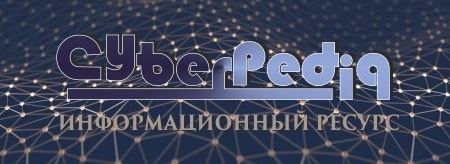
История развития хранилищ для нефти: Первые склады нефти появились в XVII веке. Они представляли собой землянные ямы-амбара глубиной 4…5 м...
Архитектура электронного правительства: Единая архитектура – это методологический подход при создании системы управления государства, который строится...
Топ:
История развития методов оптимизации: теорема Куна-Таккера, метод Лагранжа, роль выпуклости в оптимизации...
Особенности труда и отдыха в условиях низких температур: К работам при низких температурах на открытом воздухе и в не отапливаемых помещениях допускаются лица не моложе 18 лет, прошедшие...
Техника безопасности при работе на пароконвектомате: К обслуживанию пароконвектомата допускаются лица, прошедшие технический минимум по эксплуатации оборудования...
Интересное:
Как мы говорим и как мы слушаем: общение можно сравнить с огромным зонтиком, под которым скрыто все...
Что нужно делать при лейкемии: Прежде всего, необходимо выяснить, не страдаете ли вы каким-либо душевным недугом...
Наиболее распространенные виды рака: Раковая опухоль — это самостоятельное новообразование, которое может возникнуть и от повышенного давления...
Дисциплины:
![]() |
![]() |
5.00
из
|
Заказать работу |
|
|
Измельчающие машины могут быть классифицированы по различным признакам: степени измельчения материала, которую можно достичь с помощью машин (для среднего и мелкого измельчения) и мельниц (для тонкого и коллоидного измельчения); способу измельчения — машины изрезывающие, истирающие, раздавливающие, ударные, ударно-истирающие и др. В дальнейшем изложении будем придерживаться обеих классификаций, дополняющих друг друга.
Машины для среднего и мелкого измельчения
Изрезывающие машины. Применяются для измельчения высушенного растительного лекарственного сырья, которое изрезывается до размера частиц 2—8 мм (для получения сборов или производства экстракционных препаратов) с помощью траво- и корнерезок. Рабочим инструментом изрезывающих машин является нож или система ножей, совершающих возвратно-поступательное или вращательное движение. В некоторых случаях машина имеет две системы ножей. Один нож в этих системах двигается, другие смонтированы неподвижно.
Рисунок 1.
Траво- и корнерезки. В зависимости от строения ножей различают траворезки дисковые и барабанные. В дисковых траворезках ножи имеют изогнутое лезвие и насажены на спицы рабочего колеса, в барабанных ножи помешаются на боковой поверхности барабана, вращающегося вокруг своей оси.
Для измельчения плотных частей растений (корни, корневища, коры) применяются корнерезки. Отличительной их особенностью является наличие гильотинных ножей.
Раздавливающие машины. Валковая дробилка состоит из двух параллельных цилиндрических валков, которые, вращаясь навстречу друг другу, измельчают материал главным образом путем раздавливания (рис2). Валки размещены на подшипниках в корпусе, причем валок (1) вращается в неподвижно установленных, а валок (2) — в скользящих подшипниках, которые удерживаются в заданном положении (в зависимости от требуемой ширины зазора) с помощью пружины (3). При попадании в дробилку куска материала чрезмерной твердости пружины ее сжимаются, подвижный валок отходит от неподвижного и кусок выпадает из дробилки, при этом устраняется возможность ее поломки.
|
Рисунок 2.
В промышленности используются валковые дробилки, отличающиеся по числу, форме и скорости вращения валков. Приводной механизм состоит из двухпеременных передач от отдельного двигателя на шкив каждого валка, окружная скорость которых составляет 2—4,5 м/с. Наибольший размер кусков измельчаемого в валковой дробилке материала зависит от диаметра валков и зазора между ними. Для того чтобы куски измельчаемого материала вследствие трения втягивались между гладкими валками, их диаметр должен быть приблизительно в 20 раз больше диаметра максимального куска измельчаемого материала. Поэтому гладкие валки применяются только для среднего и мелкого измельчения.
