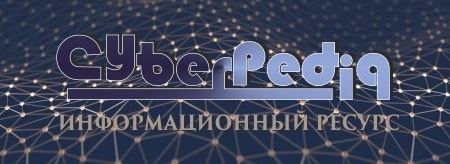
Состав сооружений: решетки и песколовки: Решетки – это первое устройство в схеме очистных сооружений. Они представляют...
Адаптации растений и животных к жизни в горах: Большое значение для жизни организмов в горах имеют степень расчленения, крутизна и экспозиционные различия склонов...
Топ:
Процедура выполнения команд. Рабочий цикл процессора: Функционирование процессора в основном состоит из повторяющихся рабочих циклов, каждый из которых соответствует...
Особенности труда и отдыха в условиях низких температур: К работам при низких температурах на открытом воздухе и в не отапливаемых помещениях допускаются лица не моложе 18 лет, прошедшие...
Организация стока поверхностных вод: Наибольшее количество влаги на земном шаре испаряется с поверхности морей и океанов...
Интересное:
Берегоукрепление оползневых склонов: На прибрежных склонах основной причиной развития оползневых процессов является подмыв водами рек естественных склонов...
Мероприятия для защиты от морозного пучения грунтов: Инженерная защита от морозного (криогенного) пучения грунтов необходима для легких малоэтажных зданий и других сооружений...
Наиболее распространенные виды рака: Раковая опухоль — это самостоятельное новообразование, которое может возникнуть и от повышенного давления...
Дисциплины:
![]() |
![]() |
5.00
из
|
Заказать работу |
|
|
Мощность резания
Для разрушения материала срезаемого слоя и превращения его в стружку необходимо затратить некоторое количество энергии и произвести работу резания. Мощность, затрачиваемая на процесс резания, называется эффективной мощностью Ne (кВт), которую рассчитываем по формуле:Ne= Pz*V/60*1020
Эффективная мощность должна быть меньше мощности привода главного движения:
Ne меньше или равно N=1,1кВт,
При черновом точении:Ne=529*141/60*1020=1,2 кВт,
При чистовом точении:Ne=334*141/60*1020=0,8 кВт.
3. Основные размеры станка определяют предельные размеры обрабатываемых поверхностей или режущего инструмента. Так, например, для сверлильного станка основной размер однозначно определяет наибольший диаметр сверления. Однако наибольший диаметр отверстия, обрабатываемого зенкером, и наименьший диаметр сверления должны быть определены на основании дополнительных требований: можно при - 1.76. К определению наи - нять, что наибольший диаметр отверстия, обра-большего диаметра детали, батываемого зенкером, следует взять больше обрабатываемой на токарном диаметра сверления на величину припуска, станке оставляемого на зенкерование.
Фасонные резцы
Фасонные резцы относятся к нестандартным резцам.
Фасонные резцы применяют для обработки деталей со сложной формой образующей. По сравнению с обычными резцами они обеспечивают идентичность формы, точность размеров детали, которая зависит в основном от точности изготовления резца, высокую производительность благодаря одновременной обработке всех участков фасонного профиля детали и большую экономию машинного времени. Резцы проектируют для обработки конкретной детали, и их применение экономически оправдано в крупносерийном и массовом производстве.
|
Рис. 1. Формы фасонных резцов.
![]() | ![]() |
![]() |
Фасонные резцы классифицируют по следующим признакам:
1. По форме - стержневые (рис. 1, а), призматические (рис. 1, б) и круглые (рис. 1, в).
2. По направлению подачи: радиальные (рис. 2,а) и тангенциальные (Рис. 2, б).
Рис. 2. Радиальный и тангенциальный фасонные резцы. Sr — радиальная подача резца, St — тангенциальная подача.
3. По расположению оси отверстия или установочной базы резца по отношению к оси вращения заготовки: с параллельным или наклонным расположением.
4. По конструкции: цельные и составные, например, с припаянными пластинами из твёрдого сплава.
Таблица 1
Развертки.
