедолжно контролироваться по манометру,установленномунаверхней крышке (днище) сосуда.
6.3.20. В случаях, когдапроведение гидравлического испытания невозможно (большое напряжение от весаводы в фундаменте, междуэтажных перекрытиях или самом сосуде; трудностьудаления воды; наличие внутри сосуда футеровки, препятствующей заполнениюсосуда водой), разрешается заменять его пневматическим испытанием (воздухом илиинертным газом). Этот вид испытания допускается при условии его контроляметодом акустической эмиссии (или другим, согласованным с Госгортехнадзором России методом).
Припневматическомиспытании применяются меры предосторожности: вентиль нанаполнительном трубопроводе от источника давления и манометры выводятся запределы помещения, в котором находится испытываемый сосуд, а люди на времяиспытания сосуда пробным давлением удаляются в безопасное место.
6.3.21. День проведениятехнического освидетельствования сосуда устанавливается владельцем ипредварительно согласовывается с лицом, проводящим освидетельствование. Сосуддолжен быть остановлен не позднее срокаосвидетельствования, указанного в его паспорте. Владелец не позднее, чем за 5 дней обязан уведомить опредстоящем освидетельствовании сосуда лицо, выполняющее указанную работу.
В случае неявкиинспектора в назначенный срок администрации предоставляется правосамостоятельно провести освидетельствование комиссией, назначенной приказом руководителя организации.
Результатыпроведенного и срок следующего освидетельствования заносятся впаспорт сосуда и подписываются членами комиссии.
Копия этойзаписи направляется в орган Госгортехнадзора России не позднеечем через 5 дней после освидетельствования.
Установленныйкомиссией срок следующего освидетельствования не должен превышать указанного внастоящихправилах.
6.3.25. Если при анализе дефектов, выявленных техническим освидетельствованием сосудов, будет установлено, что ихвозникновение связано с режимом эксплуатации сосудов в данной организации илисвойственно сосудам данной конструкции, то лицо, проводившее освидетельствование,должно потребовать проведения внеочередноготехнического освидетельствования всех установленных в данной организации сосудов, эксплуатация которых проводилась поодинаковому режиму, или соответственно всех сосудов данной конструкции с уведомлениемоб этом органа Госгортехнадзора России.
6.3.26. ОргануГосгортехнадзора России предоставляется право висключительных случаях продлять на срок не более 3 месяцев установленныесроки технического освидетельствования сосудов по обоснованному письменному ходатайству владельца сосуда.
Назначение и классификация баллонов. Требования к конструкции, маркировке, установке и техническому освидетельствованию баллонов
Глава 10. Документация и маркировка
213. Каждый сосуд поставляется изготовителем заказчику с паспортом согласно приложению 1 к настоящим Требованиям.
К паспорту прикладывается руководство по эксплуатации.
Паспорт сосуда составляется на государственном и русском языках.
Допускается к паспорту прикладывать распечатки расчетов.
Элементы сосудов (корпуса, обечайки, днища, крышки, трубные решетки, фланцы корпуса, укрупненные сборочные единицы), предназначенные для реконструкции или ремонта, поставляются изготовителем с удостоверением о качестве изготовления, содержащим сведения в объеме, согласно требованиям соответствующих разделов паспорта.
214. На каждом сосуде прикрепляется табличка. Для сосудов наружным диаметром менее 325 мм допускается табличку не устанавливать. При этом все необходимые данные наносятся на корпус сосуда электрографическим методом.
215. На табличке наносятся:
1) товарный знак или наименование изготовителя;
2) наименование или обозначение сосуда;
3) порядковый номер сосуда по системе нумерации изготовителя;
4) год изготовления;
5) рабочее давление, МПа;
6) расчетное давление, МПа;
7) пробное давление, МПа;
8) допустимая максимальная и (или) минимальная рабочая температура стенки, °С;
9) масса сосуда, кг.
Для сосудов с самостоятельными полостями, имеющими разные расчетные и пробные давления, температуру стенок, указывают эти данные для каждой полости.
Глава 3. Конструкция сосудов
12. Конструкция сосудов обеспечивает надежность и безопасность эксплуатации в течение расчетного срока службы и предусматривает возможность проведения технического освидетельствования, очистки, промывки, полного опорожнения, продувки, ремонта, эксплуатационного контроля металла и соединений.
