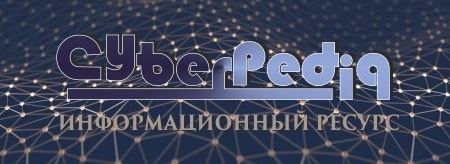
История развития хранилищ для нефти: Первые склады нефти появились в XVII веке. Они представляли собой землянные ямы-амбара глубиной 4…5 м...
Археология об основании Рима: Новые раскопки проясняют и такой острый дискуссионный вопрос, как дата самого возникновения Рима...
Топ:
Характеристика АТП и сварочно-жестяницкого участка: Транспорт в настоящее время является одной из важнейших отраслей народного хозяйства...
Теоретическая значимость работы: Описание теоретической значимости (ценности) результатов исследования должно присутствовать во введении...
Интересное:
Лечение прогрессирующих форм рака: Одним из наиболее важных достижений экспериментальной химиотерапии опухолей, начатой в 60-х и реализованной в 70-х годах, является...
Национальное богатство страны и его составляющие: для оценки элементов национального богатства используются...
Инженерная защита территорий, зданий и сооружений от опасных геологических процессов: Изучение оползневых явлений, оценка устойчивости склонов и проектирование противооползневых сооружений — актуальнейшие задачи, стоящие перед отечественными...
Дисциплины:
![]() |
![]() |
5.00
из
|
Заказать работу |
|
|
В топках промышленных парогенераторов и водогрейных котлов в основном сжигаются вязкие мазуты марок 40, 100 и реже 200. Топочные мазуты этих марок делятся на малосернистые, сернистые и высокосернистые с содержанием серы соответственно не более 0,5; 2,0 и 3,5%. Для сжигания мазута необходима его предварительная подготовка: уменьшение вязкости и распыление, при котором обеспечивается испарение мазута. Распыление и распределение жидкого топлива в потоке окислителя (воздуха) производится в одном из элементов горелки, называемом форсункой.
В настоящее время имеются разнообразные конструкции форсунок для сжигания мазута. Из различных типов форсунок с пневматическим распыливанием мазута наибольшее распространение в свое время получили разработанные ЦКТИ горелки двух типов: низконапорные типа НГМГ (в настоящее время сняты с производства, но находятся в эксплуатации во многих котельных) и паромеханические типа ГМГ. Обе эти конструкции выполнены как комбинированные для сжигания газа и мазута. В последнее время для сжигания мазута начинают применяться камеры двухступенчатого сжигания. Для водогрейных котлов применяются ротационные горелки, разработанные ЦКТИ совместно с БЗЭМ, Калужским машиностроительным заводом и заводом «Ильмарине».
Для стационарных паровых котлов форсунки паромеханические выпускаются в соответствии с ОСТ 108.836.03—80, механические по ОСТ 108.836.01—80 и паровые по ОСТ 108.836.04—80.
Для сжигания вязкого мазута независимо от типа применяемых форсунок необходим его предварительный подогрев, от ко- < торого зависит качество распыливания мазута. Температура подогрева мазута выбирается с таким расчетом, чтобы вязкость мазута перед горелками обеспечивала необходимое качество распыливания. Для механических и паромеханических форсунок вязкость мазута рекомендуется поддерживать 2,5° -УВ (16,1 мм2/с), для пневматических — не более 6° УВ (44 мм2/с) и ротационных — не более 8°УВ (59 мм2/с). Для получения указанных значений вязкости мазута перед форсунками необходимо подогревать мазут марки 40 до 115 °С, а марки 100 — до 130 °Спри сжигании в топках с механическими и паромеханическими форсунками; в топках с пневматическими форсунками— соответственно до 90 и ПО °С; в топках с ротационными форсунками — до 80 и 95 °С.
