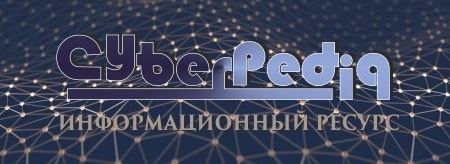
Архитектура электронного правительства: Единая архитектура – это методологический подход при создании системы управления государства, который строится...
История развития пистолетов-пулеметов: Предпосылкой для возникновения пистолетов-пулеметов послужила давняя тенденция тяготения винтовок...
Топ:
Характеристика АТП и сварочно-жестяницкого участка: Транспорт в настоящее время является одной из важнейших отраслей народного...
Процедура выполнения команд. Рабочий цикл процессора: Функционирование процессора в основном состоит из повторяющихся рабочих циклов, каждый из которых соответствует...
Когда производится ограждение поезда, остановившегося на перегоне: Во всех случаях немедленно должно быть ограждено место препятствия для движения поездов на смежном пути двухпутного...
Интересное:
Финансовый рынок и его значение в управлении денежными потоками на современном этапе: любому предприятию для расширения производства и увеличения прибыли нужны...
Уполаживание и террасирование склонов: Если глубина оврага более 5 м необходимо устройство берм. Варианты использования оврагов для градостроительных целей...
Берегоукрепление оползневых склонов: На прибрежных склонах основной причиной развития оползневых процессов является подмыв водами рек естественных склонов...
Дисциплины:
![]() |
![]() |
5.00
из
|
Заказать работу |
|
|
Главным технологическим агрегатом от надежности и эффективности работы которого зависит качество цемента и ТЭП завода является печной агрегат. Это комплект технологического оборудования, состоящий из: собственно, вращающейся печи; внутрипечного теплообменника (при мокром способе), запечного теплообменника (при сухом способе); дозатора подачи сырья; топливосжигающего устройства; тягодутьевого оборудования; аппаратов для очистки и выброса в атмосферу газов и воздуха; в комплект может входить холодильный агрегат(рекуператорный).
Химические реакции образования клинкерных минералов протекают при высоких температурах порядка 1450-1480ºС. Условно все процессы, происходящие при обжиге можно разбить на несколько этапов, которым соответствуют зоны печного агрегата.
МОКРЫЙ СПОСОБ.
1. Зона удаления воды и подогрева шихты
Удаление физически связанной воды, нагревание сырьевой смеси с одновременным изменением ее некоторых свойств. Имеют место физические процессы образования и разрушения гранул, теплообмена между средой и материалом, образование окатышей, присадка золы и пыли на влажной смеси. Протекают некоторые химические реакции, не имеющие существенного значения для синтеза клинкера.
Протяженность зоны по длине печного агрегата составляет 50-60%
2. Зона кальцинирования.
300-800ºС. Химические процессы, связанные с термической диссоциацией и превращениями некоторых минералов сырьевой шихты.
Диссоциация (декарбонизация) СаСО3 с образованием СаО
СаСО3 →СаО + СО2
Глины: Каолинит Al2O3 SiO2 2H2Oв интервале 450-600 удаляется химически связанная вода, считается возможным распад глинистого минерала на аморфные оксиды γAl2O3 и SiO2, образование метакаолинита, муллита.
|
Монтмориллонит: при температуре 100-300 удаляется химически связанная межслоевая вода, 450-750 удаляется гидроксильная вода.
Шлаки: 400-600 кристаллизация с образованием (в зависимости от состава шлака)
ßC2S;C3S2; C2AS;CS; CAS;C2AS;SiO2- тридимит, CF
Если сырье - Белитовый, нефелиновый шлам
C3A →C5A3 +4CaO
Протяженность зоны 20-23% от длины печи
3. Зона экзотермических реакций.
900-1200 Протекают твердофазовые реакции. В результате декарбонизации СаСО3 и дегидратации глинистых минералов в системе имеются реакционно способные соединения, возникли новые продукты со множеством дефектных мест, что обуславливает их высокую реакционную способность. Из числа образующихся в данной зоне продуктов следует выделить:
C2S СА→ С5А3 → С3А CF → C2F → C4AF
При участии шлака его минералы насыщаются до клинкерных (при минимальных затратах тепла) процессы протекают по схемам:
CS + С → C2S (СаОSiO2 + СаО→2 СаОSiO2)
C2AS + 3С → C2S + С3А
↓+С
C3S
СaOМqOSiO2 + СaO → C2S + MqOSiO2
Протяженность зоны 5-7%
4. Зона спекания. Протяженность зоны 10-15% от длины печи
1300-1450-1500 Образование жидкой фазы и синтез главного минерала портландцемента C3S (3СаО SiO2). В состав жидкой фазы переходит С3А; С5А3; C2F; C4AF; Na; K; Mq
Жидкофазовое спекание происходит при образовании приблизительно 25-35% расплава. Признаками спекания являются уменьшение пористости и увеличение плотности, округлость зерен.
