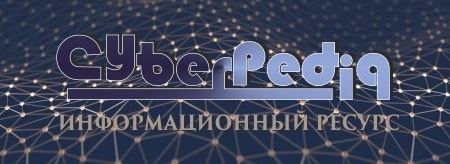
Таксономические единицы (категории) растений: Каждая система классификации состоит из определённых соподчиненных друг другу...
Биохимия спиртового брожения: Основу технологии получения пива составляет спиртовое брожение, - при котором сахар превращается...
Топ:
Отражение на счетах бухгалтерского учета процесса приобретения: Процесс заготовления представляет систему экономических событий, включающих приобретение организацией у поставщиков сырья...
Теоретическая значимость работы: Описание теоретической значимости (ценности) результатов исследования должно присутствовать во введении...
Интересное:
Средства для ингаляционного наркоза: Наркоз наступает в результате вдыхания (ингаляции) средств, которое осуществляют или с помощью маски...
Влияние предпринимательской среды на эффективное функционирование предприятия: Предпринимательская среда – это совокупность внешних и внутренних факторов, оказывающих влияние на функционирование фирмы...
Лечение прогрессирующих форм рака: Одним из наиболее важных достижений экспериментальной химиотерапии опухолей, начатой в 60-х и реализованной в 70-х годах, является...
Дисциплины:
![]() |
![]() |
5.00
из
|
Заказать работу |
|
|
Литьё в оболочковые формы — способ получения фасонных отливок из металлических сплавов в формах, состоящих из смеси песчаных зёрен (обычно кварцевых) и синтетического порошка (обычно фенолоформальдегидной смолы и пульвер-бакелита). Предпочтительно применение плакированных песчаных зёрен (покрытых слоем синтетической смолы).
Оболочковую форму получают одним из двух методов. Смесь насыпают на металлическую модель, нагретую до 300 °C, выдерживают в течение нескольких десятков секунд до образования тонкого упрочнённого слоя, избыток смеси удаляют. При использовании плакированной смеси её вдувают в зазор между нагретой моделью и наружной контурной плитой. В обоих случаях необходимо доупрочнение оболочки в печи (при температуре до 600-700 °C) на модели. Полученные оболочковые полуформы скрепляют, и в них заливают жидкий сплав. Во избежание деформации форм под действием заливаемого сплава перед заливкой их помещают в металлический кожух, а пространство между его стенками и формой заполняют металлической дробью, наличие которой воздействует также на температурный режим охлаждающейся отливки.
Этим способом изготавливают различные отливки массой до 25 кг. Преимуществами способа являются значительные повышение производительности по сравнению с изготовлением отливок литьём в песчаные формы, управление тепловым режимом охлаждения отливки и возможность механизировать процесс.
43. Лаки и эмали, бумаги и картоны. Виды, свойства, применение.
Билет 18
-- Центробежное литье. Суть, технология, применение.
Центробежное литье — это способ получения отливок в металлических формах. При центробежном литье расплавленный металл, подвергаетсяь действию центробежных сил, отбрасывается к стенкам формы и затвердевает. Таким образом получается отливка. Этот способ литья широко используется в промышленности, особенно для получения пустотелых отливок (со свободной поверхностью). Центробежный метод литья (центробежное литье) используется при получении отливок, имеющих форму тел вращения.
|
Подобные отливки отливаются из чугуна, стали, бронзы и алюминия. При этом расплав заливают в металлическую форму, вращающуюся со скоростью 3000 об/мин. Под действием центробежной силы расплав распределяется по внутренней поверхности формы и, кристаллизуясь, образует отливку. Центробежным способом модно получить двухслойные заготовки, что достигается поочередной заливкой в форму различных сплавов. Кристаллизация расплава в метллической форме под действием центробежной силы обеспечивает получение плотных отливок. При этом, как правило, в отливках не бывает газовых раковин и шлаковых включений. Особыми преимуществами центробежного литья является получение внутренних полостей без применения стержней и большая экономия сплава в виду отсутствия литниковой системы. Выход годных отливок повышается до 95%. В нашем производстве используют машины с горизонтальными осями вращения. Широким спросом пользуются отливки втулок, гильз и других заготовок, имеющих форму тела вращения, произведенные с помощью метода центробежного литья.
Преимущества технологии центробежного литья:
Технология центробежного литья обеспечивает целый ряд преимуществ, зачастую недостижимых при других способах, к примеру:
- Высокая износостойкость;
- Высокая плотность металла;
- Отсутствие раковин;
- Мелкое зерно;
- В продукции центробежного литья отсутствуют неметаллические включения и шлак.
Недостатки:
- Ограниченная номенклатура по конфигурации;
- Отливки имеют химически неоднородную поверхность;
- Значительная шероховатость;
- Внутренняя поверхность более шероховатая.
|
Технологические возможности:
- любые сплавы;
- масса до 45 тонн;
- толщина стенок от 3..250 мм;
- длина 6 метров;
- 13-16 квалитет для цветных металлов;
- 14-17 квалитет для черных металлов;
- Rz=320..40.
Применение
Центробежным литьем получают литые заготовки, имеющие форму тел вращения:
- втулки;
- венцы червячных колес;
- барабаны для бумагоделательных машин;
- роторы электродвигателей.
---Магнитные материалы. Кривые намагничивания. Основные характеристики магнитных материалов (остаточная индукция, коэрцитивная сила, магнитная проницаемость).