Применяют для окончательной обработки отверстий с целью получения высокой точности и меньших параметров шероховатости поверхности.
Режущая часть развертки (рис. 5.11) расположена к оси под углом 2φ и выполняет основную работу резания.
Для обработки вязких металлов φ=12-:-15°, для хрупких и твердых материалов φ=3-:-5°.
Рис. 5.11. Типы разверток:
а — части и элементы разверток, б — машинная развертка с цилиндрическим хвостовиком, в — машинная развертка с коническим хвостовиком, г — машинная развертка со вставными ножами, д — насадная развертка, оснащенная пластинками твердого сплава
|
Твердосплавные развертки имеют угол φ= 30-:-45°. Направляющий конус развертки расположен под углом 45°. Он направляет развертку, предохраняя ее зубья от повреждения. Задний угол α на режущей части принимается от 6 до 15°. На калибрующей части угол α обычно равен нулю. Передний угол γ принимается от 0 до 15°. Для хрупких металлов γ = 0°. для твердосплавных разверток γ от 0 до —5°.
По своей конструкции и назначению развертки делятся на ручные и машинные, цилиндрические и конические, насадные и цельные.
Ручные развертки изготовляют с цилиндрическим хвостовиком; ими вручную обрабатывают отверстия диаметром от 3 до 50 мм.
Машинные развертки выпускают с цилиндрическими и коническими хвостовиками и используют для развертывания отверстий диаметром от 3 до 100 мм. Обрабатывают отверстия этими развертками на сверлильном или токарном станке.
Насадные развертки служат для развертывания отверстий диаметром от 25 до 300 мм. Их насаживают на специальную оправку, имеющую конический хвостовик для крепления на станке. Насадные развертки изготовляют из быстрорежущей стали или оснащают пластинками из твердых сплавов.
Конические развертки применяют для развертывания конических отверстий. Обычно в комплект входят две развертки: черновая и чистовая.
Цельные развертки изготовляют из инструментальной углеродистой легированной или быстрорежущей стали.
При развертывании отверстий в твердых металлах используют развертки, оснащенные пластинками твердого сплава, обладающие по сравнению с быстрорежущими развертками большей износоустойчивостью.
Расточные инструменты
Расточные инструменты применяются для увеличения диаметров отверстий и являются широко универсальными инструментами, так как, в отличие отзенкеров, разверток и других инструментов, допускают регулировку (настройку) режущих кромок в радиальном направлении.
Расточными инструментами обрабатывают отверстия диаметром 1... 1000 мм и более с точностью JT5...JT6 и шероховатостью Ra 0,8...1,6.
В механообработке нашли применение следующие типы расточных инструментов: 1) стержневые резцы; 2) двухсторонние пластинчатые резцы-блоки; 3) расточные головки для обработки неглубоких отверстий; 4) расточные головки для обработки глубоких отверстий.
Стержневые резцы имеют одну режущую кромку из быстрорежущей стали или в виде СМП из твердого сплава или сверхтвердых материалов.
Державки стержневых резцов в поперечном сечении имеют круглую, квадратную или прямоугольную формы. Наиболее простой и распространенный способ закрепления резца с державкой квадратной или круглой формы показан на рис. 1, а. Здесь резец 2 закреплен винтом 3 в оправке l; вылет резца регулируется винтом 4.
![]() ![]() ![]() ![]() ![]() ![]() |
|
|
|
10. ответ
Тема 11.1. Опоры. Подшипники скольжения
Тема 11.2. Oпоры. Подшипники качения
Содержание лекции
Общие сведения
Разновидности подшипников
Конструкции подшипников скольжения
Достоинства и недостатки подшипников скольжения
Принцип работы подшипника скольжения
Материалы вкладышей
Смазочные материалы
Виды разрушения вкладышей
Критерии работоспособности. Условный расчет подшипников скольжения
Общие сведения
Валы и вращающиеся оси монтируют на опорах, которые определяют положение вала или оси, обеспечивают вращение, воспринимают положение вала или оси, обеспечивают вращение, воспринимают нагрузки и передают их основанию машины. Основной частью опор являются подшипники, которые могут воспринимать радиальные, радиально-осевые и осевые нагрузки; в последнем случае опора называется подпятником, а подшипник носит название упорного. Подшипники вращающихся осей некоторых транспортных средств с преобладающей вертикальной нагрузкой называют буксами.