Процессы твердофазового спекания описывают диаграммами состояния:
Образование C3Sобусловлено тем, что в жидкой фазе растворяетсяC2Sиизвесть (СаО) при этом происходит диссоциация на ионы [SiO2]־; O־²; Ca ²; Si с последующим образованиемC3S
Жидкая фаза расплава клинкера в интервале температур 1400-1450 не является истинным раствором, это структурированная жидкость, поскольку она содержит некоторое количество кристаллов. Их присутствие обусловлено химической природой расплава, неустановившимся равновесием или переменным состоянием расплава. Элементами расплава являются простые и сложные ионы, т.е. расплав – ионная жидкость.
|
В присутствииNaпроисходит снижение эвтевтики. Аналогичное явление понижения температуры жидкофазового спекания происходит при наличии в системеB2O3;PbO. Состав и количество жидкой фазы зависит от содержания алюминатов и алюмоферритов кальция. Что задается на стадии проектирования сырьевой смеси, параметр задачи – величина глиноземного модуля 0.32-0.64. При этих условиях понижается вязкость и возрастает коэффициент диффузии, в результате образуются кристаллы C3S с однородной кристаллической решеткой. Если глиноземный модуль равен 1.28, то при расплавлении смеси полученный расплав имеет высокую вязкость, соответственно, понижается диффузионная способность и количество образующегося в системе C3S снижается.
5. Зона охлаждения
1450-1300. Кристаллизация клинкерных минералов. Процесс кристаллизации характеризуется размерами и количеством образовавшихся кристаллических фаз. Характеризуется температурой в зоне обжига, длиной зоны обжига ее близостью к концу печи. Если зона длинная, то создаются крупные, неправильно локализованные кристаллы с пониженной реакционной способностью.
Протяженность зоны 2-4%
Интенсификация процесса обжига может быть обеспечена:
Введением минерализаторов, соединений, понижающих эвтевтику, к ним относят CаF2; Na2SiF6, соединения бария, бора, хрома. Но! Данные вещества могут нарушить футеровку печи, изменить некоторые свойства цемента, например, сроки схватывания.
Снижением влажности шлама за счет применения пластифицирующих добавок
Применением системы возврата пыли в печь
Устройством в печи теплообменных устройств
Улучшением полноты сгорания топлива
1- подача шлама, 2- фильтр подогреватель, 3- цепная завеса, 4 – теплообменник, 5- бандаж, 6- подбандажная обечайка, 7- венцовый привод, 8- оросительное устройство, 9- горячая головка печи, 10- колосниковый холодильник
Вращающаяся печь обжига портландцементного клинкера- футерованный огнеупорными кирпичами стальной цилиндр, имеющий небольшой наклон от загрузочного к разгрузочному концу. Движение материала по печи и теплоносителя организовано по принципу противотока. На цилиндр надеты бандажы, опирающиеся на опорные ролики, печь приводится в движение через венцовую и подвенцовую шестерни.
|
Скорость вращения печи 1.5-2 об/мин. Степень заполнения печи материалом 7-17%, если топливо уголь 4-10% от полезного объема печного агрегата. При увеличении скорости вращения возрастает интенсивность перемешивания материала, уменьшается толщина слоя, сокращается время пребывания материала в печи и возрастает производительность печи.
Футеровка зон печи: 1, 2 – шамотный кирпич, в зоне спекания – хромомагнезитовая, магнезитохромитовая, периклазошпинельная. Стойкость футеровки (в среднем) 240 суток.
При мокром способе применяют длинные вращающиеся печи размером 5х185 (производительность 1800 т/сутки), 4.5х170 (пр. 1200 т/с), 4х150 (пр. 840 т/с), 7х230 (пр.3000т/с). В среднем соотношение диаметра к длине 35-40.
Зона сушки и подогрева, оснащается теплообменниками: Цепные завесы, Звеньевой, Циклоидный, Шарнирно-винтовой Ячейковый теплообменник
__12 м____28м____28 м______26 м_______30 м______26 м______9 м_____
Основное назначение устройств- увеличить поверхность теплообмена между газами и материалом за счет чего сокращается расход топлива на 5-12%, но кроме этого позволяют решить еще ряд вопросов: снижают пылеунос, повышают коэффициент заполнения печи.