13. Для каждого сосуда в паспорте устанавливается и указывается расчетный срок службы с учетом условий эксплуатации.
14. Устройства, препятствующие наружному и внутреннему осмотрам сосудов (мешалки, змеевики, рубашки, тарелки, перегородки и другие приспособления), предусматриваются съемными.
При применении приварных устройств предусматривается возможность их удаления для проведения наружного и внутреннего осмотров и последующей установки на место. Порядок съема и установки этих устройств указывается в руководстве по эксплуатации сосуда.
15. Если конструкция сосуда не позволяет проведение наружного и внутреннего осмотров или гидравлического испытания, предусмотренных настоящими Требованиями, разработчиком проекта сосуда в руководстве по эксплуатации указывается методика, периодичность и объем контроля, выполнение которых обеспечивает своевременное выявление и устранение дефектов. В случае отсутствия в руководстве таких указаний методика, периодичность и объем контроля определяются специализированной организацией.
16. Конструкции внутренних устройств обеспечивают удаление из сосуда воздуха при гидравлическом испытании и воды после гидравлического испытания.
17. Сосуды имеют штуцера для наполнения и слива воды, для удаления воздуха при гидравлическом испытании.
18. На каждом сосуде предусматривается вентиль, кран или другое устройство, позволяющее осуществлять контроль за отсутствием давления в сосуде перед его открыванием; при этом отвод среды направляется в безопасное место.
19. Сосуды, предназначенные для работы в условиях циклических и знакопеременных нагрузок, рассчитываются на прочность с учетом этих нагрузок.
20. Сосуды, которые в процессе эксплуатации изменяют свое положение в пространстве, имеют приспособления, предотвращающие их самоопрокидывание.
21. Конструкция сосудов, обогреваемых горячими газами, обеспечивает надежное охлаждение стенок, находящихся под давлением, до расчетной температуры.
22. Для проверки качества приварки колец, укрепляющих отверстия для люков, лазов и штуцеров, предусматривается резьбовое контрольное отверстие в кольце, если оно приварено снаружи, или в стенке, если кольцо приварено с внутренней стороны сосуда.
Данное требование распространяется и на привариваемые снаружи к корпусу накладки или другие укрепляющие элементы.
Наружные глухие элементы (например, накладки), не работающие под давлением, имеют дренажные отверстия в самых низких местах.
23. Заземление и электрическое оборудование сосудов выполняются с соблюдением норм технической эксплуатации электроустановок потребителей и техники безопасности при эксплуатации электроустановок потребителей в установленном порядке.
24. Сосуды снабжаются необходимым количеством люков и смотровых лючков, обеспечивающих осмотр, очистку и ремонт сосудов, монтаж и демонтаж разборных внутренних устройств.
Сосуды, состоящие из цилиндрического корпуса и решеток с закрепленными в них трубками (теплообменники), и сосуды, предназначенные для транспортировки и хранения криогенных жидкостей, сосуды, предназначенные для работы с веществами 1-го и 2-го класса опасности в соответствии с ГОСТ 12.1.007, но не вызывающие коррозии и накипи, допускается изготовлять без люков и лючков, независимо от диаметра сосудов при условии выполнения требований пункта 15.
25. Сосуды с внутренним диаметром более 800 мм имеют люки, а с внутренним диаметром 800 мм и менее-лючки.
26. Внутренний диаметр круглых люков-не менее 400 мм. Размеры овальных люков по наименьшей и наибольшей осями в свету-не менее 325×400 мм.
Внутренний диаметр круглых или размер по наименьшей оси овальных лючков-не менее 80 мм.
27. Люки и лючки располагаются в местах, доступных для обслуживания. Требования к устройству, расположению и обслуживанию смотровых окон в барокамерах определяются проектной организацией и указываются в руководстве по монтажу и эксплуатации завода-изготовителя.
28. Крышки люков являются съемными. На сосудах, изолированных на основе вакуума, допускаются приварные крышки.
29. Крышки массой более 20 кг снабжаются подъемно-поворотными или другими устройствами для их открывания и закрывания.
30. Конструкция шарнирно-откидных или вставных болтов, хомутов, зажимных приспособлений люков, крышек и их фланцев предотвращает их самопроизвольный сдвиг.
31. При наличии на сосудах штуцеров, фланцевых разъемов, съемных днищ или крышек, внутренний диаметр которых не менее указанных величин для люков в пункте 26 настоящих Требований, обеспечивающих возможность проведения внутреннего осмотра, допускается люки не предусматривать.