Разновидности подшипников
По принципу работы различают
1) подшипники скольжения, в которых цапфа вала скользит по опорной поверхности,
2) подшипники качения, в которых между поверхностью вращения детали и опорной поверхностью расположены тела качения.
Материалы вкладышей
Материалы вкладышей подшипников должны иметь:
1. Достаточную износостойкость и высокую сопротивляемость заеданию в периоды отсутствия жидкостной смазки (пуск, торможение и др.). Изнашиванию должны подвергаться вкладыши, а не цапфа вала, так как замена вала значительно дороже вкладыша. Подшипник скольжения работает тем надежнее, чем выше твердость цапфы вала. Цапфы, как правило, закаливают.
2. Высокую сопротивляемость хрупкому разрушению при действии ударных нагрузок и достаточное сопротивление усталости. 3. Низкий коэффициент трения и высокую теплопроводность с малым расши-рением.
Вкладыши выполняют из следующих материалов:
1) Бронзовые вкладыши широко используют при средних скоростях и больших нагрузках. Наилучшими антифрикционными свойствами обладают оловянные бронзы (БрО10Ф1, Бр05Ц5С5 и др.). Алюминиевые (БрАЭЖЗА и др.) и свинцовые (БрСЗО) бронзы вызывают повышенное изнашивание цапф валов, поэтому применяются в паре с закаленными цапфами. Свинцовые бронзы используют при знакопеременных ударных нагрузках.
2) Вкладыш с баббитовой заливкой применяют для ответственных подшипников при тяжелых и средних режимах работы (дизели, компрессоры и др.). Баббит является одним из лучших антифрикционных материалов для подшипников скольжения. Хорошо прирабатывается, стоек против заедания, но имеет невысокую прочность, поэтому баббит заливают лишь тонким слоем на рабочую поверхность стального, чугунного или бронзового вкладыша. Лучшими являются высокооловянные баббиты Б86, Б83.
3)Чугунные вкладыши без заливки применяют в неответственных тихоходных механизмах. Наибольшее применение получили антифрикционные чугуны АЧС-1
4) Металлокерамические вкладыши изготовляют прессованием и последующим спеканием порошков меди или железа с добавлением графита, олова или свинца. Особенностью этих материалов является большая пористость, которая используется для предварительного насыщения горячим маслом. Вкладыши, пропитанные маслом, могут долго работать без подвода смазочного материала. Их применяют в тихоходных механизмах в местах, труднодоступных для подвода масла.
5) Неметаллические материалы для вкладышей применяют антифрикционные самосмазывающие пластмассы (АСП), древеснослоистые пластики, твердые породы дерева, резину и др. Неметаллические материалы устойчивы против заедания, хорошо прирабатываются, могут работать при смазывании водой, что имеет существенное значение для подшипников гребных винтов, насосов, пищевых машин и т. п.
В массовом производстве вкладыши штампуют из стальной ленты, на которую нанесен тонкий антифрикционный слой (оловянные и свинцовые бронзы, баббиты, фторопласт, нейлон и др.).
Смазочные материалы
Для уменьшения трения и изнашивания подшипники смазывают смазочными материалами, которые должны быть маслянистыми и вязкими. Маслянистостью называется способность смазочного материала образовывать на поверхности трения устойчивые адсорбированные пленки.
Вязкостью называется объемное свойство смазочного материала оказывать сопротивление относительному перемещению его слоев. В технических характеристиках масел указывают так называемую кинематическую вязкость — V в мм2/с, которая зависит от плотности. Эта вязкость приводится в справочной литературе при температурах, приближающихся к рабочим, чаще всего при 50 и 100 °С. Вязкость является важнейшим свойством масел, определяющим их смазывающую способность. Она существенно понижается с ростом температуры.