|
На рис. 3-15 показана схема газомазутной горелки типа НГМГ с воздушным распиливанием мазута. В горелке НГМГ мазут поступает под давлением не более 30 кПа по мазутному стволу 4 и вытекает через мазутовыпускные отверстия 8. Распиливающий (первичный) воздух получает закрутку в завихрителе 9 и, выходя через пережимное кольцо 7, подхватывает и
распиливает струйки мазута, вытекающие через отверстия 8. Давление первичного воздуха составляет 2500—3000 Па при расходе 10—15 % общего количества воздуха, необходимого для горения. При эксплуатации форсунки необходимо следить за правильной установкой мазутного ствола. Многочисленные испытания показали, что излишнее смещение мазуто-выпускных отверстий относительно пережима в сторону топки приводит к удлинению факела, затягиванию процесса горения в камеру догорания и даже в газоходы котла. Излишнее смещение мазутовыпускных отверстий в противоположную сторону относительно пережима приводит к попаданию мазута на за-вихритель. Положение мазутовыпускных отверстий относительно пережима уточняется при наладке горелки. На рис. 3-16 показано оптимальное положение мазутовыпускных отверстий
для горелки НГМГ-4, установленной на котле ДКВР-6,5-14. При монтаже горелок нужно следить за тем, чтобы закрутка первичного (распыливающего) воздуха и вторичного воздуха, подаваемого для горения, производилась в одну и ту же сторону. На рис. 3-17 показана одна из конструкций вихревых горелок с паромеханической форсункой, разработанная ЦКТИ и серийно выпускаемая заводом «Ильмарине». Горелка состоит из паромеханической форсунки, двухзонного направляющего аппарата и газовой камеры с газовыпускными отверстиями. Горелка предназначена для сжигания мазута и природного газа.
|
Один из вариантов форсунки с паромеханическим распыливанием, применяемых в вихревых горелках, показан на рис. 3-18. Принцип действия форсунки заключается в следующем. Мазут по трубе 2 через распределительную шайбу 4 поступает в кольцевую камеру распылителя 5 и затем по тангенциальным каналам попадает в его завихрительную камеру. Закрученная струя мазута под действием центробежных сил прижимается к стенкам завихрительной камеры и, продолжая двигаться поступательно, срывается с кромки сопла распылителя 5, разбиваясь на множество мельчайших капель. Пар из трубы / поступает в полость между деталями, пропускающими мазут, и концевой гайкой 8. Из этой полости пар поступает через тангенциальные каналы в камеру парового завихрителя 6. Затем пар выходит под углом из цилиндрической щели и охватывает с внешней стороны распыленную струю мазута.
При расходах мазута, меньших 50 % номинального, давление мазута перед форсункой становится недостаточным'для хорошего качества распиливания и в форсунку дополнительно подается пар. Однако, так как расход пара не превышает 0,03 кг/кг,
подача его производится при всех нагрузках форсунки с давлением 70 — 200 кПа.
В то же время испытания показали, что
при расходах мазута
70 % и более подача
пара практически не
улучшает качества
распыливания. Давление мазута перед форсункой в зависимости
от ее номинальной
мощности выбирается
от 1,3 до 3,5 МПа. Ре
гулирование мощности
форсунки произво-
дится изменением давления мазута перед ней.
Качество работы мазутных форсунок с механическим и паромеханическим распыливанием зависит от тщательности изготовления, точности сборки и установки. Очень важно обеспечить плотность мазутного тракта во избежание попадания мазута в паровой канал, так как последнее приводит к закупорке ка нала из-за коксования мазута. При обслуживании форсунки необходимо систематически ее прочищать и заменять распылитель, который чаще выходит из строя, чем остальные детали. Абразивный износ внутренних поверхностей, особенно стенок распылителя, приводит к изменению формы факела, увеличению расхода топлива и укрупнению размера капель. Скорость износа зависит от загрязненности мазута механическими примесями, его состава, а также от давле-
|
ния подачи. Опыт показывает, что, несмотря на очистку мазута от механических примесей, наблюдается загрязнение входных каналов и распределительной шайбы форсунки. Это приводит к смещению факела относительно оси форсунки и ухудшению качества ее работы. При снижении производительности форсунки вследствие частичного закоксовывания или засорения температура стенок быстро растет, а это приводит к ускоренному закоксовыванию. Во избежание этого надо систематически следить за температурой и чистотой распылителей, а также характером факела. При появлении около корня факела темных полос, скоплений капель и разрывов необходимо проверить состояние
деталей форсунки.
На рис. 3-19 показана горелка РГМГ (ротационная газомазутная горелка) с встроенным вентилятором распыливающёго воздуха, выпускаемая серийно мощностью до 8 МВт. Горелки большей мощности выпускаются с отдельно устанавливаемым вентилятором распыливающёго воздуха.