Ударно-центробежные мельницы. Дисмембратор и дезинтегратор. Рабочими частями дисмембрато-р а (рис.3) являются диски: вращающийся — со скоростью до 3000 об/мин (1) и неподвижный (3). Роль последнего выполняет внутренняя стенка корпуса. На внутренней поверхности дисков укреплены по концентрическим окружностям пальцы. При этом диски поставлены один против другого так, что пальцы (2) вращающегося диска входят в свободное пространство между пальцами (4) неподвижного диска. Число пальцев в концентрических окружностях увеличивается по направлению от центра к периферии. Материал, подлежащий измельчению, через загрузочный бункер (5) поступает в центр дисмембратора, в зону между вращающимися и неподвижными пальцами, где и происходит его измельчение. Под действием центробежной силы частицы перемещаются от центра к периферии рабочего органа дисмембратора, многократно ударяются о пальцы, поверхность дисков, испытывают взаимные удары и разрушаются. Измельченные частицы отбрасываются в улитку (6), откуда, ударяясь о корпус дисмембратора (7) и вращающийся диск, падают вниз и выводятся из машины. Для предотвращения попадания в зоны измельчения механических предметов исходное сырье проходит предварительно через магнитный сепаратор (8), который устанавливается в нижней части бункера.
|
Барабанные мельницы. Материал измельчается внутри вращающегося корпуса (барабана) под воздействием мелющих тел. В зависимости от вида мелющих тел различают шаровые и стержневые мельницы. В зависимости от формы барабана и отношения его длины / к диаметру d различают короткие (l/d = — 1,5—2,0), трубные (//d=3,0—6,0), цилиндро-кони-ческие мельницы (барабан имеет форму двух усеченных конусов, широкие основания которых соединены цилиндрической частью) и др.
Шаровые мельницы. В химико-фармацевтической промышленности для тонкого измельчения наиболее широко применяются шаровые мельницы периодического действия. Они представляют собой (рис. 7.7) пустотелый вращающийся барабан, в который через люк с плотно прижатой к барабану специальной скобой-крышкой загружают измельчаемый материал и мелющие тела — стальные шары диаметром от 25 до 150 мм (приблизительно на 40—45% объема барабана).
Струйные мельницы. Измельчение материала происходит в струе энергоносителя (воздух, инертный газ, перегретый пар), подаваемого в мельницу со скоростью, достигающей нескольких сотен метров в секунду.
В струйной мельнице с плоской помольной камерой (рис. 7.10) энергоноситель из распределительного коллектора (2), через сопла (3) отдельными струями поступает в помольно-разделительную камеру. Оси сопел расположены под некоторым углом относительно соответствующих радиусов камеры, вследствие чего струи газа внутри камеры пересекаются. Материал на измельчение подается инжектором (струйный компрессор) через штуцер (1), увлекается струями газа, получает усконение и измельчается под действием многократных соударений и частично истиранием частиц в точках пересечения струй. Так как струи энергоносителя входят в зону измельчения под некоторым углом, вся масса пылегазовои смеси приобретает вращательное движение в направлении струй. В результате такого движения частицы оказываются в поле центробежных сил и разделяются на фракции. При этом более крупные сосредоточиваются в периферийной части зоны измельчения, а мелкие оттесняются к центру. Измельчившись до определенных размеров (1—6 мкм), частицы вместе с нисходящим газовым потоком, непрерывно вращаясь, вытекают из зоны измельчения в корпус циклона-осадителя (4), осаждаются на его внутренней поверхности и удаляются в приемник (5). Наиболее мелкие частицы, содержание которых 5—10 % увлекаются восходящим потоком отработанного воздуха, уносятся через штуцер (6) и улавливаются в дополнительных циклонах или матерчатых фильтрах.
|
|
|
Индивидуальные очистные сооружения: К классу индивидуальных очистных сооружений относят сооружения, пропускная способность которых...
Состав сооружений: решетки и песколовки: Решетки – это первое устройство в схеме очистных сооружений. Они представляют...
Поперечные профили набережных и береговой полосы: На городских территориях берегоукрепление проектируют с учетом технических и экономических требований, но особое значение придают эстетическим...
Наброски и зарисовки растений, плодов, цветов: Освоить конструктивное построение структуры дерева через зарисовки отдельных деревьев, группы деревьев...
© cyberpedia.su 2017-2024 - Не является автором материалов. Исключительное право сохранено за автором текста.
Если вы не хотите, чтобы данный материал был у нас на сайте, перейдите по ссылке: Нарушение авторских прав. Мы поможем в написании вашей работы!