Смазочные материалы могут быть жидкими, пластичными (густыми), твердыми и газообразными.
Жидкие масла являются основным смазочным материалом. Они имеют низкий коэффициент внутреннего трения, их легко подавать к местам смазывания, они оказывают охлаждающее действие. Недостатком является вытекание масла из мест смазывания. Жидкие масла бывают органические и минеральные.
Органические масла — растительные (касторовое и др.) и животные (костный жир и др.) — обладают высокими смазывающими свойствами, но дефицитны и применяются в специальных случаях. Минеральные масла — продукты перегонки нефти — находят преимущественное применение для подшипников. К ним относят индустриальные масла различных марок, моторные и др.
Вода применяется для смазывания подшипников с вкладышами из дерева, резины и некоторых пластмасс.
Пластичный смазочный материал (мази) изготовляют путем загущения жидких минеральных масел мылами жирных кислот или углеводородами. К ним относятся солидолы, консталины и др. Эти мази хорошо заполняют зазоры, герметизируя узлы трения. Вязкость их мало меняется с изменением температуры. Применяются в подшипниках при малых скоростях скольжения и ударных нагрузках.
Твердые смазочные материалы — графит, слюда и др.— прменяются в машинах, когда по условиям производства нельзя применить жидкие масла или мази (ткацкие станки, пищевые машины и др.).
Газообразные смазочные материалы — воздух, пары углеводородов и др.— применяются в малонагруженных подшипниках при очень большой угловой скорости вала (центрифуги, шпиндели шлифовальные и др.).
Виды разрушения вкладышей
Работа подшипников скольжения сопровождается абразивным изнашиванием вкладышей и цапф, заеданием и усталостным выкашиванием.
Абразивное изнашивание возникает вследствие попаданий со смазочным материалом абразивных частиц и неизбежной граничной смазки при пуске и останове.
Заедание возникает при перегреве подшипника, так как вследствие трения вкладыш и цапфа нагреваются. При установившемся режиме работы температура подшипника не должна превышать допускаемого значения для данного материала вкладыша и сорта масла. С повышением температуры понижается вязкость масла; масляная пленка местами разрывается, образуется металлический контакт с температурными пиками. Происходит заедание цапфы в подшипнике.
Усталостное выкашивание поверхности вкладышей происходит редко и встречается при пульсирующих нагрузках (в пошневых двигателях и т. п.).
Содержание лекции
Общие сведения
Достоинства подшипников качения
Недостатки подшипников качения
Классификация и маркировка подшипников качения
Основные типы подшипников качения
Материалы, применяемые для изготовления подшипников качения
Виды разрушения подшипников качения и критерии работоспособности
Расчет (подбор) подшипников качения на долговечность
Алгоритм расчета подшипников качения
Общие сведения
Подшипники качения представляют собой готовый узел рис.3.2.5, основным элементом которого являются тела качения — шарики или ролики 3, установленные между кольцами 1 к 2 и удерживаемые на определенном расстоянии друг от друга обоймой, называемой сепаратором 4. В процессе работы тела качения катятся по дорожкам качения колец, одно из которых в большинстве случаев неподвижно. Распределение нагрузки между несущими телами качения неравномерно и зависит от величины радиального зазора в подшипнике и от точности геометрической формы его деталей.
Рисунок 3.2.5 Подшипник качения
Подшипники качения широко распространены во всех отраслях машиностроения. Они стандартизованы и изготовляются в массовом производстве на ряде крупных специализированных заводов.
Рис. 23 Примеры сортовых и периодических профилей
Для изготовления машиностроительных профилей применяют прокатку, прессование, волочение. Поэтому кроме группирования по приведенным геометрическим признакам профили разделяют и по способу их изготовления.
Рис. 26 Схема прокатки шаров в стане поперечно-винтовой прокатки
Виды поковок
Поковкой называют заготовку детали, полученную обработкой металлов давлением. Огромное разнообразие машиностроительных деталей и соответственно такое же разнообразие форм и размеров поковок обусловливает существование различных способов изготовления поковок.
