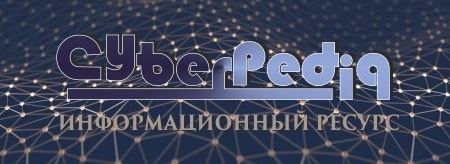
Наброски и зарисовки растений, плодов, цветов: Освоить конструктивное построение структуры дерева через зарисовки отдельных деревьев, группы деревьев...
Археология об основании Рима: Новые раскопки проясняют и такой острый дискуссионный вопрос, как дата самого возникновения Рима...
Топ:
Устройство и оснащение процедурного кабинета: Решающая роль в обеспечении правильного лечения пациентов отводится процедурной медсестре...
Когда производится ограждение поезда, остановившегося на перегоне: Во всех случаях немедленно должно быть ограждено место препятствия для движения поездов на смежном пути двухпутного...
Проблема типологии научных революций: Глобальные научные революции и типы научной рациональности...
Интересное:
Аура как энергетическое поле: многослойную ауру человека можно представить себе подобным...
Финансовый рынок и его значение в управлении денежными потоками на современном этапе: любому предприятию для расширения производства и увеличения прибыли нужны...
Влияние предпринимательской среды на эффективное функционирование предприятия: Предпринимательская среда – это совокупность внешних и внутренних факторов, оказывающих влияние на функционирование фирмы...
Дисциплины:
![]() |
![]() |
5.00
из
|
Заказать работу |
Основы металлургии
Конспект лекций по дисциплине
«Основы металлургии»
для студентов специальности 133 «Отраслевое машиностроение», специализации «Металлургическое оборудование»
всех форм обучения
Мариуполь
УДК 531.8:621.771(07)
Основы металлургии [Электронный ресурс]: конспект лекций по курсу «Основы металлургии» специальности 133 «Отраслевое машиностроение», специализации «Металлургическое оборудование» всех форм обучения / сост. А. В. Ширяев. – Мариуполь: ГВУЗ «ПГТУ», 2017. – 55 с. – Режим доступа:
Конспект лекций включает содержание, краткий лекционный материал, согласно программе курса, контрольные вопросы, список основной, дополнительной литературы, информационные ресурсы.
Изложены основы современных методов расчета металлургического оборудования. Даны способы и методики исследования прочности узлов и деталей оборудования, методы расчета технологических нагрузок.
Автор А. В. Ширяев, канд. техн. наук, доцент
Рецензент А. А. Ищенко, д-р техн. наук, проф.
Утверждено
на заседании кафедры механического оборудования
заводов чёрной металлургии,
протокол № 9 от 06 января 2017 г.
Утверждено
методической комиссией факультета
машиностроения и сварки,
протокол № 10 от 10 января 2017 г.
Ó ГВУЗ «ПГТУ», 2017
СОДЕРЖАНИЕ
ВВЕДЕНИЕ. …...5
Лекция 1. Металлургические процессы ………..……………….6
1.1 Металлургическиепроцессы …………………………………………...6
1.2 Производство черных металлов и сплавов (черная металлургия)…….6
1.3 Современное металлургическое производство и его продукция……...8
Лекция 2.Агломерационное и доменное производство………………………………………………………………….10
2.1 Агломерационное производство………………………………………10
2.2 Доменное производство………………………………………………..16
Лекция 3.Производство стали…………………………………….24
3.1 Основные положения…………………………………………………..24
3.2 Кислородно-конверторное производство……………………………..25
3.3 Мартеновское производство.……………………………..…………....28
Лекция 4. Разливка стали………………………………………….31
4.1 Производство (переплав) стали в электропечах. Способы улучшения качества жидкой стали. Разливка стали…………………………………………..31
4.2 Классификация и маркировка конструкционных материалов………36
Лекция 5.Литейное производство………………………………40
5.1 Литейное производство.………………………………………………..40
Лекция 6. Обработка метала давлением....................................42
6.1 Основные способы ОМД……………………………………………….42
6.2 Влияние ОМД на структуру и свойства металла……………………..42
6.3 Факторы, влияющие на пластичность при ОМД……………………..43
Лекция 7.Прокатка……………………………………………………..44
7.1 Продукция прокатного производства…………………………………44
7.2 Инструмент и оборудование для прокатки……………………………45
7.3 Технологический процесс производства основных видов проката…46
Лекция 8.Ковка, штамповка……………………………………….51
8.1 Ковка……………………………………………………………………..51
8.2 Штамповка…………………………………….………………………...52
СПИСОК РЕКОМЕНДОВАННЫХ ИСТОЧНИКОВ ……………………54
Ведение
Дисциплина «Основы металлургии» является одной из специальных дисциплин при подготовке бакалавра специальности 133 – «Отраслевое машиностроение».