Цепные завесы – устанавливают во вращающихся печах для интенсификации процессов сушки шлама и теплообмена между обжигаемым материалом и газовым потоком. Завеса улучшает теплоиспользование в холодном конце вращающихся печей: жидкий шлам обволакивает цепи и поверхность его соприкосновения с газовым потоком увеличивается; там где шлам частично высушен, тепло передается нагретыми цепями при погружении их в шлам. в зоне сушки и подогрева шлама в печи навешивают цепи, общая длина цепей превышает 2000 м, площадь более 1500 м2, поверхность цепей рассчитывают таким образом, чтобы при выходе из цепной завесы шлам имел влажность около 12%. При излишней поверхности цепей шлам пересушивается и повышается пылевынос сырья с отходящими из печи газами. Цепи подвешивают по варианту свободновисячего конца или гирляндные. Цепи подвешивают на швеллерах (скобах, серьгах, кольцах) которые установлены по окружности печи так, чтобы каждый последующий ряд цепей был смещен на некоторый угол, что улучшает транспортировку материала по печи
|
Звеньевые теплообменники. Звенья цепей, соединенные шарнирами. При вращении печи цепи погружаются в слой материала и передают тепло материалу. Данный теплообменник работает при температурах 1100ºС, изменяет производительность печи на 10-12%, снижает расход топлива на 5-12%.
Более эффективны теплообменники ячейкового, шарнирно-винтового, циклоидного типа, оснащены пересыпающими лопастями из тугоплавких металлов (Х23Н18), кирпича или керамики. Принцип действия теплообменников основан на расчленении единого потока на несколько потоков меньшего сечения – увеличивается поверхность теплообмена, существенно уменьшается термическое сопротивление и увеличивается теплообмен. Теплообменники работают в условиях более высоких температур.
СУХОЙ СПОСОБ
При сухом способе производства применяют короткие печи, процессы, происходящие в 1-2 или 1-2-3 зонах выполняют в запечных теплообменных устройствах – циклонных теплообменниках, декарбонизаторах. Циклонные теплообменники могут отличаться конструкцией: двухветвевые,
Обжигают сырьевую муку в коротких вращающихся печах с предварительной тепловой обработкой:
v в циклонных теплообменниках, в которых отходящими из печей газами материал нагревается до 800-850˚С и частично декарбонизируется (на 30-40%)
v в циклонных теплообменниках и далее в специальных реакторах- декарбонизаторах, в которых температура муки повышается до 920-950˚С, а декарбонизация материала перед его поступлением в печь достигает 85-90%.
Как за рубежом, так и в России подавляющее число строящихся заводов проектируются для обжига сухой сырьевой шихты во вращающихся печах с циклонными теплообменниками, в которых тепловая подготовка шихты осуществляется во взвешенном состоянии в газоходах и циклонах за счет тепла отходящих из печи газов температурой 1000—1100 °С. Проходя циклонный теплообменник за 20—25 сек, шихта нагревается до температуры 800—850 °С и декарбонизируется, примерно, на 15%.
Существуют серьезные проблемы обжига сырьевой муки. В ходе обжига в печах с циклонными теплообменниками сырьевой шихты с повышенным содержанием щелочей, при температуре выше 800 °С щелочи начинают возгоняться и переносятся вместе с топочными газами в более холодные зоны, где конденсируются на стенках циклонного теплообменника (особенно в загрузочной головке) и материале. Это обстоятельство в отдельных случаях приводит к образованию настылей, мешающих нормальному ведению процесса обжига. В клинкере остается больше щелочных оксидов (К2О и Nа20), цементный камень характеризуется высолами, комкуется при хранении и приобретает еще ряд нежелательных характеристик. Пыль, выносимая из теплообменника отходящими газами, во избежание превышения содержания щелочей в клинкере выше нормативной величины, не может быть возвращена обратно в процесс обжига (пылеунос в печи достигает 5%)
|
Сущность процесса заключается в том, что под действием собственного веса материал движется сверху вниз через циклоны и газоходы ступеней теплообменника навстречу потоку газов, отходящих с печи обжига, при этом происходит нагрев смеси, дегидратация глинистых минералов и начинается процесс декарбонизации, полностью декарбонизация не происходит – приблизительно 15-18% известняка декарбонизируется.
К недостаткам печных установок с циклонными теплообменниками следует отнести сравнительно низкую стойкость футеровки в печи на участке начала зоны высоких температур, в печах с запечными теплообменниками продолжительность кампании футеровки в 2—5 раз меньше, чем в печах для обжига шлама и составляет, в зависимости от эксплуатационных факторов 80—140 суток. Основной причиной является нестабильность положения и протяженности зоны кальцинирования, которая возникает в результате поступления в печь дисперсного порошка сильно аэрированного газами и воздухом, захваченными при прохождении через теплообменник и загрузочную головку При отсутствии возможности организовать управление или регулирование движением такого потока материала, даже незначительное изменение какого-либо из факторов, влияющее на скорость движения (температура, химсостав шихты, наличие примесей и т. д.) приводит к нарушению режима движения материала по печи. При этом происходит быстрое изменение положения границ зоны спекания и смена температуры обмазки, приводящие к срыву ее с примыкающим к ней слоем огнеупора. Это явление при частой повторяемости и является причиной быстрого разрушения футеровки в начале зоны спекания.