Поковки могут быть сгруппированы по признакам, определяющим технологию их изготовления. Такими признаками являются масса, конфигурация, марка сплава и тип производства.
Изготовление поковок может осуществляться по схемам свободного пластического течения между поверхностями инструмента или затекания металла в полость штампа. Для заполнения полости штампа необходимо давление, значительно превышающее давление при свободном пластическом течении металла. Вследствие этого поковки большой массы затруднительно изготовлять штамповкой. Для тяжелых поковок единственно возможным способом изготовления является ковка — вид горячей обработки металлов давлением, при котором деформирование производят последовательно на отдельных участках заготовки. Металл свободно течет в стороны, не ограниченные рабочими поверхностями инструмента, в качестве которого применяют плоские или фигурные бойки, а также различный подкладной инструмент. Таким образом, при ковке используют универсальный (годный для изготовления различных поковок) инструмент, в то время как для штамповки требуется специальный инструмент — штамп, изготовление которого при небольшой партии одинаковых поковок экономически невыгодно. Поэтому в единичном и мелкосерийном производствах ковка обычно экономически более целесообразна. Чем больше партия одинаковых поковок, тем более специализированным может быть технологический процесс их изготовления, так как применение более сложного, а значит более дорогого, инструмента и специального оборудования экономически оправдано.
Рис. 29 Виды машиностроительных поковок
Упрощенно поковки можно разделить на такие группы:
осесимметричные типа дисков и колес (рис. 29, 1, а); втулок и колец (рис. 29, 1, б); осесимметричные типа стаканов и втулок, размер которых вдоль оси больше поперечных (рис. 29, 2); осесимметричные типа валов и осей (рис. 29, 3), длина которых вдоль оси больше поперечных размеров; неосесимметричные типа рычагов, вилок, крюков (рис. 29, 4} с меньшим или большим соотношением габаритных размеров; к этой многочисленной группе относятся поковки гаечных ключей, шатунов, звеньев гусениц тракторов, лопаток турбин, крюков грузоподъемных механизмов, коленчатых валов и др.
Кроме такого разделения поковок по типу деталей при технологических расчетах по конфигурации поковки делят на группы сложности. Критерием сложности поковки может быть отношение объемов поковки и описанной вокруг нее простой геометрической фигуры – призмы или цилиндра.
Ковка
Процесс ковки состоит из чередования в определенной последовательности основных и вспомогательных операций. Каждая операция определяется характером деформирования и применяемым инструментом.
К основным операциям ковки относятся осадка, протяжка, прошивка, отрубка, гибка.
Осадка - операция уменьшения высоты заготовки при увеличении площади ее поперечного сечения (см. рис. 30, а). Осаживают заготовки между бойками или подкладными плитами.
Разновидностью осадки является высадка, при которой металл осаживают лишь на части длины заготовки.
Протяжка - операция удлинения заготовки или ее части за счет уменьшения площади поперечного сечения (рис. 30, а).
Рис. 30 Схемы протяжки и ее разновидностей
Протяжку производят последовательными ударами или нажатиями на отдельные участки заготовки, примыкающие один к другому, с подачей заготовки вдоль оси протяжки и поворотами ее на 90° вокруг этой оси. При слишком малой подаче могут получиться зажимы (рис. 30, б).
Прошивка - операция получения полостей в заготовке за счет вытеснения металла (рис. 31, а). Прошивкой можно получить сквозное отверстие или углубление (глухая прошивка).
Отрубка - операция отделения части заготовки по незамкнутому контуру путем внедрения в заготовку деформирующего инструмента - топора (рис. 31, г).
Гибка - операция придания заготовке изогнутой формы по заданному контуру (рис. 31,е). Этой операцией получают угольники, скобы, крючки, кронштейны и т. п.
Рис. 31 Схемы операции ковки: а— двусторонняя прошивка; б— сквозная прошивка; в— прошивни; г— отрубка; д— топоры; е— гибка ж— штамповка в подкладных штампах
Оборудование для ковки выбирают в зависимости от режима ковки данного металла или сплава, массы поковки и ее конфигурации. Необходимую мощность оборудования обычно определяют по приближенным формулам или справочным таблицам.