Целью преподавания учебной дисциплины «Основы металлургии» является предоставление студенту необходимых знаний и умений относительно технологии и механического оборудования металлургических цехов, необходимых для практической деятельности. А также сформировать у студента теоретические знания, навыки и умения, которые позволят, пользуясь пониманием основ технологии и механического оборудования и их использования в инженерных задачах, подготовить специалистов к практической деятельности в отрасли машиностроения.
Предметомизучения учебной дисциплины являются основы технологии, знаний металлургического оборудования и использование этих знаний в инженерной деятельности.
Согласно с требованиями образовательно-профессиональной программы студенты должны знать назначение, устройство и условия работы металлургического оборудования, его достоинства и недостатки; основы технологии производства чёрных металлов; перспективы и направления металлургии.
В течение семестра по материалу студент прослушивает лекции, выполняет лабораторные работы, самостоятельно изучает материал и получает зачёт.
Дисциплина «Основы металлургии» базируется на дисциплинах «Технология конструкционных материалов», «Материаловедение».
Основные знания по данному предмету студенты получают как на лекциях, лабораторных занятиях занятиях, консультациях так и выполнении самостоятельной работы.
Конспект лекций по дисциплине «Основы металлургии» для студентов специальности «Металлургическое оборудование» всех форм обучения является вспомогательным пособием для изучения дисциплины и не является источником, на который можно делать ссылки в литературном обзоре и т.д.
Первоисточниками являются печатные издания, приведенные в разделе «СПИСОК РЕКОМЕНДОВАННЫХ ИСТОЧНИКОВ».
Для подготовки и успешного сдачи зачета необходимо изучить литературу, перерисовать необходимые схемы, усвоить материал, выполнить требования учебного процесса и подтвердить свои знания на собеседовании с преподавателем.
Металлургические процессы
Металлургическими процессами называются процессы изготовления материалов (металлов, сплавов). Делятся на черную металлургию – получение так называемых «черных» сплавов – чугун, сталь и цветную металлургию – чистые цветные металлы и их сплавы: медь, бронза, латунь, алюминий, магний, титан и их сплавов. Получают металлы и сплавы из руд и других исходных материалов.
Способы: пирометаллургический, электрометаллургический, гидрометаллургический, химикометаллургический, порошковая металлургия, электронно-лучевой способ, плазменный и др.
Пирометаллургический – производство сплавов путем плавления руд с образованием шлака. Применяют топливо твердое или газообразное.
Электрометаллургический – выплавка сплавов и металлов путем использования тепла электрической энергии. Может также основан на электролизе растворов или расплавов (производство алюминия из глинозема).
Гидрометаллургический – основан на выщелачивании металлов из руд.
Химикометаллургический – сначала проводят химические реакции, затем продукты переплавляют (например, производство титана).
Основные положения
Сущность любого металлургического передела чугуна в сталь- снижение содержания углерода и примесей путем их избирательного окисления и перевода в шлак и газы в процессе плавки. Содержание углерода в стали менее 2,14%.
Основные материалы для производства стали - передельный чугун и стальной лом (скрап).
Какие же основные реакции проходят при выплавке стали?
Т.к. в чугуне в наибольшем количестве содержится Fe, то при подаче кислорода, в первую очередь, происходит его окисление. Одновременно, но с меньшей скоростью окисляются С, Si, P, Mn, и др. Оксид железа FeO при высоких температурах растворяется в железе и окисляет эти элементы, как химически более активные, а само железо восстанавливается. Чем больше FeO в расплаве тем активнее окисляются примеси. Поэтому для ускорения процесса окисления железа добавляют железную руду и окалину.
Этапы выплавки стали. Первый этап - расплавление шихты и нагрев ванны жидкого металла. Температура при этом высока, интенсивно проходит окисление железа и окисление кремния Si, фосфора P, марганца Mn (реакции экзотермические - с выделением тепла). Наиболее важная задача этапа - удаление фосфора P путем соединения с окисью кальция CaO, и перемещение его в шлак. Для повышения содержания FeO на первом этапе в ванну добавляют железную руду. Периодически удаляют фосфористый шлак и вводят добавки СаО.
Второй этап – «кипение» металлической ванны - начинается по мере прогрева до более высоких температур. Интенсивно протекает реакция окисления углерода. Пузырьки оксида углерода вызывают «кипение» ванны. При этом снижается содержание углерода до требуемого, выравнивается температура по объему ванны, частично удаляются неметаллы включения, прилипающие к всплывающим пузырькам, а также другие газы. Поэтому этап «кипения» ванны - основной в процессе выплавки стали. На этом же этапе происходит удаление серы S в шлак (чем выше температура тем интенсивнее происходит соединение серы с кальцием). Соединение CaS нерастворимо в железе, поэтому оно растворяется в шлаке.