32. В сосудах применяются днища: эллиптические, полусферические, торосферические, сферические неотбортованные, конические отбортованные, конические неотбортованные, плоские отбортованные, плоские неотбортованные.
33. Эллиптические днища имеют высоту выпуклой части, измеренную по внутренней поверхности, не менее 0,2 внутреннего диаметра днища. Уменьшение этой величины согласовывается со специализированной научно-исследовательской организацией.
34. Торосферические (коробовые) днища изготавливаются размерами, где:
1) высота выпуклой части, измеренная по внутренней поверхности, не менее 0,2 внутреннего диаметра;
2) внутренний радиус отбортовки не менее 0,1 внутреннего диаметра днища;
3) внутренний радиус кривизны центральной части не более внутреннего диаметра днища.
35. Сферические неотбортованные днища применяются с приварными фланцами, при этом:
1) внутренний радиус сферы днища-не более внутреннего диаметра сосуда;
2) сварное соединение фланца с днищем выполняется со сплошным проваром.
36. В сварных выпуклых днищах, за исключением полусферических, состоящих из нескольких частей с расположением сварных швов по хорде, расстояние от оси сварного шва до центра днища выбирается не более 1/5 внутреннего диаметра днища.
Круговые швы выпуклых днищ располагаются от центра днища на расстоянии не более 1/3 внутреннего диаметра днища.
37. Конические неотбортованные днища имеют центральный угол не более 45°. Центральный угол конического днища увеличивается по заключению специализированной научно-исследовательской организации по аппаратостроению.
38. Плоские днища с кольцевой канавкой и цилиндрической частью (бортом), изготовленные механической расточкой, изготавливаются из поковки. Допускается изготовление отбортованного плоского днища из листа, если отбортовка выполняется штамповкой или обкаткой кромки листа с изгибом на 90°.
40. При сварке обечаек и труб, приварке днищ к обечайкам применяются стыковые швы с полным проплавлением.
Сварные соединения в тавр и угловые с полным проплавлением применяются для приварки плоских днищ, плоских фланцев, трубных решеток, штуцеров, люков, рубашек.
Нахлесточные сварные швы применяются для приварки к корпусу укрепляющих колец, опорных элементов, подкладных листов, пластин под площадки, лестницы, кронштейны и тому подобное.
41. Конструктивный зазор в угловых и тавровых сварных соединениях применяется в случаях, предусмотренных НД, согласованной в установленном порядке.
42. Сварные швы выполняются доступными для контроля при изготовлении, монтаже и эксплуатации сосудов, предусмотренного настоящими Требованиями, требованиями соответствующих стандартов и НД.
43. Продольные швы смежных обечаек и швы днищ сосудов смещаются относительно друг друга на величину трехкратной толщины наиболее толстого элемента, но не менее чем на 100 мм между осями швов.
Указанные швы не смещаются относительно друг друга в сосудах, предназначенных для работы под давлением не более 1,6 МПа (16 кгс/см2) и температуре стенки не выше 400°С, с номинальной толщиной стенки не более 30 мм при условии, что эти швы выполняются автоматической или электрошлаковой сваркой и места пересечения швов контролируются методом радиографии или ультразвуковой дефектоскопии в объеме 100 %.
44. При приварке к корпусу сосуда внутренних и внешних устройств (опорных элементов, тарелок, рубашек, перегородок и других) допускается пересечение этих сварных швов со стыковыми швами корпуса при условии предварительной проверки перекрываемого участка шва корпуса радиографическим контролем или ультразвуковой дефектоскопией.
45. В случае приварки опор или иных элементов к корпусу сосуда расстояние между краем сварного шва сосуда и краем шва приварки элемента выбирается не менее толщины стенки корпуса сосуда, но не менее 20 мм.
Для сосудов из углеродистых и низколегированных марганцовистых и марганцово-кремнистых сталей (приложение 2 «Подразделение сталей на типы и классы» настоящих Требований), подвергаемых после сварки термообработке, независимо от толщины стенки корпуса, расстояние между краем сварного шва сосуда и краем шва приварки элемента выбирается не менее 20 мм.
46. В горизонтальных сосудах допускается местное перекрытие седловыми опорами кольцевых (поперечных) сварных швов на общей длине не более 0,35πD, а при наличии подкладного листа-не более 0,5πD, где D-наружный диаметр сосуда.