По опытным данным количество ремонтов в начале зоны спекания примерно в 1,5 раза больше, чем на других участках зоны
При обжиге в печах с циклонными теплообменниками сырьевой шихты с повышенным содержанием щелочей в элементах теплообменника (загрузочная головка, газоходы, циклоны и течки) и в клинкере остается больше щелочных оксидов (К2О и Nа20), чем в печных установках других конструкций. В ходе обжига при температуре выше 800 °С щелочи начинают возгоняться и переносятся вместе с топочными газами в более холодные зоны, где и конденсируются на стенках циклонного теплообменника и материале, особенно в загрузочной головке и газоходе I ступени. Это обстоятельство в отдельных случаях приводит к образованию настылей, мешающих нормальному ведению процесса обжига. Помимо этого, пыль, выносимая из теплообменника отходящими газами, во избежание превышения содержания щелочей в клинкере выше нормативной величины, не может быть возвращена обратно в процесс обжига.
В современной практике применяют не циклонные теплообменники, а шахтно-циклонные более простой конструкции. Замена циклонов шахтой снижает аэродинамическое сопротивление.
Для улучшения условий работы футеровки и повышения срока ее службы, а также увеличения удельной загрузки печи при обеспечении стабильности теплового режима работы и возможности регулирования процесса декарбонизации оказалось целесообразным перенести процесс декарбонизации материала полностью или частично из вращающейся печи в специальное устройство «декарбонизатор».
Декарбонизатор- интенсивный нагрев в вихревой камере, оснащенной вихревой горелкой и тангенциально расположенными патрубками
В циклонных теплообменниках с декарбонизаторами (кальцинаторами) процесс декарбонизации материал почти полностью (примерно на 90%) проходит в теплообменнике. Этот процесс во всех конструкциях декарбонизаторов протекает температуре газов ~900°С с минимальной разностью температур между газом и материалом- примерно 50 °С. Этот эффект достигается за счет суспендирования частиц материала в газах и сжигания в топке декарбонизатора примерно 60 % топлива. При этом расход топлива в самой печи уменьшается вдвое и составляет примерно 40% от общего расхода топлива. Однако, чтобы печь могла работать в нормальном тепловом режиме, в ней нужно сжигать такое количество топлива, при котором скорости газов в печи достигнут расчетных величин. В результате производительность печи может быть увеличена вдвое.
На рис. представлена схема работы декарбонизатораRSР фирмы «Онода» — (Япония). Как показано на схеме, сырьевая шихта из циклона II ступени при температуре около 700°С спускается в вихревой кальцинатор и равномерно рассеивается по его сечению тангенциально подводимым горячим воздухом с температурой 650°С из холодильника. При этом достигается интенсивный теплообмен между материалом и продуктами горения топлива. Декарбонизатор установлен параллельно выходящему
от печи газоходу (смесителю), соединяющему загрузочную головку с циклоном I ст.
Декарбонизатор состоит из двух камер (топок): вихревой горелки — 7 и вихревого кальцинатора — 10. Вихревая камера оборудована горелкой — 7, служащей для розжига и поддержания устойчивого и интенсивного горения факелов форсунок (горелок) — 9 вихревого кальцинатора. Вихревой кальцинатор оборудован тремя рядами форсунок, которые установлены перпендикулярно к образующей кальцинатора. Устойчивое горение топлива в форсунках (горелках) вихревой горелки и кальцинатора поддерживается горячим избыточным воздухом от холодильника.
Выходящие из декарбонизатора газы поступают в смесительную камеру, где происходит их смешение с выходящими из печи газами, а затем смесь газов поступает в нижний циклон.
В самой печи осуществляется только завершение процесса декарбонизации, а также окончание незавершенных процессов клинкерообразования. Заданный тепловой режим в кальцинаторе поддерживается регулированием подачи топлива в горелки (форсунки).
При увеличении производительности печи примерно вдвое уменьшаются соответственно и потери тепла корпусом печи и циклонного теплообменника в окружающую среду, в результате чего удельный расход тепла на обжиг в установке с теплообменником и кальцинатором снижается примерно на 5-6%.
По данным фирмы «Онода» и др. источников, при применении кальцинаторов типа RSР производительность печных установок с циклонными теплообменниками может быть увеличена в 2-3 раза. Кроме того, исследованиями установлено, что благодаря сжиганию топлива в декарбонизаторах (около 60%) в условиях быстрого перепада температур газов при общем более низком температурном режиме обеспечивается значительное (в 2,5-3 раза) снижение содержания оксидов азота (N02) в отходящих от установки газах. Одновременно снижается возгонка и улетучивание сульфатов с отходящими газами.