Мазутная форсунка 11 горелки состоит из полого вала 17, на котором закреплены рабочее колесо 18 вентилятора распыливающёго воздуха, распыливающий стакан 13 и гайка-питатель 14. Вал 17 через клиноременную передачу 19 получает вращение от электродвигателя 20. Мазут подводится к штуцеру 3. В центральном отверстии вала расположена консольная топливная трубка 15, по которой мазут поступает в кольцевую внутреннюю полость гайки-питателя 14. В гайке-питателе имеются четыре радиальных канала, по которым под действием центробежных сил мазут вытекает на внутреннюю стенку распыливающёго стакана, образуя пленку. В стакане пленка перемещается в осевом направлении и затем срывается с кромки стакана, распадаясь на капли. При этом угол раскрытия образующегося конуса, если не подавать распыливающёго воздуха, близок к 180°. Для получения нужного угла раскрытия конуса и лучшего распыления мазута через завихритель 12 подается распиливающий (первичный) воздух. Первичный воздух поступает также через четыре отверстия в гайке-питателе в полость распыливающёго стакана 13, что предохраняет его от закоксовывания. Распыливающий стакан имеет конусообразную форму и отполирован.
|
Вторичный воздух поступает в улиточный короб 8 и из него направляется к завихрителю 16 и всасывающему патрубку первичного воздуха 7, в котором имеется шибер для регулирования количества воздуха, поступающего к распыливающему вентилятору. Распыливающий вентилятор создает напор около 5000 Па. Давление мазута не должно превышать 0,2 МПа.
Подробные промышленные испытания горелки РГМГ-10 выполнены ЦКТИ. Основные параметры горелки по данным этих испытаний показаны на рис. 3-20. В результате испытаний установлено, что диапазон регулирования мощности горелки — от 10 дб 100%. Доля первичного (распыливающёго) воздуха на номинальной нагрузке составляла примерно 10 % общего расхода
![]() |
воздуха, поданного на горение. Давление первичного воздуха на нагрузках 100—30 % номинальной поддерживалось равным 5000—6000 Па, а на нагрузках ниже 30 % номинальной — в пределах от 2500 до 3500 Па. При испытании сжигался мазут марки 40 и природный газ Дашавского месторождения с низшей теплотой сгорания 36,12 МДж.
При эксплуатации ротационных форсунок необходимо следить за чистотой внутренней поверхности распыливающего стакана, так как нагарообразование, смолистые и другие отложения резко ухудшают качество распыливания. Об отложениях на стенках распыливающего стакана можно судить по появлению в топке крупных летящих капель — «звездочек». В таких случаях форсунка должна быть отключена и выведена из воздушного короба. Для этого достаточно вывернуть барашки прижимного устройства и откатить мазутную часть горелки, которая имеет двойной шарнир. После этого следует очистить полость стакана деревянным, алюминиевым или красномедным ножом и промыть соляровым маслом или другим легким топливом. Уда-
лять нагар стальным инструментом нельзя, так как на стенке стакана останутся риски, что резко ухудшит качество распиливания мазута. Недопустимы также зазубрины, выбоины на кромке распыливающего стакана. Периодически следует проверять размах вибрации кромки стакана, который не должен превышать 0,06 мм.
Факел, выдаваемый горелкой, должен быть симметричным относительно геометрической оси горелки. Несимметричность факела и даже вибрационное горение могут возникать вследствие неправильного выполнения амбразуры или ее разрушения
|
в процессе эксплуатации. Периодически следует добавлять смазку в подшипниковые узлы, производя подачу ее шприцем до тех пор, пока она не начнет устойчиво выжиматься из контрольных отверстий.
При задевании топливной трубки за вал форсунки появляется резкий звенящий шум. Устранение этого достигается центровкой топливной трубки относительно отверстия вала форсунки. Резкий шум также может быть вызван задеванием колеса вентилятора за его корпус вследствие смещения ротора форсунки. Ликвидация этого Дефекта достигается регулировкой положения ротора с помощью прокладок, установленных в подшипниковых узлах. Правильность положения ротора проверяется через инспекционное отверстие в корпусе вентилятора. Несовпадение выходной кромки колеса вентилятора с выходной кромкой направляющего аппарата не должно превышать 0,5 мм.
На рис. 3-21 показана камера двухступенчатого сжигания топлива. Она состоит из паромеханической форсунки 2 с завихрителем первичного воздуха 4 и камеры горения, в которую по кольцевому каналу через завихритель 6 подается вторичный воздух. Основная часть воздуха (50—70 %) подается через мазутную форсунку, а остальная — через завихритель в камеру горения. Вторичный воздух, проходя по кольцевому каналу, охлаждает камеру горения. Распыленный в паромеханической форсунке мазут, попадая в зону высоких температур камеры горения, газифицируется и, смешавшись с вторичным воздухом, догорает в топке парогенератора.