Третий этап (завершающий) - раскисление стали - восстановление оксида железа из его окиси. В готовой стали FeO – вредная примесь. Существуют два способа раскисления: осаждающий и диффузионный.
Осаждающий - введение прямо в жидкую сталь растворимых раскислителей – ферросплавов (FeMn, FeSi, Al и др.). Образуются оксиды MnO, SiO2, Al2O3 и др., которые всплывают в шлак.
Диффузионное раскисление - раскисление шлаком. Ферросплавы FeMn, FeSi и др. вводят в шлак. В шлаке уменьшается содержание FeO, которая затем из стали начинает переходить в шлак.
В этот период для получения легированной стали вводят легирующие элементы Ni, Co, Mo, Cu, Si, Mn, Al, Cr, V, Ti, др. Их могут вводить прямо в ковш после слива стали.
В зависимости от степени раскисления выплавляют спокойные, кипящие и полуспокойные стали. Спокойная сталь получается при полном раскислении в печи и в ковше, кипящая – при неполном раскисление в печи, и этот процесс продолжается в изложнице. Выделяющийся газ СО способствует удалению N, H2. В слитках остаются пузырьки, но металл практически не содержит неметаллических включений, поэтому «кипящие» марки стали - очень пластичные. Полуспокойная сталь - промежуточная между спокойной и кипящей.
Мартеновское производство
Мартеновская печь (рис.3.3) — пламенная отражательная регенеративная печь. Она имеет рабочее плавильное пространство, ограниченное снизу подиной, сверху сводом, а с боков передней 5 и задней стенками. Подина имеет форму ванны с откосами по направлению к стенкам печи.
Свод мартеновской печи делают из огнеупорного кирпича. В передней стенке печи имеются загрузочные окна 4 для подачи шихты и флюса, а в задней — отверстие (летка)для выпуска готовой стали. Головки печи 2 служат для смешения топлива (мазута или газа) с воздухом и подачи этой смеси в плавильное пространство.
Для подогрева воздуха и газа (при работе на низкокалорийном газе) печь имеет два регенератора 1. Регенератор—это камера, в которой размещена насадка — огнеупорный кирпич.
Газовый факел 7 способствует окислению примесей шихты 6. Для интенсификации процесса окисления в жидкий металл подают кислород при помощи фурм 3. Мартеновский газ удаляется через систему газоотводов, систему газоочистки (не показана) и дымовую трубу 8.
В зависимости от состава шихты может производиться два вида плавки: «скрап – процесс», в котором шихта - стальной лом и 25-45% чушкового передельного чугуна (жидкого чугуна нет); «скрап- рудный процесс» - 55-75% жидкого чугуна, остальное скрап и железная руда.
Технология скрап-рудного процесса.
1. Завалочная машина через окна загружает железную руду и известняк
2. Их прогрев
3. Подача скрап (стального лома)
4. Прогрев скрапа
5. Заливка жидкого чугуна
6. Период плавки скрапа. Интенсивное окисление примесей. Раствор SiO2, P2O3, MnO, CaO и извести образуют шлак. Частично окисляется углерод.
7. Период «кипения» - загружают руду, или продувают ванну металла кислородом. Интенсивное окисление углерода с образованием СО. Подачу топлива и воздуха отключают и удаляют шлак через загрузочные окна. Для удаления серы добавляют новый шлак - известь с добавлением боксита или плавикового шпата. Образуемое соединение CaS всплывает в шлак. В период "кипения" сталь доводится до заданного химического состава.
8. Раскисление в два этапа: а) в период "кипения" прекращают подачу руды и добавляют раскилители (FeMn, FeSi, Al); б) окончательно раскискисляют сталь, добавляя Al и FeSi в ковш после выпуска стали из печи.
9. Отбор контрольных проб.
10. Выпуск стали в ковши. Для этого сверлят, или пробивают леточную массу в летке.
Мартеновским способом можно выплавить практически любые марки стали.
Схема грузопотоков мартеновского цеха представлена на рис. 3.4.
![]() |
Контрольные вопросы
1. Чем отличается чугун от стали?
2. Сущность процесса выплавки стали?
3. Что добавляют в расплав для ускорения образования FeO?
4. Что происходит на этапе расплавления шихты?
5. Что происходит на этапе "кипения" стали?
6. Что происходит при раскислении стали?
7. Что является окислителем углерода в кислородно-конверторном способе?
8. Что является окислителем углерода в мартеновском производстве?
9. В чем принципиальное различие кислородно-конверторного и мартеновского производства стали?