Рис. Схема работы циклонных теплообменников с декарбонизатором системы RSP
1, 3, 5. 6—циклоны; 2 — газоходы; 4 — отходящие газы; 7 — горелка вихревой камеры; 8 — вихревая камера; 9 — боковая горелка кальцинатора; 10—вихревой кальцинатор; 11 — воздуховод; 12—циклон; 13 —колосниковый холодильник; 14 — вращающаяся печь; 15— загрузочная головка
Пылеочистка
Топочные газы проходят по печи, отдают тепло материалу, насыщаются пылевидными частицами (при трении сырья, клинкера о футеровку печи, между собой) и поступают в пылеосадительную систему, где очищаются до требований санитарных норм и выбрасываются в атмосферу. Пылеосадительная система включает: пылеосадительную камеру, циклоны, рукавные фильтры, электрофильтры.
пылеосадительная камера
шахтная аспирационная колонна
циклон
рукавный фильтр
электрофильтр
В пылеосадительной камере и аспирационной шахте обеспечивается грубая очистка, осаждаются крупные частицы, в батарее циклонов обеспечивается следующий этап очистки ≈ на 90%, полная очистка происходит в рукавных фильтрах и электрофильтрах, выбрасываемые газы должны содержать не более 8 мг цемента/ м3. Для очистки от углекислого газа, двуокиси азота, серного ангидрита применяют химические сорбенты. При применении сухого способа объем печных газов уменьшается на 35-40 %, снижается стоимость обеспыливания.
Уловленная пыль возвращается на технологию. При мокром способе производства для возврата пыли в печь существует несколько схем: вдувание пыли с загрузочного конца печи; вдувание за цепную завесу под слой материала, по специальному трубопроводу в зону спекания.
Все приведенные схемы не лишены недостатков, так если вдувание с холодного конца печи, то произойдет замазывание теплообменников, в зону спекания – сложно и пыль подхватывается потоком газов и вновь выносится из печи, наиболее эффективно вдувание за цепной завесой.
При сухом способе производстве отходящие газы из теплообменника через запечный дымосос направляются направляют в агрегат помола а затем на очистку.
41. Оборудование для обжига, направления повышения эффективности печных агрегатов. (+смотреть вопрос 40)
Клинкер по сухому способу во вращающихся печах с циклонными теплообменниками, а в новейших системах в сочетании с реакторами (декарбонизаторами) получают по технологической схеме (при использовании известняка и глины), изображенной на 27.
Добывают известняк и глину с учетом их свойств теми же приемами, какие используются при мокром способе производства. Последующая их переработка (дробление, измельчение, смешение компонентов) определяется спецификой сухого способа производства. Добытый известняк вначале подвергают двухстадийному, а иногда одностадийному дроблению до кусков размером 1—3 см. Для этой цели на новых предприятиях часто используют передвижные механизмы, например молотковые дробилки соответствующей производительности. Полученную щебенку направляют на усредиительиый склад, где с помощью комплекса машин осуществляется первичная гомогенизация сырья. Добытую глину вначале также подвергают дроблению при одновременной сушке с последующей подачей полученного материала на усредиительиый склад для гомогенизации. С этих складов известняк и глину направляют через автоматические дозаторы в требуемом соотношении по массе в шаровые мельницы, где осуществляются сушка и тонкий помол •сырья. Для сушки в мельницы направляют дымовые газы, образующиеся во вращающихся печах при сжигании топлива. Шаровые мельницы часто работают в замкнутом цикле с сепараторами (проходными или центробежными). Из мельниц мука в виде пылегазовой смеси направляется в осадительные циклоны, а затем в горизонтальные электрофильтры, в которых выделяется твердая фаза. Иногда для оптимизации работы оборудования в линии устанавливаются охладители газов, в которые в необходимом количестве пульверизируется вода. При этом температура газов, поступающих в электрофильтры, должна держаться на уровне 120—140 °С. В этих условиях остаточное содержание пыли в газах, выбрасываемых в атмосферу, доводится до санитарных норм (75—90 мг/м3).
На крупных предприятиях с производительностью одной технологической линии 3000 т клинкера в сутки устанавливают две шаровые мельницы размером 4,2X10 м, дающие 120—130 т/ч муки с остатком 10—12 % на сите № 008.