Результаты испытания камер двухступенчатого сжигания показали их работоспособность и надежность при эксплуатации
под наддувом (давление в топке парогенератора составляло 2500 Па). При высокой удельной нагрузке топочного объема (1,2-103 МВт/м3) и коэффициенте избытка воздуха 1,05 потеря теплоты от химической неполноты горения отсутствовала.
При эксплуатации камер двухступенчатого сжигания необходимо следить за работой паромеханической форсунки* не допуская ее перегрева и закоксовывания. Следует также регулировать распределение первичного и вторичного воздуха, поддерживая распределение, заданное режимной картой, давление воздуха перед форсункой и завихрителем камеры горения.
При эксплуатации форсунок рассмотренных конструкций необходимо следить за сохранением производительности форсунки при неизменном давлении, за вязкостью мазута, отсутствием закоксовывания, поддержанием минимального коэффициента избытка воздуха. Нарушение производительности форсунки при неизменных давлении перед ней и вязкости мазута наблюдается при нарушении заданной точности изготовления и недостаточно тщательной сборке при ремонте. Погрешности изготовления оказывают тем большее влияние, чем меньше расчетная производительность форсунки. Небрежная сборка форсунок может привести к снижению производительности до уровня 40 % номинальной, а также способствует закоксовыванию форсунки.
Качество распыливания мазута существенно зависит от вязкости его перед форсункой. Кроме того, на распыливание топлива оказывают влияние поверхностное натяжение, плотность мазута и наличие механических примесей. Механические примеси, карбены и карбоиды уменьшают внутреннее сопротивление мазута распыливанию. При этом в процессе нагревания и длительного хранения дисперсность карбенов и карбоидов изме-меняется, что приводит к изменению качества распыливания мазута. Мазут, содержащий мелкодисперсные частицы, при прочих равных условиях распыливается на более мелкие капли по сравнению с мазутом, содержащим крупные частицы.
Нарушения нормального режима работы форсунок чаще всего происходят вследствие их закоксовывания. Многочисленные наблюдения за работой форсунок показали, что закоксовы-вание обусловлено термоокислительными процессами с образованием слоя кокса вследствие нагрева мазута стенками форсунки. Чем выше температура стенок форсунки, тем интенсивнее происходит отложение смол и увеличивается слой кокса. Температура стенки головки форсунки в значительной мере зависит от ее расположения относительно среза амбразуры. Часто при эксплуатации различных форсунок стремятся из-за коксовых отложений в амбразуре расположить головку форсунки на срезе амбразуры или даже несколько выдвинуть ее за пределы среза (рис. 3-22, а). Как показали испытания, такое положение головки форсунки не обеспечивает должного охлаждения ее. По данным испытаний ВТИ выдвижение головки за срез амбразуры приводит к резкому повышению температуры
металла ее стенки. Так, например, расположение головки на расстоянии 100 мм от среза амбразуры в направлении топочной камеры приводит к повышению температуры металла стенки до 500 °С. Надежное охлаждение головки форсунки обеспечивается при перемещении ее на расстоянии 100 мм от среза амбразуры в глубь горелки, как показано на рис. 3-22, б. При таком расположении головки температура металла стенки не превышает 200 °С и никакого ухудшения экономических показателей работы топки не наблюдается. Таким образом, в случае коксования амбразуры следует прежде всего проверить качество изго-
товления и сборки форсунки, а не перемещать ее в глубь топочной камеры.
Коэффициент избытка воздуха при сжигании сернистых мазутов не только влияет на экономичность работы котельного агрегата, но и определяет надежность работы хвостовых поверхностей нагрева и загрязнение воздушного бассейна выбросами. Первые лабораторные опыты по сжиганию мазута с коэффициентом избытка воздуха, близким к единице, были выполнены в СССР и показали возможность работы топки без химического недожога. Обычно принято считать коэффициенты избытка воздуха 1,00—1,02 предельно низкими; 1,02—1,05 низкими и более 1,15 высокими. В нормах теплового расчета котельных агрегатов рекомендуется принимать коэффициент избытка воздуха на выходе из топки 1,10. Для оценки коррозионной активности продуктов горения при сжигании сернистых мазутов существенной характеристикой является также температура точки росы и содержание серного ангидрида.