Лекция 4. Разливка стали
План
4.1 Производство (переплав) стали в электропечах. Способы улучшения качества жидкой стали. Разливка стали
4.2 Классификация и маркировка конструкционных материалов
4.1 Производство (переплав) стали в электропечах. Способы улучшения качества жидкой стали. Разливка стали
Электросталеплавильные печи предназначены для переплава низкокачественной стали и получения стали высокого качества, углеродистой, легированной. Преимущество переплава в электропечах – имеется возможность получать высокую температуру металла, создавать любую атмосферу (окислительную, восстановительную, нейтральную, вакуум), что позволяет выплавлять сталь любого состава.
На рис. 4.1 представлена конструкция дуговой электросталеплавильной печи с поворачивающимся сводом ДСП-80. Корпус 1 печи установлен на роликах в люльке 3, опирающейся своими сегментами 21 на фундаментные балки 4. при сливе металла и скачивании шлака печь наклоняется двумя реечными механизмами с электроприводами 5. Загрузка печи производится сверху специальной загрузочной бадьей 20. Для завалки шихты свод 2 приподнимают цепным механизмом 8 и отводят в сторону вместе с полупорталом 6 посредством механизма поворота свода 11. Опора 7 полупортала закреплена в люльке 3. Для поворота корпуса на некоторый угол в обе стороны служит механизм поворота 9. Электрод 14 закрепляют на концах электрододержателя 15 механизма зажима 16; каретки электрододержателей перемещаются по колоннам 17. Ток подводится к печи от трансформатора гибкими шинами 18. Для каждого электрода предусмотрен свой независимый механизм перемещения 10, расположенный на площадке полупортала. Жидкий металл сливают через носок 13. Заправку подины (днища), скачивание шлака, загрузку ферросплавов, шлакообразующих и легирующих элементов выполняют через рабочее окно 12, снабженное заслонкой с механизмом подъема. В средней части люльки размещено устройство 19 для электромагнитного перемешивания металла в ванне.
Технология плавки на углеродистой шихте (для производства конструкционных сталей):
1) Загрузка шихты: стальной лом (90%),чушковый передельный чугун (до 10%), электродный бой или кокс для науглераживания металла и известь 2-3%.
2) Опускание электродов и включение тока.
3) Плавление шихты. Окисление Fe, Si, P, Mn и частичное - углерода кислородом воздуха и оксидами шихты и окалины.
4) Нагрев металла и шлака на 1500-15400 С. Загрузка руды и извести - период "кипения". Окисление углерода.
5) Окончание «кипения» (содержание С < заданного). Удаление шлака.
6) Удаление серы и раскисление стали, доведение химсостава. Для этого добавляют MnSi, CaSi (раскислители), затем – известь. Затем в шлак вводят еще (после образования шлака) известь, CaF, молотый кокс, FeSi – для раскисления. Шлак становится белым. В этой период удаляется S с образованием CaS.
7) Отбор проб, при необходимости добавление ферросплавов, окончательное окисление Al и Ca и доводка стали до заданных параметров.
8) Выпуск стали в ковш.
![]() |
Способы улучшения качества жидкой стали. После плавки даже в качественной стали остаются примеси, азы, неметаллические включения, поэтому дополнительно производится обработка жидкой стали в ковше, вакуумирование и т.д. Рассмотрим некоторые способы улучшения качества стали.
1) Обработка синтетическим шлаком: вначале в ковш заливают жидкий шлак - 55% CaО, 45% Al2O3 и SiO2, MnO. Затем в ковш заливают жидкую сталь. Сталь и шлак перемешиваются, за счет большой площади контакта происходит интенсивное удаление S, P и др. примесей, а также газов. Шлак сливают.
2) Электрошлаковый переплав: отливается стальной слиток – электрод. Затем его опускают в специальную изложницу (второй электрод), погружая в жидкий шлак. При прохождении тока через слиток, он нагревается и расплавленные капли стали очищаются, проходя через шлак. Таким способом выплавляют особовысококачественные стали.
3) Вакуумирование стали. Жидкий металл помещают в разреженную атмосферу, при этом удаляются растворенные в металле газы, одновременно подаются специальные добавки и производится очистка от неметаллических примесей.
4) Вакуумно-дуговой и вакуумно-индукционный переплав в специальных печах для получения высококачественного металла.
Разливка стали. Разливка стали может выполняться двумя способами. Сталь из печи сливают в ковш, затем производится разливка или в изложницы, или на машине непрерывного литья заготовок (МНЛЗ).
Разливка слитков производится двумя способами: сверху и сифонная (несколько слитков через специальную систему каналов - снизу).
Общие недостатки разливки в слитки: низкая производительность; часть слитка приходится удалять (из-за наличия в верхней и нижней частях газов, неметаллических включений), а это - потери металла; необходимость последующей прокатки на обжимных станах.
