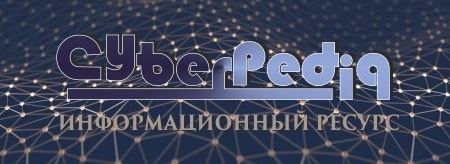
Археология об основании Рима: Новые раскопки проясняют и такой острый дискуссионный вопрос, как дата самого возникновения Рима...
Адаптации растений и животных к жизни в горах: Большое значение для жизни организмов в горах имеют степень расчленения, крутизна и экспозиционные различия склонов...
Топ:
Генеалогическое древо Султанов Османской империи: Османские правители, вначале, будучи еще бейлербеями Анатолии, женились на дочерях византийских императоров...
Отражение на счетах бухгалтерского учета процесса приобретения: Процесс заготовления представляет систему экономических событий, включающих приобретение организацией у поставщиков сырья...
Когда производится ограждение поезда, остановившегося на перегоне: Во всех случаях немедленно должно быть ограждено место препятствия для движения поездов на смежном пути двухпутного...
Интересное:
Аура как энергетическое поле: многослойную ауру человека можно представить себе подобным...
Распространение рака на другие отдаленные от желудка органы: Характерных симптомов рака желудка не существует. Выраженные симптомы появляются, когда опухоль...
Лечение прогрессирующих форм рака: Одним из наиболее важных достижений экспериментальной химиотерапии опухолей, начатой в 60-х и реализованной в 70-х годах, является...
Дисциплины:
![]() |
![]() |
5.00
из
|
Заказать работу |
|
|
1. Контроль качества работ по сварке монтажных соединений включает проверку:
- качества материалов и изделий, применяемых при устройстве соединений, и степени их соответствия проекту;
- соблюдения последовательности сварочных работ и технологии;
- качества выполненных соединений.
2. Сварочные материалы должны применяться проектных марок.
3. При осуществлении контроля за соблюдением технологии и последовательности работ особое внимание должно быть обращено на выполнение следующих требований:
- сварка должна производиться после проверки правильности установки элементов конструкции и положения соединяемых деталей;
- последовательность выполнения операций (порядок наложения сварных швов), а также общая последовательность устройства монтажных соединений в пределах сооружения, блоков, ярусов должна соответствовать указаниям технологических карт;
- работы по сварке монтажных соединений должны выполняться с соблюдением заданных режимов сварки ив отвечающих характеру работ условиях;
- сварка монтажных стыков должна выполняться сварщиками, прошедшими контрольные испытания.
4. Сварщик должен ставить личное клеймо на расстоянии 40-60 мм от границы выполненного им шва сварочного соединения. При выполнении сварного соединения несколькими сварщиками взамен постановки клейм допускается составление исполнительных схем с подписями сварщиков.
5. Контроль качества сварных соединений надлежит осуществлять методами, указанными в табл. 4.
Таблица 4
(СНиП 3.03.01-87, таблица 40)
Методы контроля | Тип конструкции, объем контроля |
1. Внешний осмотр с проверкой геометрических размеров и формы швов | Все типы конструкций в объеме; 100 % |
2. Контроль швов неразрушающими методами (радиографическими, ультразвуковыми и др.) | Все типы конструкций в объеме не менее 0,5 % длины швов |
3. Испытания на непроницаемость и герметичность | Конструкции (резервуарные и т. п.), методы и объемы контроля которых предусмотрены чертежами КМ |
4. Механические испытания контрольных образцов | Конструкции, для которых требования механических свойств сварных соединений предусмотрены чертежами КМ |
Для конструкций, работающих на динамические и усталостные нагрузки, для снижения концентрации напряжений и повышения их сопротивляемости хрупким разрушениям проекты КМ должны предусматривать дополнительные требования к контролю геометрических размеров швов, угла наклона образующей и радиуса сопряжения швов с основным металлом и угловых деформаций свариваемых элементов. Измерения производятся специальными шаблонами с точностью до ±0,1 мм.
|
6. Трещины всех видов и размеров в швах сварных соединений конструкций не допускаются и должны быть устранены с последующей заваркой и контролем.