Опыт эксплуатации и испытания котельных агрегатов показал, что достижение низких и предельно низких коэффициентов избытка воздуха возможно только при точном порционировании
топлива и воздуха по всем установленным горелкам. Уменьшение числа горелок облегчает равномерное распределение между ними топлива и воздуха. Вязкость мазута перед форсунками особенно заметно влияет на потери теплоты от химической неполноты сгорания при низких коэффициентах избытка воздуха. На рис. 3-23 в качестве примера показано влияние вязкости на потери теплоты от химической неполноты горения при различном избытке воздуха по результатам испытаний ВТИ на одном из котлов, оборудованных форсунками с паромеханическим распыливанием мазута.
Компоновка форсунок также оказывает влияние на работу топочной камеры. В литературе указывается, что при встречной компоновке горелок обеспечить работу топки с низким коэффициентом избытка воздуха проще, чем при однофронтовой компоновке. На котлах малой производительности применяется, как правило, однофронтовая компоновка горелок, и это вызывает затруднения при организации процесса горения с низким коэффициентом избытка воздуха.
Устойчивость и качество работы мазутных форсунок различных конструкций в значительной мере зависят от воздухонаправляющих аппаратов. Для организации перемешивания распыленного мазута с воздухом современные мазутные форсунки оборудованы воздухонаправляющими аппаратами, производящими закрутку воздушного потока. Закрученная струя имеет ряд преимуществ по сравнению с прямоточной. Она обладает большой эжекционной способностью, провалом скорости в осевой области, при известных условиях переходящим в осевой обратный ток. Наличие осевого обратного тока обеспечивает непрерывное поступление горячих топочных газов к корню факела
и его стабилизацию.
Закрутка воздушного потока в воздухонаправляющих аппаратах мазутных форсунок чаще всего осуществляется установкой плоских или винтовых лопаток. Если воздух в форсунке для горения подается одним потоком, воздухонаправляющее устройство называют однопоточным, если двумя потоками — двухпоточным. В горелках типа ГМГ и НГМГ воздух подается двумя потоками и закрутка его производится плоскими лопатками.
При эксплуатации воздухонаправляющих аппаратов необходимо следить за состоянием лопаток, не допуская их загрязнения или закоксовывания. При ремонте воздухонаправляющих аппаратов и замене отдельных лопаток установка их должна проводиться по шаблону под одинаковым углом.
Существенное влияние на работу форсунок оказывает также качество и правильность выполнения амбразуры. Амбразуры должны быть выполнены по чертежу в соответствии с типом установленной форсунки. Ось амбразуры должна совпадать с осью форсунки. На рис. 3-24 в качестве примера показаны два типа амбразур (цилиндрическая и коническая), применяе-
мые для форсунок с пневматическим и паромеханическим распиливанием.
Зольность мазута не превышает 0,3 %, однако в эксплуатации наблюдаются загрязнения поверхностей нагрева плотными отложениями в зонах с температурой продуктов горения более 700 °G. Наиболее интенсивно загрязняются пароперегреватели и поверхности нагрева водогрейных котлов типа ПТВМ, имеющие небольшие площади поперечного сечения для прохода продуктов горения.
Обслуживание мазутных форсунок требует повышенного внимания. Необходимо следить за устойчивостью факела, не
допуская пульсации и неравномерного заполнения топочного объема. Пульсация факела может возникать вследствие поступления обводненного мазута, недостаточного его подогрева, загрязнения фильтров и сопл форсунок, шлакования амбразур, отложений на лопатках воздухонаправляющего аппарата или их коробления и ряда других нарушений режима горения. Неравномерное заполнение топочного объема факелом может привести к местному перегреву экранных труб или обмуровки топки. В связи с этим необходимо следить за дальнобойностью факела и окончанием горения в пределах топочной камеры.
Особенно внимательно следует производить розжиг форсунок, не допуская образования сажи, уноса несгоревших капелек мазута, подтекания его из форсунки, плохого горения или погасания растопочного факела, В форсунках с паромеханическим распыливанием необходимо сначала открывать подачу пара и только после этого подачу мазута. В форсунках с воздушным распыливанием сначала подается распиливающий воздух, а затем мазут.
Отложение сажи и унос несгоревших капелек мазута могут привести к хлопкам и взрывам, а также к горению в хвостовых поверхностях нагрева, которое обнаруживается по внезапному повышению температуры продуктов горения в соответствующем
газоходе.