В изложницы сверху (рис. 4.2, а) сталь разливают непосредственно из ковша 1.
При сифонной разливке (рис. 4.2, б) сталью заполняют одновременно несколько изложниц (4—6). Изложницы устанавливают на поддоне 6, в центре которого располагается центровой литник 3, футерованный огнеупорными трубками 4, соединенный каналами 7 с изложницами. Жидкая сталь 2 из ковша 1 поступает в центровой литник и снизу плавно без разбрызгивания заполняет изложницы 5, закрытые сверху прибыльной надставкой 8 с футеровкой 9. Поверхность слитка получается чистой, можно разливать большую массу металла одновременно в несколько изложниц. Для обычных углеродистых сталей используют разливку сверху, а для легированных и высококачественных — разливку сифоном.
Разливка на машинах непрерывного литья заготовок (МНЛЗ). Преимущества: непрерывность, высокая производительность, практически любое поперечное сечение слитка, ликвидация прокатки на обжимных станах, т.к. получают готовые литые слябы, заготовки и др.
Применяются различные типы МНЛЗ, но наиболее распространенная - криволинейная МНЛЗ.
Суть процесса: сталь разливается в водоохлаждаемую "изложницу'' без дна – кристаллизатор, в котором образуется твердая корочка по периметру слитка (внутри – жидкий металл) и слиток, застывая, постепенно опускается вниз.
Перед началом разливки в кристаллизатор помещают затравку (временное ''дно'' кристаллизатора), затем, после выхода слитка ее специальным устройством отделяют и убирают. Выход готовых заготовок - 96-98 %.
В состав двухручьевой слябовой машины криволинейного типа МНЛЗ входят (рис. 4.3): сталеразливочный стенд 1, тележка 2 с круговым движением для промежуточного ковша 3, радиальный кристаллизатор 4 с механизмом качания 5, верхняя и нижняя секции неприводной роликовой проводки 6, криволинейный участок приводной роликовой проводки 7, пружинно-винтовой механизм 8 для перемещения и прижатия роликов, механизм привода вращения рабочих роликов
![]() |
11, роликовые секции горизонтального участка 9, самоходная машина 10 для ввода затравки в кристаллизатор, а также машина газовой резки слитка на мерные длины, устройство с криволинейными направляющими для подъема и опускания роликовых секций при их замене, уборочные рольганги и механизмы для передачи и штабелирования слябов.
Кристаллизация и строение слитков.
Залитая в изложницу сталь отдает теплоту ее стенкам, поэтому затвердение - у стенок. Сталь застывает в виде кристаллов дендридной формы. В зависимости от степени раскисления изменяется строение слитка. У слитков из спокойной стали (изложницы с расширением кверху) строение плотное, у слитков из кипящих сталей (изложницы с расширением книзу) внутри имеются «соты» - застывшие пузыри СО.
Спокойная сталь (рис. 4.4, а) затвердевает без выделения газов, в верхней части слитка образуется усадочная раковина 1, а в средней — усадочная осевая рыхлость.
Слиток спокойной стали (рис.4.4, а) имеет следующее строение: тонкую наружную корку А из мелких равноосных кристаллов; зону Б крупных столбчатых кристаллов (дендритов); зону В крупных, неориентированных кристаллов; конус осаждения Г — мелкокристаллическую зону у донной части слитка. Прибыльную и подприбыльную части слитка, а также донную его часть при прокатке отрезают.
В слитках кипящей стали(рис.4.4, б) не образуется усадочная раковина: усадка стали рассредоточена по полостям газовых пузырей, возникающих при кипении стали в изложнице. При прокатке слитка газовые пузыри завариваются. Слиток кипящей стали имеет следующее строение:плотную наружную корку А без пузырей, из мелких кристаллитов, зону сотовых пузырей П, вытянутых к оси слитка и располагающихся между кристаллитами Б, зону В неориентированных кристаллов, промежуточную плотную зону С, зону вторичных круглых пузырей К и среднюю зону Д с отдельными пузырями, которых больше в верхней части слитка.
Строительные – это стали углеродистые и низколегированные, обыкновенного качества (группа А).
2) Машиностроительные конструкционные стали применяются для изготовления деталей машин. Их главная характеристика – механические свойства. Содержание углерода - в пределах 0,05 ¸ 0,75%.
3) Инструментальные стали характеризуются высокой твердостью, прочностью и износостойкостью. Твердость и вязкость зависят от содержания углерода и легирующих элементов.
4) Машиностроительные стали специального назначения характеризуются высокими механическими свойствами при низких и высоких температурах; физическими, химическими и технологическими свойствами.
