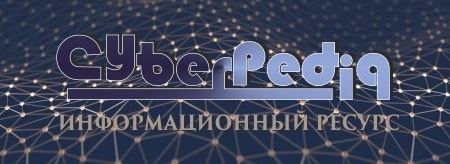
Своеобразие русской архитектуры: Основной материал – дерево – быстрота постройки, но недолговечность и необходимость деления...
Биохимия спиртового брожения: Основу технологии получения пива составляет спиртовое брожение, - при котором сахар превращается...
Топ:
Генеалогическое древо Султанов Османской империи: Османские правители, вначале, будучи еще бейлербеями Анатолии, женились на дочерях византийских императоров...
Установка замедленного коксования: Чем выше температура и ниже давление, тем место разрыва углеродной цепи всё больше смещается к её концу и значительно возрастает...
Определение места расположения распределительного центра: Фирма реализует продукцию на рынках сбыта и имеет постоянных поставщиков в разных регионах. Увеличение объема продаж...
Интересное:
Наиболее распространенные виды рака: Раковая опухоль — это самостоятельное новообразование, которое может возникнуть и от повышенного давления...
Что нужно делать при лейкемии: Прежде всего, необходимо выяснить, не страдаете ли вы каким-либо душевным недугом...
Искусственное повышение поверхности территории: Варианты искусственного повышения поверхности территории необходимо выбирать на основе анализа следующих характеристик защищаемой территории...
Дисциплины:
![]() |
![]() |
5.00
из
|
Заказать работу |
|
|
Высокое качество продукции при экономном расходовании материалов обеспечивается на всех этапах производства, начиная с разработки конструкции, изготовления лекал, подготовки и раскроя тканей. Начальные этапы производства выполняются в подготовительном, экспериментальном и раскройном цехах предприятия. Подготовительное производство включает в себя следующие работы: прием, распаковку, качественную и количественную проверку материалов, хранение и накапливание материалов для раскроя, расчет ткани для безостаткового ее использования, изготовление зарисовок, комплектование материалов (основного, подкладочного, приклада) в соответствии с расчетом и подачу их в раскройный цех. В связи с этим в подготовительном цехе выделяют распаковочное, разбраковочно-промерочное и обмеловочное отделения. Отделение обмеловки может быть расположено в экспериментальном цехе при применении свето- или фотокопий раскладок лекал. В распаковочное отделение поступают разнообразные материалы, необходимые для изготовления планового ассортимента изделий предприятия. Количество поступающих материалов проверяют по сопровождающим их документам. Распакованный материал укладывают на стеллажи или поддоны ярлыками наружу. В этом отделении хранят материалы с соблюдением мер, предупреждающих их порчу. Ткани предохраняют от атмосферных осадков, действия солнечных лучей, сырости, низкой температуры, запыления, насекомых. Весь поступающий на предприятие материал (ткань) подвергают контрольной и производственной разбраковке. Цель контролькой разбраковки - проверка правильности сопроводительного документа (сорта куска, его длины и ширины). Производственная разбраковка нужна для полного использования куска ткани по длине и ширине. Текстильные дефекты не должны попадать при раскрое на детали изделия. Обе разбраковки выполняют одновременно на промерочно-разбраковочной машине или на специально оборудованном столе. Проверка материалов на промерочно-разбраковочной машине состоит в следующем. На машине развертывают сложенную вдвое ткань, заправляют ее между направляющими валиками, пропускают через экран машины и наматывают на стержень в рулон. Движущуюся по экрану хорошо освещенную ткань проверяет контролер, отмечая текстильные дефекты. На некоторых машинах одновременно измеряется длина куска с помощью электрического щупа. При разбраковке ткани выявляют пятна, зауженные места, разноцвет краев ткани по сравнению с серединой, разноцвет по длине куска и другие дефекты, влияющие на внешний вид изделия. У мест расположения дефектов ткани делают мелом пометку, а на кромку навешивают цветную нитку («сигнал»). Каждый дефект оценивается определенным количеством баллов в зависимости от его величины и характера. Путем суммирования баллов по всем дефектам куска контролируют правильность установленного сорта. Для