При этом перекрываемые участки сварных швов по всей длине проверяются методом радиографии или ультразвуковой дефектоскопии. Перекрытие мест пересечения швов не допускается.
47. В стыковых сварных соединениях элементов сосудов с разной толщиной стенок обеспечивается плавный переход от одного элемента к другому путем постепенного утонения кромки более толстого элемента. Угол наклона поверхностей перехода не более 20°.
Если разница в толщине соединяемых элементов составляет не более 30 % толщины тонкого элемента и не более 5 мм, то допускается применение сварных швов без предварительного утонения толстого элемента. Форма швов обеспечивает плавный переход от толстого элемента к тонкому.
При стыковке литой детали с деталями из труб, проката или поковок учитывают, что номинальная расчетная толщина литой детали на 25-40 % больше аналогичной расчетной толщины стенки элемента из труб, проката или поковок, поэтому переход от толстого элемента к тонкому выполняется таким образом, чтобы толщина конца литой детали была не менее расчетной величины.
Глава 12. Установка сосудов
269. Сосуды устанавливаются на открытых площадках в местах, исключающих
скопление людей, или в отдельно стоящих зданиях.
270. Допускается установка сосудов:
1) в помещениях, примыкающих к производственным зданиям, при условии отделения
их от здания капитальной стеной;
2) в производственных помещениях в случаях, предусмотренных отраслевыми
правилами безопасности;
3) с заглублением в грунт при условии обеспечения доступа к арматуре и защиты
стенок сосуда от почвенной коррозии и коррозии блуждающими токами.
271. Не допускается установка сосудов, зарегистрированных в территориальных
подразделениях уполномоченного органа, в жилых, общественных и бытовых зданиях, в
примыкающих к ним помещениях.
272.Установка сосудов исключает их опрокидывание.
273. Установка сосудов обеспечивает возможность осмотра, ремонта и очистки их с
внутренней и наружной сторон.
Для удобства обслуживания сосудов устраиваются площадки и лестницы. Для
осмотра и ремонта сосудов применяются люльки и другие приспособления.
Указанные устройства не нарушают прочности и устойчивости сосуда, а приварка их
к сосуду выполняется по проекту в соответствии с требованием настоящих Правил.
Материалы, конструкция лестниц и площадок соответствуют действующей нормативной
документации.
К изготовлению баллонов предъявляются повышенные требования. Стенки баллонов не должны иметь раковин, плен, закатов и рисок глубиной более 10% номинальной толщины стенки. Допускаются лишь незначительные дефекты в виде углублений, вдавлен от окалины, коночного происхождения и др;
На верхней сферической части каждого баллона должны быть отчетливо, путем клеймения, нанесены следующие данные: товарный знак завода-изготовителя; номер баллона; фактический вес порожнего баллона, кг: для баллонов емкостью до 12 л включительно — с точностью до 0,1 кг, для баллонов емкостью свыше 12 до 55 л включительно — с точностью до 0,2кг; вес баллонов емкостью свыше 55 л указывается в соответствии с ГОСТом или ТУ на их изготовление; дата (месяц и год) изготовления и год следующего освидетельствования; рабочее давление Р., кгс/см2; пробное гидравлическое давление П, кгс/см2 емкость баллона, л; для баллонов емкостью до 12 л включительно — номинальная, для баллонов емкостью свыше 12 л до 55 л включительно — фактическая с точностью до 0,3 л, для баллонов емкостью свыше 55 л — в соответствии с ГОСТом или ТУ на их изготовление; клеймо ОТК завода-изготовителя круглой формы диаметром 10 мм (за исключением стандартных баллонов емкостью свыше 55 л); номер стандартов для баллонов емкостью свыше 55 л.
Высота знаков на баллонах должна быть не менее 6 мм, а на баллонах емкостью свыше 55 л' — не менее 8 мм. Вес баллонов, за исключением баллонов для ацетилена, указывается с учетом веса нанесенной краски, кольца для колпака и башмака но без веса вентиля и колпака. Место на баллонах, где выбиты паспортные данные, должно быть покрыто бесцветным лаком в обведено отличительной краской в виде рамки.
У баллонов для горючих газов боковые штуцера вентилей снабжены левой, а у баллонов для негорючих газов — правой резьбой. До транспортировки и при хранении, баллонов на эти штуцера плотно навертываются специальные заглушки.