5) Стали с особыми физическими свойствами получаются в результате специального легирования и термообработки. Применяются в приборостроении, электронной, радиотехнической промышленности и т. д.
6) Стали с особыми химическими свойствами (стойкие к коррозии в агрегатных средах) характеризуются тем, что содержат не менее 12,5 – 13% Cr, Ni.
Маркировка сталей.
1) Стали обыкновенного качества (группа А) (по ГОСТ 380 - …) обозначаются: Ст 0 – Ст 6 – цифра – десятые доли С, после цифр пишется ГОСТ. (Например: Ст 5 ГОСТ 380 – 93 содержит 0,5% углерода);
2) Качественные стали (группа Б) (ГОСТ 1050 - …), высококачественные и особо высококачественные (группа В). Содержание углерода указывают в начале марки цифрой, соответствующей его содержанию:
- в сотых долях % при содержании С<0,75% (конструкционные стали).
- в десятых долях % для сталей с содержанием C > 0,75% (инструментальные стали, валковые стали и др.).
Пример: Сталь 10 ГОСТ 1050-93 (до 0,1% углерода); Сталь 50 ГОСТ 1050-93 (0,5% С).
Обозначение легирующих элементов в маркировке: Н (Никель), Г (марГанец), Х (Хром), С (Кремний – Силициум), Ю (алЮминий), Ф (Ванадий), Т (Титан), М (Молибден), В (Вольфрам), К (Кобальт).
Если после буквы нет цифры, то сталь содержит»1¸1,5% легирующего элемента (кроме Mo, V, содержание которых в сталях до 0,2 – 0,3%), наличие цифры после буквы указывает содержание в процентах легирующего элемента.
Пример:
Сталь 9Х – 0,9% С, Cr»1 -1,5%.
Сталь 9Х2 – 0,95% С, 1,5-2,5% Cr.
Сталь 75Х2Г3Н5МФ4 – 0,75% С, около 2% Cr, Мn - около 3,0%, Ni – 5,0%, Мо – до 0,3%, V до 0,4%.
Обозначение высококачественной стали, в отличие от качественной – в конце ставится «А». Пример: 30ХНМ – качественная, а 30ХНМА и У10А – высококачественная.
ИСКЛЮЧЕНИЯ: Для некоторых высококачественных сталей применяются другие обозначения и букву «А» сзади не ставят. Например, для легированных сталей с особыми физическими свойствами, они - всегда высококачественные.
Пример: высококачественные электрошлакового переплава – в конце маркировки – буква «Ш» (7ХСМФШ); шарикоподшипниковые перед цифрами буквы «ШХ» (ШХ15 – шарикоподшипниковая, 1,5% Cr); быстрорежущие сложнолегированные стали – буква «Р», следующая за ней цифра обозначает процентное содержание в ней вольфрама (в десятых долях) Р20 – 2,0% W; электротехнические «Э», цифра обозначает содержание кремния (Si) (Э18 – 1,8% Si).
Маркировка цветных металлов и сплавов.
Алюминиевые сплавы – сплавы деформируемые и литейные, и те и другие могут быть не упрочняемые и упрочняемые термической обработкой.
1. Деформируемые – хорошо обрабатываются прокаткой, ковкой, штамповкой.
Не упрочняемые термообработкой – Аl – Mn (АМц) и Al – Mg (АМг).
Упрочняемые термообработкой – сплавы Al – Cu – Mg, с добавкой некоторых элементов, а также высокопрочные и жаропрочные сплавы сложного химического состава:
- дуралюмины (Д16 - Д18) – 3,8¸4,8% Cu, 0,4 – 1,8% Mg, 0,4 – 0,9% Mn. После термообработки обладают высокой прочностью и удлинением;
- ковочные сплавы (АК6 – АК8) – 1,8 – 4,8% Cu, 0,4 - 0,8% Mg, 0,4 –1% Mn, 0,6¸1,2%. Высокая ковкость и прочность после термообработки.
2. Литейные сплавы:
(Аl –Si) 10 – 13% Si – Al2, AЛ9;
(Al – Cu) – 4,5 – 5,3% Cu и до 1% Mn – АЛ7, АЛ9 и др.;
(Al – Mg) - 9,5 – 11,5% Mg – коррозионностойкие литейные АЛ8, АЛ13.
Магниевые сплавы - деформируемые и литейные, не упрочняемые и упрочняемые термообработкой.
1. Деформируемые сплавы МА2, МА8 - до 2% Mn, до 5% Al, десятые доли церия.
2. Литейные МЛ6, МЛ3 - 2,5 – 9% Al, 0,5 – 1,5% Zn, 0,15 – 0,5% Mn.
Медь и её сплавы.