Форсировка топки изменяется регулированием подачи мазута и воздуха одновременно ко всем форсункам или отключением отдельных форсунок. При установке двух-трех форсунок чаще всего одновременно регулируют расход мазута и воздуха на все форсунки: это качественное регулирование. На водогрейных котлах при установке большого числа форсунок применяют количественное регулирование, т. е. отключение отдельных форсунок для снижения форсировки топки. При установке форсунок ротационного типа, имеющих большой диапазон регулирования мощности (20—100%), применяют качественное регулирование, которое проще и надежнее.
ТОПКИ ДЛЯ СЖИГАНИЯ ГАЗА
В топках промышленных котельных агрегатов широко используется природный газ различных месторождений.
Из многочисленных конструкций газовых горелок для промышленных котельных агрегатов в настоящее время применяются инжекционные горелки полного предварительного смешения, горизонтальные и вертикальные щелевые горелки с принудительной подачей воздуха, комбинированные газомазутные и пылегазовые горелки.
Из различных конструкций инжекционных горелок полного предварительного смешения достаточно эффективными являются блочные инжекционные горелки, разработанные производственно-техническим предприятием «Промэнергогаз» на базе исследований и конструктивных схем, выполненных ЛНИИАКХ (Ленинградский научно-исследовательский институт Академии коммунального хозяйства). На рис. 3-25 показана блочная инжекционная горелка.
При необходимости сохранения твердого топлива в качестве резервного блочные инжекционные горелки рекомендуется устанавливать на боковых стенах топочной камеры. Горелки применяются для котлов производительностью до 10 т/ч. Колосниковая решетка топки при работе на газе во избежание перегрева и присоса воздуха закрывается листовым асбестом и засыпается битым шамотным кирпичом'. Розж иг горе лок, производится горящим запальником с тыльной стороны в следующем порядке. После выполнения всех операций по подготовке котла и продувке газопровода подносят горящий запальник к тыльной стороне смесителя горелки и, приоткрыв рабочую задвижку, устанавливают давление газа перед горелкой 2000—3000 Па. Затем, быстро передвигая запальник, поджигают газ в каждом смесителе и сразу же увеличивают давление газа перед горелкой до
5000—6000 Па с таким расчетом, чтобы горящие струйки 1газа из смесителя переместились в туннель горелки. Розжиг, горилки выполняют два человека. Все операции должны быть выполнены быстро и так, чтобы не произошел отрыв пламени от туннеля горелки. Если не удастся по каким-либо причинам быстро Поджечь газ в каждом смесителе, пуск горелки прекращают и после тщательней вентиляции топки в течение 15—20 мин вторично производят зажигание горелки. Следует также немедленно пре-
кратить подачу газа в горелку, если при увеличении давления газа произойдет погасание из-за отрыва пламени от туннеля. Регулирование производительности горелки производится постепенным изменением давления газа перед ней. Горелки устойчиво работают при изменении давления газа в пределах от 5000 до 85 000 Па.,
При эксплуатации топок, оборудованных блочными инжекционными горелками, необходимо следить за состоянием туннелей, своевременно производя их ремонт в случае разрушения. При переходе на резервное твердое топливо туннели всех горелок закладываются огнеупорным кирпичом, а с колосниковой решетки убирается битый шамотный кирпич. Для выполнения этих работ требуется расхолаживание топки.
При работе блочных горелок, как показали испытания, процесс горения заканчивается на расстоянии 18—20 калибров от выходного среза смесителя (за характерный размер принята ши-
рина огневой щели смесителя), т. е. при принятой в конструкции горелки ширине щели 60 мм длина факела не превышает 1200 мм. Следует учитывать, что горелки работают с низкими коэффициентами избытка воздуха при давлении газа перед горелкой не менее 20 000 Па. Зависимость коэффициента избытка воздуха на выходе из горелки от давления газа перед ней показана на рис. 3-26.
При устойчивом газоснабжении и резервном слоевом способе сжигания твердого топлива для котлоагрегатов производительностью до 20 т/ч применяются горизонтальные щелевые (подовые) горелки.
На рис. 3-27 показана установка горизонтальных щелевых горелок в топке переведенного на газ парового котла ДКВ-4-14, а на рис. 3-28 — в топке водогрейного котла ТВГ-8, предназначенного только для сжигания газа. Горизонтальные щелевые горелки просты по конструкции, однако при эксплуатации имеют ряд особенностей. Опыт эксплуатации показал, что при пониженных нагрузках котла вследствие затягивания пламени в щель происходит перегрев металла газового коллектора и преждевременный выход его из строя. Исследованиями установлено, что температура металла газового коллектора зависит от скорости газа внутри него, скорости воздуха, омывающего коллектор, и излучения огнеупорного материала щели. Во избежание перегрева газового коллектора скорость газа в нем должна быть не менее 7—8 м/с при минимальной нагрузке котельного
агрегата.