Магнитомягкие материалы используются в энергетике в качестве разнообразных магнитопроводов в трансформаторах, электрических машинах, электромагнитах и т.д.
Для уменьшения потерь на гистерезис выбирают материалы с пониженной коэрцитивной силой, а для уменьшения вихревых токов магнитопроводы собирают из отдельных пластин и используют металлы с повышенным удельным сопротивлением. Дело в том, что ЭДС самоиндукции, благодаря которой возникают вихревые токи, пропорциональна площади поперечного сечения контура. При рассечении площади nизолированными пластинами в каждой пластине наводится уменьшенная в n раз ЭДС. Мощность потерь при протекании вихревого тока пропорциональна квадрату напряжения (ЭДС) и обратно пропорциональна удельному сопротивлению. Поэтому уменьшение ЭДС в каждой из отдельных пластин и использование металлов с повышенным удельным сопротивлением приводит к уменьшению общих потерь.
Основой наиболее широко используемых в электротехнике магнитных материалов является низкоуглеродистая электротехническая сталь. Она выпускается в виде листов, толщиной от 0.2 мм до 4 мм, содержит не выше 0.04% углерода и не выше 0.6% других примесей. Максимальное значение магнитной проницаемости mmax ~ 4000, коэрцитивной силы Нс~ 65-100 А/м. Наблюдается интересная закономерность: чем чище железо и чем лучше оно отожжено - тем выше магнитная проницаемость и тем ниже коэрцитивная сила. Для особо чистого железа эти параметры составляют: более 1 миллиона и менее 1 А/м, соответственно.
Добавлением в состав кремния достигается повышение удельного сопротивления стали с 0.14 мкОм·м для нелегированной стали до 0.6 мкОм·м для высоколегированной стали. Это дает уменьшение потерь.
Электротехническую сталь маркируют следующим образом: первая цифра-структура (1-горячекатанная изотропная, 2-холоднокатанная изотропная, 3- холоднокатанная анизотропная с ребровой структурой), вторая цифра- содержание кремния (0-до 0.4%, 1 - до 0.8%. 2 - до 1.8%, 3-до 2.8%, 4 - до 3.8%, 4 - до 4.8%), третья цифра - тип нормируемых магнитных характеристик (0- удельные потери при В=1.7 Тл, f=50 Гц, 1- удельные потери при В=1.5 Тл, f=50 Гц, 2- удельные потери при В=1 Тл, f=400 Гц, 6- В при Н=0.4 А/м, 7- В в средних полях при Н=10 А/м). Четвертая цифра в старых справочниках означала номер материала. В современных справочниках четвертая и пятая цифры являются одним числом, означающим численную характеристику нормируемого параметра.
|
Если к железу добавить никель, то полученные материалы будут обладать повышенной магнитной проницаемостью (до 100000 у 79НМ, 79% никеля и небольшое количество марганца). Такие сплавы называются пермаллои, они используются для изготовления сердечников малогабаритнгых силовых и импульсных трансформаторов. Практически такие же результаты по магнитной проницаемости можно получить, добавляя к железу кремний (9.5%) и алюминий(5.6%). Такие сплавы называются альсиферами.
Добавки к железу и никелю молибдена, хрома, меди приводит к еще большему росту начальной магнитной проницаемости, более 100 тысяч. Такие материалы используются в миниатюрных магнитных устройствах.
Практически отсутствуют потери на вихревые токи в ферритах. Дело в том, что ферриты представляют собой оксидную керамику МеО+Fe2O3, которая является диэлектриком, либо полупроводником. Типичное удельное сопротивление феррита 103-104 Ом.м. Это на 9-10 порядков превышает сопротивление металлов. Ясно, что вихревые токи в таком материале не возникнут. Магнитная проницаемость у ферритов обычно ниже, чем у стали и не превышает нескольких сотен, хотя есть ферриты с проницаемостью до нескольких тысяч (20000НМ, 1000НМ). Применение в энергетике магнитомягких ферритов - высокочастотные трансформаторы, в ряде материалов потери малы вплоть до частот гигагерцового диапазона. Однако при этом и магнитная проницаемость уменьшается до десятков (9ВЧ, 50ВЧ3).
Большую роль играют ферриты с прямоугольной петлей гистерезиса (ППГ). Они используются в качестве логических элементов в ЗУ, в качестве термодатчиков. Основной параметр - коэффициент прямоугольности петли гистерезиса, представляющий собой отношение остаточной индукции к максимальной, измеренной при Н = 5 Нс. Желательно, чтобы этот коэффициент был ближе к 1.
Билет 19
|
|
Автоматическое растормаживание колес: Тормозные устройства колес предназначены для уменьшения длины пробега и улучшения маневрирования ВС при...
Историки об Елизавете Петровне: Елизавета попала между двумя встречными культурными течениями, воспитывалась среди новых европейских веяний и преданий...
Наброски и зарисовки растений, плодов, цветов: Освоить конструктивное построение структуры дерева через зарисовки отдельных деревьев, группы деревьев...
Особенности сооружения опор в сложных условиях: Сооружение ВЛ в районах с суровыми климатическими и тяжелыми геологическими условиями...
© cyberpedia.su 2017-2024 - Не является автором материалов. Исключительное право сохранено за автором текста.
Если вы не хотите, чтобы данный материал был у нас на сайте, перейдите по ссылке: Нарушение авторских прав. Мы поможем в написании вашей работы!