1. Технически чистая медь применяется для проводников электрического тока. Маркировка: МО, МО1, М2 и т. д. – в зависимости от чистоты меди.
2. Бронзы - сплавы меди c оловом – 4 – 33% Sn, свинцом (30% Pb), алюминием – 5 – 11% Al, кремнием (4 – 5% Si), и др. В маркировке начальные буквы «Бр».
3. Латуни – сплав меди Cu c цинком Zn, могут содержать до 50% Zn, с добавлениями Al, Si, Ni, Mn.
Пример: ЛЦ40Мц1,5 – латунь, содержащая 40% Zn, 1.5 Mn, остальное - Cu.
Литература: [4],[7],[14], [10]
Контрольные вопросы
1. Преимущества выплавки стали в электропечах?
2. Состав шихты дуговой электропечи?
3. Способы улучшения качества жидкой стали?
4. Виды разливки в изложницы, их недостатки?
5. Преимущества разливки на МНЛЗ?
6. Отличие слитка спокойной стали от кипящей?
7. По каким признакам классифицируются стали?
8. Как обозначается содержание углерода в сталях обыкновенного качества и качественных?
9. Перечислите обозначение легирующих элементов?
10. Что означают цифры после буквы легирующего элемента, а для Мо и V?
Литейное производство
Литейное производство – процесс получения детали путём заливки расплавленного металла в заранее приготовленную форму, в которой металл кристаллизуется. Литьем изготавливают крупные детали: станины, корпуса редукторов и т.д.
Краткий технологический процесс:
1.Изготовление модели и стержневых ящиков.
2.Приготовление формовочных смесей.
3.Изготовление форм.
4.Приготовление сплава.
5.Заливка сплава в форму.
6.Извлечение отливки из формы, осмотр поверхности, ремонт и отгрузка.
Рассмотрим техпроцесс подробно по стадиям:
1.Изготовление модели и стержневых ящиков.
Модель и стержневой ящик составляют литейный комплекс. Изготавливают модели из древесины, пластмассы и др. Из металла – если модель серийная.
Модель определяет внешние контуры детали, но изготавливается с припусками и допусками.
Припуск – сознательное увеличение (уменьшение для отверстий) размеров на усадку материала (после остывания). Допуск – изменение размеров на обработку, т.к. на поверхности могут быть раковины и др. дефекты. Пример допусков: чугун – 2-10 мм на стороны, сталь – 4-28 мм.
Модели также выполняются с боковыми уклонами для извлечения из формы (0,5 – 2% от размера).
Модель выполняется со «знаками» (выемками) для фиксации стержня в случае изготовления детали с отверстием.
2. Приготовление формовочных смесей.
Изготавливают смеси из кварцевого песка (SiO2), огнеупорных глин, воды и специальных добавок.
Формовочные и стержневые материалы делятся на облицовочные, наполнители, единые.
Облицовочные – для изготовления части формы, которая непосредственно контактирует с поверхностью детали в случае, если требуется высокое качество. Изготавливается из свежих материалов.
Наполнители – для заполнения остальной части формы - из материалов использованных ранее. Их предварительно обрабатывают: удаляют скрап, размалывают и сепарируют магнитами.
![]() |
Единые – смесь свежих и б.у. материалов. Применяются для изготовления деталей, для которых не требуются высокое качество поверхности.
В смеси добавляют специальные добавки: для придания смеси специальных свойств: прочности; газопроницаемости; неприлипаемости. Прочность обеспечивает «жидкое стекло» (силикатный клей); газопроницаемость – опилки; неприлипаемость – смазки (графитовые и др.)
3. Изготовление форм производится путём уплотнения формовочной смеси по модели. Дополнительная оснастка:
1) Подмодельная плита (дерево, металл);
2) Опоки – деревянный (или металлический) ящик без днища;
3) Наполнительные рамки – устанавливаются на опоки, чтобы гарантировать и определить наполнение формы смесью.
4.Приготовление сплава:
Чушки (слитки) из чугуна, стали, бронзы, латуни, алюминия и т.д. расплавляют в печи вагранке.
5. Заливка сплава в форму
Заливают из ковша в специальный литейный комплекс.
6. Извлечение отливки. Форма, приготовленная из смеси разрушается (форма из металла - раскрывается).
На рис. 5.1 изображены стадии изготовления детали литьем и оснастка, необходимая для этого. На рис. 5.1, а изображена готовая форма: 1 – стержень (будущее отверстие), 2 – нижняя половинка формы, 3 – нижняя опока, 4 – крепление половинок формы, 5 – верхняя опока, 6 - верхняя половинка формы. На рис. 5.1, б изображена деталь, на рис. 5.1, в – стержень. На рис. 5.1, г изображены две половинки модели 7, а на рис. 5.1, д – стержневой ящик для изготовления стержней. На рис. 5.1, е представлена отливка, полученная после разрушения формы, где 8 – канал-стояк с литниковой чашей, 10 – шлакоуловитель, 9 – питатели, 11 – выпор.