Диаметр газовыпускных отверстий горизонтальных щелевых горелок должен быть не менее 2 мм, так как при меньшем диаметре наблюдается закоксовывание отверстий плотными отложениями. Существенное влияние на качество работы горелок оказывает равномерность распределения воздуха по длине щели, которое зависит от состояния колосников решетки. Перед установкой горелок и выкладкой пода необходимо проверить состоя-
![]() |
ние колосникового полотна решетки и заменить дефектные колосники.
При эксплуатации топок, оборудованных подовыми горелками, на отдельных установках возникали пульсации пламени и продуктов горения, сопровождавшиеся однотонным гудением либо звуками, напоминающими сильную барабанную дробь.
Описанные явления возникали вследствие вибрационного горения. В основе механизма вибрационного горения лежит взаимодействие зоны горения и потока. Механизм пульсационного горения изучен недостаточно, и в связи с этим ликвидация вибраций в основном осуществляется эмпирически.
Процесс горения при работе подовых горелок заканчивается на расстоянии 17—20 калибров от газовыпускных отверстий. При этом длина факела увеличивается с уменьшением коэффициента избытка воздуха.
На рис. 3-29 показана установка вертикальных щелевых горелок на котле ДКВР-10-14. Установка горелок 'на боковых стенах топочной камеры позволяет осуществить переход на резервное твердое топливо без демонтажа горелочных устройств, Однако переход на твердое топливо требует закладки щелей горелок, открытия амбразур забрасывателей, снятия защитного слоя битого шамотного кирпича с колосниковой решетки. Эти операции могут быть выполнены без расхолаживания котла, однако требуют не менее четырех часов при хорошей организации работ. Обратный переход на газообразное топливо возможен только при расхолаживании котла, так как необходимо выполнить закладку амбразур забрасывателей.
Опыт эксплуатации и испытания вертикальных щелевых горелок показали, что они устойчиво работают в диапазоне изменения давления газа от 2500 до 35 000 Па, выдавая факел длиной около 20 калибров от газовыпускных отверстий.
При эксплуатации горелки необходимо следить за состоянием щелей, выполненных из огнеупорного кирпича, не допуская их разрушения. При пониженных нагрузках котла допу-
стима работа на двух противоположных горелках, расположенных ближе к фронту котла. Следует учитывать, что вертикальные щелевые горелки имеют небольшое сопротивление по воздушной стороне, поэтому для контроля давления воздуха необходимо устанавливать перед ними наклонные тягонапоромеры. На рис. 3-30 приведена зависимость расхода воздуха от его давления перед горелкой при различном коэффициенте избытка воздуха.
При резервном жидком топливе наиболее распространены комбинированные газомазутные горелки типов ГМГ, НГМГ (рис. 3-17, 3-15) и РГМГ (рис. 3-19). Газовая часть горелок
![]() |
![]() |
ГМГ и НГМГ включает в себя газовыпускные отверстия, расположенные на торцевой части газового ствола. У горелок РГМГ газовыпускные отверстия расположены в газораздающем коллекторе, имеющем форму кольца.
При работе на газе вентилятор распыливающего (первичного).воздуха у горелок типа НГМГ отключается и в канал первичного воздуха подается воздух из основного воздухопровода для охлаждения мазутной форсунки. Опыт эксплуатации показал, что при работе на мазуте возможно закоксовывание газовыпускных отверстий, особенно при неправильной установке мазутного ствола (см. рис. 3-16). Поэтому при наладочных испытаниях необходимо уточнять диаметр газовыпускных отверстий в зависимости от теплоты сгорания газа. При подборе отверстий их диаметр рассчитывается на скорость выхода газа при номинальной нагрузке в пределах от 60 до 90 м/с. Температуру газа перед газовыпускными отверстиями следует принимать около 50 °С. При плановых остановках котельного агрегата необходимо проверять диаметр газовыпускных отверстий и в случае их закоксовывания производить прочистку.