экономного и полного использования каждого куска ткани необходимо знать его длину и ширину. Для этого в промышленности применяют промерочно-разбраковочные машины, на которых одновременно разбраковывают и измеряют ткань по длине и ширине. Если такого оборудования нет, промер кусков ткани осуществляют на трехметровом столе с механическим устройством для перемещения и наматывания ткани в рулон. Ширину куска измеряют через каждые три метра. За основную ширину берут наиболее часто встречающуюся, а сильно зауженные или расширенные места куска отмечают и используют при раскрое отдельно. Одновременно отмечают расположение текстильных дефектов по длине куска. Все данные о куске ткани записывают в специальном бланке, называемом паспортом куска. В подготовительном цехе разбракованную ткань укладывают на стеллажи по артикулам и ширинам торцевыми сторонами наружу. Хранение ткани осуществляют различными способами. При этом необходимо наиболее полно использовать площадь и объем склада и так располагать рулоны ткани, чтобы была возможность за минимально короткий промежуток времени механизированным способом уложить их и выбрать нужный для раскроя рулон. Склады оборудуются различными стеллажами для поштучного хранения рулонов. ![]()
|
Раскройное производство
|
|
|
|
|
Основной задачей раскройного цеха является раскраивание материалов на детали и комплектование кроя из основной ткани, подкладки и приклада для обеспечения работой швейных цехов. На раскройное производство приходится значительная доля затрат от общих затрат времени на изготовление изделия. Отсюда возникает сложная задача - механизация трудоемких процессов на этом участке. Проводимые исследования и внедрение новых видов оборудования и организации производства позволяют все больше снижать трудовые затраты на единицу продукции. Раскройное производство является одним из важнейших участков, предопределяющих качество будущего готового изделия и осуществляющих экономное расходование материалов. Вследствие этого механизация технологических операций раскройного производства позволит получить устойчивое высокое качество продукции и снизить потери ткани. На предприятии раскройное производство выделяют в самостоятельный цех, в котором выполняют следующие работы (при условии, что зарисовки изготовляют в подготовительном цехе): приемку материалов из цеха подготовки; приемку зарисовок, трафаретов и контрольных лекал из экспериментального цеха; предварительное разрезание кусков основной ткани на полотна заданной длины (мерные полотна) в соответствии с расчетом; настилание основного материала, подкладки и приклада по предварительному расчету, измерение остатков материала; контроль качества настила, подмелку нечетких контуров деталей; учет результатов настилания; клеймение деталей на верхнем полотне настила; раскрой деталей изделия; выполнение зарисовок и раскрой полотен из материала с текстильными дефектами; сборку и комплектование пачек деталей кроя из основной ткани, подкладки и приклада; нумерацию деталей кроя; выписывание сопроводительного документа (маршрутного листа) на крой, печатание талонов, товарных ярлыков и контрольных лент; отправление в кладовую готовых пачек кроя для хранения перед подачей их в швейные цехи. Указанный перечень организационных и технических операций является примерным. На разных швейных предприятиях в зависимости от местных условий (имеющегося оборудования, размещения производств и др.) могут быть изменены некоторые виды работ. Сущность рационального раскроя тканей Приемку материалов из подготовительного цеха выполняют по карте расчета. Одновременно принимают зарисовки. Карта расчета материала является результатом предварительного расчета кусков ткани до полного их использования на запланированные комбинации размероростов моделей. Предварительный расчет материалов выполняют по суточному заданию с указанием количества изделий по каждой модели и размероросту. Целью предварительного расчета является выбор варианта полного использования каждого куска ткани по длине. Раскрой материалов на швейных предприятиях выполняют настилами. Настилом называют несколько полотен материала определенной