В баллонах транспортируются и хранятся:
сжатые газы: кислород, водород, азот, воздух, коксовый, светильный, некоторые промышленные газы (побочные продукты основного производства), аргон, гелий и др.
сжиженные газы: аммиак, бутан, бутилен, дихлордифторметан (фреон), закись азота, изобутилен, сероводород, сернистый ангидрид, пропан, пропилеи, углекислота, фосген, хлор, хлористый метил, хлористый этил, этилен и др.;
ацетилен в растворенном виде.
Наружная поверхность баллонов должна быть окрашена в условный отличительный цвет (таблица).
Надписи на баллонах наносят вкруговую длиной не менее 1/3 окружности, а полосы —,по всей окружности, причем высота букв на баллонах емкостью более 12 л должна быть 60 мм, а ширина полосы — 25 мм. Размеры.надписей и полос на баллонах емкостью до 12 л должны определяться в зависимости от величины боковой поверхности баллонов.
Освидетельствование баллонов. Проверяют качество, освидетельствуют и принимают вновь изготовленные баллоны отделы технического контроля заводов-изготовителей в соответствии с требованиями «Правил устройства.и безопасной эксплуатации сосудов, работающих под давлением», государственных стандартов на баллоны и технических условий. На заводах-изготовителях баллоны подвергаются гидравлическому испытанию пробным давлением, в том числе стандартные согласно ГОСТУ нестандартные — по техническим условиям, но не менее чем полуторным рабочим давлением. Баллоны, за исключением предназначенных для ацетилена, после гидравлического подвергаются пневматическому испытанию давлением, равным рабочему При этом важно соблюдать правила погружения баллонов при пневматическом испытании в ванну с водой. Баллоны для ацетилена подвергаются пневматическому испытанию на заводах, наполняющих их пористой массой.
Результаты освидетельствования вновь изготовленных баллонов работники отдела технического контроля завода-изготовителя заносят в специальную ведомость в следующем порядке: порядковый номер, номер баллона, дата (месяц и год) изготовления (испытания) баллона и следующего освидетельствования; вес баллона, кг; емкость баллона, л; рабочее давление, кгс/см2, пробное давление, кгс/см2, подпись представителя ОТК заводаизготовителя.
Все заполненные ведомости нумеруются, прошнуровываются и хранятся в делах ОТК завода.
Техническое состояние всех баллонов, находящихся в эксплуатации, периодически проверяют на заводах-изготовителях или наполнительных станциях лица, специально назначенные для этой цели приказом руководителей этих организаций. Такое разрешение на периодическую проверку баллонов выдается указанным выше организациям при наличии условий, обеспечивающих возможность качественного проведения освидетельствования, уровня подготовки лиц, назначенных на эту работу, и наличия соответствующих инструкций. При положительном решении вопроса органы Госгортехнадзора регистрируют у себя клеймо, присвоенное данной организации.
Правилами установлены следующие сроки периодического освидетельствования баллонов:
a. баллоны, которые наполняются газами, не вызывающими коррозию (кислородом, азотом, углекислотой и т. п.), проверяются не реже одного раза в 5 лет;
b. баллоны с газами, которые вызывают коррозию (хлор,клористый метил, фосген, сероводород, сернистый ангидрид, хлористый водород и др.), а также установленные на автомобилях s качестве расходных емкостей для сжатых и сжиженных газов проверяются не реже одного раза в 2 года.
Программа периодического освидетельствования баллонов, кроме ацетиленовых, включает:
1. Осмотр внутренней и наружной поверхностей баллонов с целью выявления на их стенках коррозии, трещин, плен, вмятин и других повреждений.
Осмотру предшествует тщательная очистка баллонов и промывка их водой (а в необходимых случаях и дихлорэтаном) или дегазация.
В случае, если при осмотре наружной и внутренней поверхностей баллонов обнаружены трещины, плены, вмятины, отдулины, раковины и риски, превышающие по глубине 10% от номинальной толщины стенки, надрывы, выщербления, износ резьбы горловины, косая или слабая насадка башмака или отсутствуют какие-либо паспортные данные, то такие баллоны бракуются.
2. При отсутствии дефектов проверяется вес (емкость баллонов), который равен разности между весом баллона, заполненного водой, и весом порожнего. При этом в зависимости от увеличения емкости и потери веса баллонов определяют степень пригодности бесшовных стандартных баллонов к дальнейшему использованию.