7. По внешнему виду качество сварных соединений должно удовлетворять требованиям, изложенным в табл. 5.
Таблица 5
(СНиП 3.03.01-87, таблица 41)
Элементы сварных соединений, наружные дефекты | Требования к качеству, допустимые размеры дефектов |
1. Поверхность шва | Равномерно-чешуйчатая, без прожогов, наплывов, сужений и перерывов. Плавный переход к основному металлу (следует оговорить в чертежах КМ и КМД) |
2. Подрезы | Глубина -до 5 % толщины свариваемого проката, но не более 1 мм |
3. Дефекты удлиненные и сферические одиночные | Глубина - до 10 % толщины свариваемого проката, но не более 3 мм Длина - до 20 % длины оценочного участка* |
4. Дефекты удлиненные сферические в виде цепочки или скопления- | Глубина - до 5 % толщины свариваемого проката, но не более 2 мм |
Длина - до 20 % длины оценочного участка | |
Длина цепочки или скопления - не более удвоенной длины оценочного участка | |
5. Дефекты (непровары, цепочки и скопления пор) соседние по длине шва | Расстояние между близлежащими концами не менее 200 мм |
Примечание: * - длину табл. 7. оценочного участка следует принимать по табл 7. |
8. Контроль швов сварных соединений неразрушающими методами следует проводить после исправления недопустимых дефектов, обнаруженных внешним осмотром. Контролю должны подлежать преимущественно места с признаками дефектов и участки пересечения швов. Длина контрольного участка должна быть не менее 100 мм.
|
9. По результатам радиографического контроля швы сварных соединений должны удовлетворять требованиям, изложенным в табл. 6 и 7.
Таблица 6
(СНиП 3.03.01-87, таблица 42)
Элементы сварных соединений | Требования к качеству, допустимые размеры дефектов |
Соединения, доступные для сварки с двух сторон, соединения на подкладках | |
1. Непровары в корне шва | Высота - до 5 % толщины свариваемого проката, но не более 2 мм Длина - не более удвоенной длины оценочного участка |
Соединения без подкладок, доступные для сварки с одной стороны | |
1. Непровары в корне шва: | Высота - до 15 % толщины свариваемого проката, но не более 3 мм |
2. Удлиненные и сферические дефекты | |
одиночные | Высота - не более значений h |
образующие цепочку | Высота - не более 0,5h |
или скопление | Длина - не более длины оценочного участка |
удлиненные | Протяженность - не более отношения S/h |
непровары, цепочки и скопления пор, соседние по длине шва | Расстояние между близлежащими концами не менее 200 мм |
суммарные в продольном сечении шва | Суммарная площадь на оценочном участке - не более S |
Примечания: h - допустимая высота сферического или удлиненного одиночного дефекта; S - суммарная площадь дефектов в продольном сечении шва на оценочном участке Значения h и S следует принимать по табл. 7. |
При оценке за высоту дефектов h следует принимать размеры:
- для сферических пор и включений - диаметр;
- для удлиненных пор и включений - ширину.
Таблица 7
(СНиП 3.03.01-87, таблица 43)
Наименьшая толщина элемента конструкции в сварном соединении, мм | Длина оценочного участка, мм | Допустимые размеры одиночных дефектов | |
h, мм | S, мм2 | ||
От 4 до 6 | 0,8 | ||
Свыше 6 до 88 | 1,2 | ||
Свыше 8 до 10 | 1,6 | ||
Свыше 10 до 12 | 2,0 | ||
Свыше 12 до 14 | 2,4 | ||
Свыше 14 до 16 | 2,8 | ||
Свыше 16 до 18 | 3,2 | ||
Свыше 18 до 20 | 3,6 | ||
Свыше 20 до 60 | 4,0 |
В конструкциях, работающих на динамические нагрузки, допускаются отдельные поры или шлаковые включения диаметром до 1 мм для стали толщиной до 25 мм и не более 4 % толщины при
более 25 мм в количестве не более четырех дефектов на длине 400 мм. Особое внимание должно быть обращено на выявление дефектов в зонах высоких остаточных напряжений шириной:
|
= 4,55
- для стыковых соединений;
= 6,0
- для тавровых соединений;
= 3,5
- для угловых соединений, где
-толщина свариваемых элементов,
- катет шва.