В настоящее время все шире начинают применять каскадные мельницы без мелющих тел типа «Аэрофол», сырьевые материалы в которых измельчаются под действием падающих кусков самого материала. Эти мельницы применяют для измельчения сырья с влажностью до 20%, а по ряду данных и с большей влажностью. Выпускают их в разных странах в виде барабанов диаметром 5—9 и длиной до 1—2,4 м. Сырье загружают кусками размером до 30—50 см. В мельницу подают горячие газы, которые сушат материал до влажности 0,5— 1 %. Эти же газы выносят измельченный продукт, который затем выделяется из потока в проходных сепараторах и циклонах, причем более крупные частицы возвращаются на домол. Иногда после такой мельницы устанавливают обыкновенную шаровую для домола материала. Расход электроэнергии на помол материалов в бесшаровых мельницах уменьшается по сравнению с расходами на помол в трубных мельницах примерно на 25%- Производительность таких мельниц 250—300 т/ч и более.
Сырьевая мука, получаемая в результате помола в мельницах того или иного типа, направляется на гомогенизацию и корректирование в специальные железобетонные силосы вместимостью до 500—2000 м3 (в зависимости от масштабов производства и однородности сырья). Чем неоднороднее сырье, тем меньше обычно вместимость отдельных силосов. Муку в них перемешивают сжатым воздухом, вводимым через керамические пористые плитки, укладываемые на днище силосов. Иногда вместо керамических применяют специальные металлические плитки или даже перфорированные трубы, покрытые тканью. Воздушные струи, проникающие в муку, аэрируют ее, что сопровождается уменьшением насыпной плотности. Одновременно материал приобретает большую текучесть.
После гомогенизации проверяют состав сырьевой муки по содержанию оксида кальция (титр муки). Если оно соответствует требуемому, то смесь направляют на обжиг. Если же выявляется отклонение, то муку из двух силосов направляют в третий в таком соотношении, чтобы получить смесь требуемого состава. После заполнения общего силоса материалы в нем тщательно перемешивают до полной однородности.
При использовании способа непрерывной гомогенизации мука непрерывно подается на верх большого силоса, заполненного уже аэрированной и гомогенизированной смесью. Одновременно у днища силоса непрерывно отбирается готовый материал. Вместимость силоса принимается равной 8—10-кратной часовой производительности мельниц. Высота силосов в 1,5—2 раза больше их диаметра.
Для перемешивания применяют обычно воздух, очищенный от масла и паров воды, под давлением до 0,15— 0,2 МПа. Через 1 м2 пористых плиток подается в 1 мин около 2 м3 воздуха. Затраты электроэнергии на гомогенизацию составляют 0,4—0,6 кВт-ч на 1 т муки; общий расход энергии на всю установку (подача материала в. силосы, его выгрузка и перемешивание) 2,2—2,5 кВтХХч/т. В месте выхода готовой муки из силосов устанавливают пробоотборники, автоматически отбирающие пробы массой 10—15 г/т материала. Силосы снабжают также устройствами для обеспыливания отработанного воздуха и удаления воздуха из готовой муки.
В тех случаях, когда муку обжигают во вращающихся печах, снабженных циклонными теплообменниками, сухую смесь из силосов с помощью пневмонасосов того или иного типа направляют в приемный бункер 8 печной установки (28). Отсюда элеватором 7 материал подают на ленточный конвейер-дозатор 6, передающий его в газоход батарейного циклона 4. Здесь он подхватывается отходящими газами из циклона 5 и поступает в циклон 4. Далее таким же образом он проходит газоходы и циклоны 5, 3, 9 и поступает в печь 10. Во время перемещения по газоходам и циклонам сырьевая мука постепенно нагревается и поступает в циклон 9 с температурой 800—850 °С частично (на 30—40%) декарбонизированной. Нагревается мука в газовом потоке циклонных теплообменников очень интенсивно. Циклоны 3 и 9 изнутри футеруют огнеупорами. Газы через систему циклонов движутся под действием дымососа 1. Отработанные газы с температурой 200—300 °С очищаются от пыли в циклоне 2 и в электрофильтрах или же сначала используются для сушки муки.
Вращающиеся печи с циклонными теплообменниками имеют размеры 5X75 и 7X95 м, их суточная производительность 1600 и 3000 т. Расход топлива 3250— 3500 кДж на 1 кг клинкера. Мощные печи оснащают двумя ветвями четырехступенчатых теплообменников.
В материале, обжигаемом в рассматриваемых печах, идут те же процессы, что и при обжиге смеси в виде шлама. Полученный клинкер после охлаждения в холодильниках того или иного типа направляют на склад, а затем перерабатывают в цемент.