Ковку выполняют на ковочных молотах и ковочных гидравлических прессах.
Молоты — машины динамического, ударного действия. Продолжительность деформации на них составляет тысячные доли секунды. Металл деформируется за счет энергии, накопленной подвижными (падающими) частями молота к моменту их соударения с заготовкой. Поэтому при выборе молотов руководствуются массой их падающих частей. -
Гидравлические прессы — машины статического действия; продолжительность деформации на них может составлять от единиц до десятков секунд. Металл деформируется приложением силы, создаваемой с помощью жидкости (водной эмульсии или минерального масла), подаваемой в рабочий цилиндр пресса.
Технологические требования к деталям, получаемым из кованых поковок, сводятся главным образом к тому, что поковки должны быть наиболее простыми, очерченными цилиндрическими поверхностями и плоскостями (рис. 32, 1-4). В поковках следует избегать конических (рис. 32, 5) и клиновых (рис. 3.22, 6) форм. Необходимо учитывать трудности выполнения ковкой участков пересечений цилиндрических поверхностей между собой (рис. 32, 7) и с призматическими поверхностями (рис. 32, 8). В поковках следует избегать ребристых сечений, бобышек, выступов и т. п., учитывая, что эти элементы в большинстве случаев изготовить ковкой невозможно. В местах сложной конфигурации приходится прибегать к напускам в целях упрощения конфигурации поковки, что вызывает удорожание детали. Кроме того, следует стремиться, чтобы конфигурация детали позволяла получать при ковке наиболее благоприятное расположение волокон.
61. (2)Остановимся подробнее на первой части доклада - термодинамике процесса резания.
Закон сохранения энергии в процессе резания выражается, как известно, в превращении работы резания Ap в тепловую Q и скрытую (внутреннюю) энергию деформации деформируемых объемов стружки -
стр, поверхностных слоев детали -
дет и рабочих поверхностей инструмента -
инс т.е.
Так как долевой вклад в общие энергозатраты незначителен - всего 0,5..3,0%, она в исследованиях, как правило, не учитывалась. Это обстоятельство, видимо, отвлекло внимание ученых от целесообразности изучения термодинамики процесса резания, которая до последнего времени оставалась не раскрытой [1]. Тем не менее именно эта часть энергии - , вносящая изменения в энергию межатомных связей деформируемого материала, ответственна за изменение свойств контактных слоев стружки, детали и инструмента, соотношение твердостей которых, как известно, и определяет стойкость инструмента.
Действительно, действие всех параметров нагружения и сопутствующих процессов на интенсивность износа инструмента проявляется, в конечном итоге, через изменение (трансформацию) свойств взаимодействующих поверхностей инструмента, стружки и детали. Степень этих изменений в соответствии с принципами термодинамики определяется уровнем приращения их внутренней энергии за счет поглощения (или выделения) части энергии, развиваемой процессом в целом. Трансформация свойств деформируемых поверхностей - явление присущее всем контактным процессам, оно имеет место при всех условиях резания и сопутствует в той или иной форме всем видам износа, вследствие чего представляет наиболее широкие возможности для управления этими процессами. Таким образом, проблема повышения стойкости инструментов, связанная в общем случае с разработкой как оригинальных методов, так и с усилением эффективности традиционных, должна основываться на следствиях, вытекающих из термодинамики процесса резания, т.е. технологические меры, направленные на повышение стойкости, должны обеспечивать реализацию в непосредственных условиях резания одну из следующих задач:
1. Упрочнение рабочих поверхностей инструмента, т.е. увеличение их внутренней энергии за счет поглощения части подведенной внешней энергии;
2. Разупрочнение контактных поверхностей срезаемого слоя, т.е. выделение накапливаемой ими в процессе деформации (или предыдущих операций) внутренней энергии;
3. Направленную трансформацию свойств взаимодействующих поверхностей за счет перераспределения составляющих энергобаланса и, как следствие, .