Баллоны емкостью более 12 и до 55 л при потере веса от 7,5 до 10% или увеличении их емкости в пределах 1,5 2% переводятся на давление, сниженное против первоначально установленного на 15%.
При потере веса от 10 до 15% или увеличении емкости в пределах от 2 до 2,5% баллоны переводятся на давление, сниженное против установленного не менее чем на 50%.
При потере веса от 15 до 20% или увеличении емкости в пределах от 2,5 до 3% баллоны могут быть допущены к работе при давлении не более 6 кгс/см2.
При потере веса более 20% или увеличении емкости более чем на 3% баллоны бракуются.
Все новые данные заносятся на баллон, а старое клеймо забивается.
3. Гидравлическое испытание (кроме баллонов для ацетилена), которое проводится пробным давлением, равным полуторному рабочему.
Итоги освидетельствования баллонов, за исключением ацетиленовых, записываются в журнал в следующем порядке: порядковый номер; товарный знак завода-изготовителя; номер баллона; дата (месяц, год) изготовления баллона; дата произведенного и следующего освидетельствования; вес, указанный на баллоне, кг; вес баллона, установленный при освидетельствовании, кг; емкость баллона, установленная при освидетельствовании, л; рабочее давление Р, кгс/см2, отметка о пригодности баллона; подпись производившего освидетельствование баллонов.
Баллоны для ацетилена проверяются (освидетельствуются) не реже чем через 5 лет также на заводах-наполнителях в отдельных специальных помещениях, отвечающих требованиям Правил, с температурой воздуха не ниже 120С, но по другой схеме: осмотр наружной поверхности; проверка пористой массы; пневматическое испытание. Пористая масса проверяется на предприятиях-наполнителях каждые 12 месяцев. На баллон наноситея клеймо с годом и месяцем проверки пористой массы, указанием завода-наполнителя и, как свидетельство контроля пористой массы, изображением букв ПМ. Указанные баллоны (для ацетилена) при освидетельствовании погружаются в воду на глубину не менее 1 м и испытываются чистым азотом (не ниже 97% по объему) под давлением 35 кг/см2. Итоги такого освидетельствоваиия заносятся в журнал испытания в следующем порядке: номер по порядку, номер баллона; товарный знак завода-изготовителя и дата (месяц, год) изготовления баллона; дата произведенного и следующего освидетельствования; дата наполнения пористой массой; водяная емкость баллона, л; вес баллона без пористой массы, вентиля и колпака, но с башмаком и кольцом, кг; вес баллона без колпака, но с пористой массой," башмаком, вентилем и растворителем (тара), кг, полое пространство, см3; пробное давление азотом, кгс/cм2; рабочее давление, кгс/см2, подпись лица, производившего освидетельствование баллона.
Не прошедшие испытание, забракованные баллоны приводятся в негодность просверливанием отверстий в их корпусе или нанесением насечек на резьбе горловины.
В зависимости от исполнения цилиндрической части корпуса установлены следующие типы сосудов:
1 Кованые, изготовленные из одной кованой обечайки.
2 Кованосварные, изготовленные из однослойных кованых обечаек, сваренных кольцевыми швами между собой и концевыми элементами (днищами, фланцами, горловинами).
3 Многослойные рулонированные, изготовленные из нескольких рулонированных обечаек, сваренных между собой кольцевыми швами, а также в совокупности с однослойными частями (трубными досками, обечайками, патрубками и т.п.) и концевыми элементами.
4. Вaльцованocвaрныe, обечайки ко
Автоматическое растормаживание колес: Тормозные устройства колес предназначены для уменьшения длины пробега и улучшения маневрирования ВС при...
История создания датчика движения: Первый прибор для обнаружения движения был изобретен немецким физиком Генрихом Герцем...
Биохимия спиртового брожения: Основу технологии получения пива составляет спиртовое брожение, - при котором сахар превращается...
Индивидуальные очистные сооружения: К классу индивидуальных очистных сооружений относят сооружения, пропускная способность которых...
© cyberpedia.su 2017-2024 - Не является автором материалов. Исключительное право сохранено за автором текста.
Если вы не хотите, чтобы данный материал был у нас на сайте, перейдите по ссылке: Нарушение авторских прав. Мы поможем в написании вашей работы!