Литература: [10].
Контрольные вопросы
1. Перечислить стадии техпроцесса литья?
2.Для чего нужен припуск, уклоны?
3. Что такое «знаки»?
4.Какие бывают формовочные и стержневые материалы?
5.Для чего служат добавки в смесь?
6. Если деталь – симметричное тело вращения, какой формы выполняется модель?
Основные способы ОМД
1. Прокатка – обжатие заготовки между вращающимися валками.
2. Прессование - продавливание заготовки, находящейся в замкнутой форме, через отверстие матрицы, давящим инструментом.
3. Волочение – протягивание заготовки, через сужающую полость матрицы (фильеры).
4. Ковка – изменяет форму и размеры заготовки путём последовательного воздействия инструмента на отдельные участки заготовки.
5. Штамповка – изменение формы и размеров заготовки с помощью специальных инструментов – штампов (для каждой детали – свой штамп, в отличие от ковки).
Виды штамповки:
Объёмная – металл заполняет полость штампа, приобретая её формы и размеры.
Листовая штамповка – получаются плоские и пространственные полые детали из заготовок, у которых толщина значительно меньше остальных размеров.
Лекция 7. Прокатка
План
7.1 Продукция прокатного производства
7.2 Инструмент и оборудование для прокатки
7.3 Технологический процесс производства основных видов проката
Прокатке подвергаются до 90% всей выплавляемой стали. При прокатке металл деформируется вращающимися валками. Взаимное расположение валков и заготовки, форма и число валков могут быть различными.
Три основных вида прокатки: продольная, поперечная и поперечно-винтовая.
Продольная: заготовка деформируется между валками, вращающимися в разные стороны и перемещается перпендикулярно к осям валков.
Поперечная: Валки, вращаясь в одном направлении, придают вращение заготовке и деформируют её. Валки могут сближаться, заготовка может подаваться сбоку.
Поперечно-винтовая прокатка: Валки вращаются в одну сторону и их оси расположены под углом друг к другу. За счёт этого заготовка вращается между ними и перемещается вдоль своей оси.
Лекция 8. Ковка, штамповка
План
8.1 Ковка
8.2 Штамповка
Ковка
Ковка – вид горячей обработки металла давлением, при котором металл деформируется с помощью универсального инструмента. Ковкой получают заготовки для последующей механической обработки – поковки.
Исходные заготовки: для крупных поковок – слитки до 320 тонн; для поковок среднего и малого веса – блюмы и сортовой проката квадратного или прямоугольного сечения.
Основные операции ковки:
Осадка – операция уменьшения высоты заготовки при увеличении площади её поперечного сечения.
![]() |
Протяжка – операция удлинения заготовки или её части за счёт уменьшения площади поперечного сечения. Выполняется последовательными ударами или нажатием на отдельные участки заготовки с подачей её вдоль оси протяжки и поворотом на 90 градусов относительно этой оси (т.е. кладут на бок). Получают удлинение и ликвидируют уширение. Протяжка имеет ряд разновидностей:
а) Разгонка – увеличение ширины части заготовки за счёт её толщины.
б) Протяжка с оправкой – операция увеличения длины пустотелой заготовки за счёт уменьшения толщины её стенок.
в) Раскатка на оправке – одновременное увеличение наружного и внутреннего диаметров за счёт толщины её стенок.
Прошивка – операция получения полостей в заготовке за счёт вытеснения металла. Получают сквозные и глухие отверстия.
Отрубка – отделение части заготовки по незамкнутому контуру путём внедрения в заготовку деформирующего инструмента – «топора».
Гибка – предание заготовке изогнутой формы по заданному контуру.
![]() |
Механическое удерживание земляных масс: Механическое удерживание земляных масс на склоне обеспечивают контрфорсными сооружениями различных конструкций...
Папиллярные узоры пальцев рук - маркер спортивных способностей: дерматоглифические признаки формируются на 3-5 месяце беременности, не изменяются в течение жизни...
Эмиссия газов от очистных сооружений канализации: В последние годы внимание мирового сообщества сосредоточено на экологических проблемах...
История развития хранилищ для нефти: Первые склады нефти появились в XVII веке. Они представляли собой землянные ямы-амбара глубиной 4…5 м...
© cyberpedia.su 2017-2024 - Не является автором материалов. Исключительное право сохранено за автором текста.
Если вы не хотите, чтобы данный материал был у нас на сайте, перейдите по ссылке: Нарушение авторских прав. Мы поможем в написании вашей работы!