Вторая и третья задачи принципиально известны. Прямыми методами, направленно решающими эти задачи, является резание с искусственным нагревом и применением смазочно-охлаждающих жидкостей: в первом случае за счет теплонагрузки зоны резания, во втором, наоборот,- теплоразгрузки, т.е. путем воздействия на требуемые составляющие баланса. Однако отсутствие экспериментальных данных по влиянию искусственного нагрева и СОЖ на теплоэнергобаланс процесса резания затрудняет реализацию указанных методов в оптимальном режиме.
62. Рассмотренные характеристики поверхностного слоя - шероховатость поверхности, структура и наклеп слоя, остаточные напряжения оказывают существенное влияние на такие важные эксплуатационные свойства деталей машин, как износостойкость, статическую, длительную и усталостную прочность, коррозионную стойкость, прочность соединений с натягом.Шероховатость и волнистость поверхности, структура, фазовый и химические составы поверхностного слоя по-разному влияют на эксплуатационные свойства деталей.
Отжиг II рода
Отжиг II рода заключается в нагреве стали до температур выше точек Ас1 или Ас3, выдержке и как правило, последующем медленном охлаждении. В процессе нагрева и охлаждения в этом случае протекают фазовые превращения (g «a), определяющие структуру и свойства стали.
Различают следующие виды отжига: полный, изотермический и неполный.
Полный отжиг заключается в нагреве доэвтектоидной стали на 30 - 50°С выше температуры, соответствующей точке Ас3, выдержке при этой температуре для полного прогрева и завершения фазовых превращений в объеме металла и последующем медленном охлаждении. При нагреве до температуры выше точки А3на 30-500С образуется аустенит, характеризующий мелким зерном, поэтому при охлаждении возникает мелкозернистая структура, обеспечивающая высокую вязкость и пластичность, и возможность достижения высоких свойства после окончательной термической обработки.Чрезмерное повышение температуры нагрева выше точки А3 вызывает рост аустенита, что ухудшает свойство стали.Медленное охлаждение должно обеспечить распад аустенита при малых степенях переохлаждения, что бы избежать образования излишне дисперсной ферритно-карбидной структуры и свойственное ей более высокой твердости. Чем больше устойчивость аустенита в области температур перлитного превращения, тем медленнее должно быть охлаждение.Полному отжигу подвергают сортовый прокат из стали с 0,3-0,4 % С, поковки, фасонные отливки. Изотермический отжиг состоит обычно в нагреве легированной стали, как и для полного отжига, и в сравнительно быстром охлаждении до температуры, лежащей ниже точки А1 (обычно 660 - 6800С) При этой температуре назначают изотермическую выдержку 3 - 6 ч., необходимую для полного распада аустенита, после чего следует охлаждение на воздухе. Преимущество изотермического отжига
Пружинную (канатную) проволоку из стали, содержащей 0,65-0,9%С, перед холодным волочением подвергают изотермической обработке - патентированию. Для потентирования проволоку подвергают высокотемпературной аустенизации для получения однородного аустенита, а затем пропускают через расплавленную соль температурой 450-5500С. В результате изотерм
|
|
Опора деревянной одностоечной и способы укрепление угловых опор: Опоры ВЛ - конструкции, предназначенные для поддерживания проводов на необходимой высоте над землей, водой...
История развития пистолетов-пулеметов: Предпосылкой для возникновения пистолетов-пулеметов послужила давняя тенденция тяготения винтовок...
Эмиссия газов от очистных сооружений канализации: В последние годы внимание мирового сообщества сосредоточено на экологических проблемах...
Историки об Елизавете Петровне: Елизавета попала между двумя встречными культурными течениями, воспитывалась среди новых европейских веяний и преданий...
© cyberpedia.su 2017-2024 - Не является автором материалов. Исключительное право сохранено за автором текста.
Если вы не хотите, чтобы данный материал был у нас на сайте, перейдите по ссылке: Нарушение авторских прав. Мы поможем в написании вашей работы!