В последнее десятилетие печные агрегаты с циклонными теплообменниками получили дальнейшее существенное развитие [3]. Был предложен обжиг сырьевой муки по схеме циклонный теплообменник — декарбони-затор— вращающаяся печь. Известно, что около 60% общего количества теплоты, необходимой для получения клинкера, расходуется на декарбонизацию сырьевой муки. В соответствии с этим в новых конструкциях печных агрегатов материал после теплообменников в потоке газов с температурой 800—850 °С поступает з зону, где температура повышается до 1000—1050 °С благодаря сжиганию здесь дополнительного количества топлива. В этой зоне, называемой реактором, в среде раскаленных газов при вихреобразном движении пылевидные частички в течение 70—80 с подвергаются почти полной декарбонизации (85—90%). Отсюда материал с температурой 900—950 °С поступает во вращающуюся печь, где завершаются процессы клинкерообразования и последующего охлаждения продукта. Важно отметить, что почти полная декарбонизация материала и высокая его температура при поступлении в печь дают возможность устанавливать ее с уклоном 3,5—4° и в два-три раза увеличивать частоту ее вращения.
Вынос наиболее теплоемкого процесса декарбонизации из вращающейся печи в специальный реактор с подачей сюда большей части топлива дает высокий технический эффект. Так, по производственным данным, если печи с циклонными теплообменниками дают в сутки около 1,5 т клинкера с 1 м3 объема печи, то у печей, работающих с декарбоыизатором, удельная производительность увеличивается вдвое и более при практически одинаковом расходе топлива (3200—3300 кДж/кг клинкера).
В настоящее время печные агрегаты, работающие по схеме циклонные теплообменники — реакторы — печь, получили значительное применение в Японии. Здесь созданы, в частности, различные типы реакторов-декарбонизаторов, включенных в технологические линии производительностью до 3000—5000 т и более клинкера в сутки. В других странах известны обжиговые агрегаты системы «Дополь», в которых последняя ступень теплооб* менников имеет вид шахты, выполняющей роль декар-бонизатора.
На 29 представлена схема обжига клинкера с использованием теплообменников и декарбонизаторов, применяемая на некоторых заводах в Японии. Сырьевая мука, пройдя циклоны, поступает в декарбонизатор, куда также подается топливо и вторичный воздух из холодильника 7 по газоходу 4. Во вращающуюся печь 5 материал поступает с температурой около 1000 °С, почти полностью декарбонизированный и подготовленный к завершающим реакциям образования клинкера.
Как уже указывалось, сырьевую муку при сухом способе производства можно обжигать во вращающихся печах, работающих в сочетании с конвейерными кальцина-торами (печи «Леполь»), а также в шахтных. В том и в другом случаях муку до поступления на обжиг гранулируют и получают гранулы размером от 5—10 до 20— 30 мм. В настоящее время для этой цели используют тарельчатые грануляторы вместо ранее распространенных барабанных.
Вращающиеся печи в сочетании с кальцинаторами (печи «Леполь») характеризуются суточной производительностью 1000—3000 т. Установка, рассчитанная на выпуск 1800 т/сут, состоит из печи размером 5X85 м и кальцинатора с площадью решетки 200 м2. Расход теплоты в печах с кальцина торами примерно 3150— 3550 кДж/кг клинкера. Из вращающейся печи клинкер направляется в холодильник и далее на склад и помол.
Вращающиеся печи с кальцинаторами, часто работающие с пониженными коэффициентами использования по времени (не более 0,8—0,85) и плохо поддающиеся автоматизации, в последние годы реконструируются и переводятся на работу с теплообменниками, что способствует значительному сокращению удельных расходов труда, топлива и электроэнергии и повышению производительности печей.
Шахтные печи рассчитаны на производительность 150—250 т клинкера в сутки. Они работают на короткопламенных видах топлива (антрацит, кокс). Эти печи характеризуются пониженным расходом теплоты—3750—4600 кДж на 1 кг клинкера. Вместе с тем по качеству получаемого клинкера эти печи уступают вращающимся. В СССР в шахтных печах выпускается лишь около 3—4 % всего цемента.
Процесс обжига клинкера в современных шахтных печах полностью автоматизирован. Высота шахты 8 — 10, диаметр 2,5—2,8 м. Печь конструкции Гипроцемента имеет высоту 8 и внутренний диаметр 2,85 м. Мощность ее до 250 т клинкера в сутки при расходе теплоты 4200 кДж/кг. В печи обжигается сырьевая мука, смешаиная с топливной крупкой и подвергнутая грануляции. Сырьевая мука и топливная крупка из отдельных бункеров, размещенных над шахтой, с помощью ленточных весовых дозаторов направляются в строго установленном количестве в смесительный шнек, а далее в тарельчатый гранулятор. Отсюда гранулы вращающейся воронкой загружаются в печь, где распределяются ровным слоем. Топливо сгорает за счет воздуха, подаваемого под разгрузочную решетку в низ печи под давлением 25—30 кПа. Часть воздуха поступает непосредственно в зону горения. Предусмотрена также возможность введения некоторого количества воздуха, обогащенного кислородом, в зону интенсивного горения топлива.