длины, уложенных одно на другое слоями (в пачку), предназначенных для одновременного раскраивания. Кусок ткани не всегда удается полностью использовать, так как чаще всего его длина не бывает кратной длине полотна настила. Сочетания в раскладке изделий различных размеров, ростов (длин) и полнотных групп дают разные длины зарисовок, что помогает подобрать вариант использования кусков ткани различной длины. Остаток ткани, имеющий длину меньше нормы расхода ткани на изделие самого малого размера и роста, предусмотренное программой предприятия, называется нерациональным. Чтобы не было нерациональных остатков, куски ткани рассчитывают на несколько разных по длине настилов. В этом случае ткань из одного куска настилают по нескольку полотен на каждый настил. При расчете ткани к длине рамки зарисовки прибавляют припуски на потери по длине при настилании полотен. Величина этих припусков зависит от вида волокна, ширины ткани, длины настила и не должна превышать для костюмных тканей 2 см на одно полотно. Так образуется норма расхода ткани на полотно для настила. Благодаря предварительным расчетам на предприятиях стало возможным применение рационального способа раскроя ткани, при котором остаются маломерные остатки (лоскут), не превышающие установленных нормативов: для шерстяных костюмных тканей - 0,4%, для шелковых подкладочных тканей - 0,7, для хлопчатобумажных подкладочных - 0,3, для искусственной кожи - 0,9% площади раскраиваемого материала. Наиболее распространен механизированный способ расчета кусков ткани. Он осуществляется на электронно-счетных машинах. Сведения о метраже куска и длинах настилов, на которые надо его раскроить, вводятся в запоминающее устройство машины. Результаты расчета машина выдает в виде ответа, сколько полотен и какой длины можно раскроить без остатка или с минимальным (до 0,15 м) остатком из заданного куска ткани. При расчете кусков учитывают способ расположения полотен. Полотна в настиле могут располагаться лицевыми сторонами вниз («лицом вниз») или попарно лицевыми сторонами одно к другому («лицом к лицу»). При раскрое костюмов и брюк способом настилания «лицом к лицу» количество полотен в настиле должно быть четным. Расчет кусков ткани для раскроя осложняется наличием в ткани текстильных дефектов. Дефекты ткани, недопустимые в готовых швейных изделиях, принимают при расчете кусков за условные разрезы ткани и стремятся разместить в месте отреза полотна. Если это не удается сделать, куски ткани с условными разрезами рассчитывают так, чтобы полотна ткани с дефектами были раскроены отдельно. Эти полотна ткани в записи расчета отмечают обычно красным карандашом, а сами полотна называют дефектными. Дефектные полотна поступают на индивидуальные раскладки и зарисовки, при выполнении которых местные дефекты стремятся оставлять в межлекальных участках зарисовки. Исходными данными для выполнения расчета кусков ткани являются данные, записанные в паспортах кусков, и суточное задание на раскрой. Куски ткани в один расчет подбирают по ширине, артикулу, рисунку и цвету. Для увеличения высоты настилов на швейных предприятиях допускается комплектовать в один настил ткани разных цветов, однако гладкие и рисунчатые полотна никогда не помещают в одном настиле. Это объясняется тем, что раскладку для рисунчатых тканей выполняют с припусками на подбор рисунка, а на гладких тканях этих припусков не делают. Пример расчета кусков основной ткани приведен в табл. 5.
![]() ![]() ![]() ![]()
![]() Семя – орган полового размножения и расселения растений: наружи у семян имеется плотный покров – кожура... ![]() Типы сооружений для обработки осадков: Септиками называются сооружения, в которых одновременно происходят осветление сточной жидкости... ![]() Адаптации растений и животных к жизни в горах: Большое значение для жизни организмов в горах имеют степень расчленения, крутизна и экспозиционные различия склонов... ![]() Эмиссия газов от очистных сооружений канализации: В последние годы внимание мирового сообщества сосредоточено на экологических проблемах... © cyberpedia.su 2017-2024 - Не является автором материалов. Исключительное право сохранено за автором текста. |