10. По результатам ультразвукового контроля швы сварных соединений должны удовлетворять требованиям табл. 8.
Таблица 8
(СНиП 3.03.01-87, таблица 44)
Сварные соединения | Наименьшая толщина элемента конструкции в сварном соединении, мм | Длина оценочного участка, мм | Фиксируемая эквивалентная площадь одиночного дефекта, мм2 | Допустимое число одиночных дефектов на оценочном участке, шт. | |
наименьшая поисковая | допустимая оценочная | ||||
Стыковые | Свыше 6 до 10 | ||||
Угловые | Свыше 10 до 20 | ||||
Тавровые | Свыше 20 до 30 | ||||
Нахлесточные | Свыше 30 до 60 |
11. В соединениях, доступных сварке с двух сторон, а также в соединениях на подкладках суммарная площадь дефектов (наружных и внутренних) на оценочном участке не должна превышать 5 % площади продольного сечения сварного шва на этом участке. В соединениях без подкладок, доступных сварке только с одной стороны, - не более 10 %.
В случае обнаружения недопустимого дефекта следует выявить его фактическую длину, дефект исправить и вновь проконтролировать. При повторном выявлении дефекта контролю подлежит все сварное соединение.
12. Контроль непроницаемости швов сварных соединений следует, как правило, производить пузырьковым или капиллярным методами в соответствии с ГОСТ 3242-79. Величина разрежения при пузырьковом методе должна быть не менее 2500 Па (250 мм вод. ст.). Продолжительность контроля капиллярным методом должна быть не менее 4 ч при положительной и менее 8 ч при отрицательной температуре окружающего воздуха.
13. Контроль герметичности швов сварных соединений следует, как правило, производить пузырьковым методом.
|
14. Механические испытания контрольных образцов проводят при наличии требований в чертежах КМ к показателям прочности, пластичности и вязкости металла шва и зоны термического влияния сварного соединения. Число контрольных образцов и требования к их сварке аналогичны требованиям к пробным образцам (см. п. 4 «Общих положений» настоящего раздела).
Кроме того, производится испытание на статическое растяжение металла шва стыкового, углового и таврового соединений - по 3 образца.
Сварные соединения низколегированной стали проверяются на твердость металла шва и зоны термического влияния (не менее чем в четырех точках) - на одном образце.
15. Все ожоги поверхности основного металла сварочной дугой следует зачищать абразивным инструментом на глубину 0,5-0,7 мм. Ослабление сечения при обработке сварных соединений (углубление в основной металл) недолжно превышать 3 % толщины свариваемого элемента, но не более 1 мм.
Исправления сварных соединений зачеканкой не допускается.
|
|
Биохимия спиртового брожения: Основу технологии получения пива составляет спиртовое брожение, - при котором сахар превращается...
Кормораздатчик мобильный электрифицированный: схема и процесс работы устройства...
Автоматическое растормаживание колес: Тормозные устройства колес предназначены для уменьшения длины пробега и улучшения маневрирования ВС при...
Общие условия выбора системы дренажа: Система дренажа выбирается в зависимости от характера защищаемого...
© cyberpedia.su 2017-2024 - Не является автором материалов. Исключительное право сохранено за автором текста.
Если вы не хотите, чтобы данный материал был у нас на сайте, перейдите по ссылке: Нарушение авторских прав. Мы поможем в написании вашей работы!