Готовый клинкер разгружается с помощью решетки, которая может вращаться с разной скоростью в зависимости от протекания процесса обжига. Чтобы предотвратить выбивание воздуха из печи, при выгрузке продукта устанавливают двух- или трехшлюзовый затвор. Верхнюю часть печи футеруют огнеупором, а внизу устанавливают чугунные кольца, лучше выдерживающие абразивное действие клинкера.
При обжиге материала в шахтных печах сырьевые гранулы вначале подвергаются сушке отходящими дымовыми газами. Затем по мере перемещения их вниз в зону более высоких температур и нагревания до 400— 500 °С в них проходит дегидратация глинистых минералов. В это время начинается горение топлива (антрацита, кокса с содержанием летучих не более 3—5 %), находящегося в гранулах. Это резко повышает температуру материала, что сопровождается декарбонизацией известняка и выделением С02.
Углекислый газ способен взаимодействовать с углеродом по реакции: C-J-C02=F^2CO. Образование СО в массе материала сопровождается возникновением среды, которая может вызвать восстановление оксида железа до Fe304 или FeO, ухудшающих качество клинкера и облегчающих спекание материала в крупные куски и его привары к стенкам печи. Для предотвращения таких нежелательных явлений следует часть воздуха, необходимого для горения топлива, вводить в зону спекания материала. Все это осложняет управление процессами обжига и клинкерообразования в шахтных печах и приводит иногда к снижению качества продукта.
Образовавшийся клинкер в нижней части печи интенсивно охлаждается. Затем его выгружают и направляют, как обычно, на склад и помол.
Разрабатываются также новые способы обжига сырьевых смесей, в частности в «кипящем» слое. Сущность этого способа заключается в том, что через слой мелкозернистой или гранулированной сырьевой смеси просасываются снизу вверх горячие газы со скоростью 1,5— 3 м/с, при которой гранулы находятся в непрерывном возвратно-поступательном движении (в «кипящем» состоянии). При этом происходит интенсивный теплообмен между газами с температурой 1350—1450 °С и материалом.
Ряд исследований показал, что в этих условиях обжиг гранул размером 2—5 мм заканчивается в течение 30—40 мин, причем получаются цементы высоких марок.
По опытам П. Г. Романкова, А. Б. Рашковской, М. М. Сычева и других, при использовании реактора вихревого типа цикл клинкерообразования заканчивается в течение 5—6 мин. Изучается возможность обжига сырьевой муки во взвешенном состоянии в потоке горячих газов с использованием для этой цели топок циклонного типа. Проводятся исследования электротермической обработки сырьевых смесей.
Большой интерес в создании принципиально новой технологии цемента представляют опыты, проведенные сотрудниками Гипроцемента (Н. А. Олесов, И. Г. Абрам-сон, Б. В. Волконский, С. И. Данюшевский и др.) и Института электрофизической аппаратуры им Д. В. Ефремова (В. А. Глухих, Б. И. Альбертинский и др.). Они подвергли облучению ускоренными электронами образцы из сырьевой портлаидцементиои смеси и обнаружили практически полное завершение реакций синтеза клинкера в течение 5—15 с при энергопотреблении 3300± ±300 Дж/г. Клинкер через 28 сут твердения показал прочность 50 МПа. Авторы преимуществами радиацион-ио-химического способа изготовления цементного клинкера считают следующее: скорость протекания реакций клинкерообразования в 100 раз выше обычной, что создает предпосылки для коренного уменьшения габаритов и металлоемкости производственных агрегатов; отказ от применения природного топлива; резкое уменьшение вредных выбросов в атмосферу и повышение уровня технической культуры производства
42. Процессы помола портландцементного клинкера. Требования по зерновому составу и его влияние на свойства цемента.
ПОМОЛ ЦЕМЕНТНОГО КЛИНКЕРА
Важным фактором, позволяющим регулир
|
|
Состав сооружений: решетки и песколовки: Решетки – это первое устройство в схеме очистных сооружений. Они представляют...
Особенности сооружения опор в сложных условиях: Сооружение ВЛ в районах с суровыми климатическими и тяжелыми геологическими условиями...
Автоматическое растормаживание колес: Тормозные устройства колес предназначены для уменьшения длины пробега и улучшения маневрирования ВС при...
Адаптации растений и животных к жизни в горах: Большое значение для жизни организмов в горах имеют степень расчленения, крутизна и экспозиционные различия склонов...
© cyberpedia.su 2017-2024 - Не является автором материалов. Исключительное право сохранено за автором текста.
Если вы не хотите, чтобы данный материал был у нас на сайте, перейдите по ссылке: Нарушение авторских прав. Мы поможем в написании вашей работы!