У горелок ГМГ при работе на газе мазутная форсунка удаляется, и в горелку подается небольшое количество первичного воздуха во избежание перегрева его завихрителя. Все рассмотренные горелки предназначены для раздельного сжигания газа и мазута. Однако кратковременная работа горелок на газе и мазуте в период перехода с одного вида топлива на другое допускается. В горелках РГМГ для удобства удаления форсунки из воздушного короба она крепится к кольцу-раме двухосным кронштейном, позволяющим ей совершать поступательное и вращательное движения. При выводе форсунки из воздушного короба центральное отверстие закрывается специальными захлопками.
При переводе пылеугольных топок на сжигание газа обычно применяются комбинированные пылегазовые горелки. В качестве примера пылегазовых горелок на рис. 3-31 показана горелка конструкции Оргэнергостроя с расходом природного газа 2000 м3/ч. При работе на газе подвижная часть телескопической трубы с чугунным насадком и конусом убирается внутрь горелки.
Опыт эксплуатации показал, что у горелки с периферийной выдачей газа в закрученный поток воздуха наблюдается нарушение плотности сочленения с обмуровкой топочной камеры. В результате воздействия газовоздушного потока на стенки амбразуры он через неплотности швов кирпичной кладки проникает в обмуровку. Если газовоздушная смесь попадает в топку и сгорает в ней, это не опасно, но возможно выбивание газовоздушной смеси в помещение цеха и загазовывание его. Для ликвидации утечек газа рекомендуется применять уплотнение в виде металлического кольца, которое закладывается в обмуровку (8 на рис. 3-31).
При эксплуатации горелок наблюдается также повреждение газовых коллекторов и оплавление амбразур. На' рис. 3-32 показаны различные формы применяемых газовых коллекторов и наиболее характерные места их повреждений.
Надежность розжига газовых горелок с „принудительной подачей воздуха зависит главным образом от положения запальника по отношению к амбразуре горелки и от плотности шиберов, регулирующих подачу воздуха в горелку. Розжиг каждой из установленных горелок должен производиться от индивидуального запальника, устанавливаемого в запальное отверстие. Устойчивость пламени запальника зависит от разрежения
в топке и плотности шибера, регулирующего подачу воздуха в горелку. В связи с этим перед вводом запальника в топку необходимо плотно закрыть шибер, регулирующий подачу воздуха, и отрегулировать разрежение в верхней части топки, которое должно составлять 20—30 Па. При высокой топке разрежение в ее верхней части перед розжигом горелки следует снизить до 10 Па, так как при этом разрежение в зоне горелки достигает 70—90 Па. Пламя запальника должно располагаться в непосредственной близости от амбразуры и над ней, как показано на рис. 3-33, а.
При устойчивой работе запальника подача газа в горелку производится плавно, так, чтобы давление газа не превышало 10—15 % номинального. Воспламенение газа, выходящего из горелки, должно происходить немедленно. Если газ, выходящий из горелки, сразу же не воспламенится, необходимо быстро закрыть подачу газа к горелке, удалить из топки запальник и провентилировать в течение 10—15 минут топочную камеру. Повторный розжиг горелки разрешается только после устранения причин, воспрепятствовавших ее нормальному пуску.
При внесении запальника в топку и розжиге горелки необходимо соблюдать осторожность, находясь в стороне от запального отверстия. После воспламенения газа, выходящего из горелки, производят подачу воздуха с таким расчетом, чтобы светимость пламени уменьшилась,, но не произошло отрыва его от горелки. Для повышения производительности горелки сначала увеличивают на 10—15 % давление газа, а затем соответственно давление воздуха, восстанавливая прежнее разрежение в топке. При устойчивой работе первой горелки приступают последовательно к розжигу остальных горелок.
Отключение
|
|
Автоматическое растормаживание колес: Тормозные устройства колес предназначены для уменьшения длины пробега и улучшения маневрирования ВС при...
История создания датчика движения: Первый прибор для обнаружения движения был изобретен немецким физиком Генрихом Герцем...
Организация стока поверхностных вод: Наибольшее количество влаги на земном шаре испаряется с поверхности морей и океанов (88‰)...
Поперечные профили набережных и береговой полосы: На городских территориях берегоукрепление проектируют с учетом технических и экономических требований, но особое значение придают эстетическим...
© cyberpedia.su 2017-2024 - Не является автором материалов. Исключительное право сохранено за автором текста.
Если вы не хотите, чтобы данный материал был у нас на сайте, перейдите по ссылке: Нарушение авторских прав. Мы поможем в написании вашей работы!